Metal Parts Quality
Quality is an integral part. It can be defined as a standard of excellence or superiority. It measures how well something fulfills its intended purpose and meets customer expectations.
This includes factors such as durability, functionality, performance and design. It involves providing reliable, timely and efficient services. Providing high quality service is essential to building a loyal customer base and maintaining a good reputation.
Quality can be measured through various indicators such as reliability, performance and customer feedback. Quality can be measured through metrics such as customer satisfaction, response time and error rates.
Quality Definition
Systems Mangement
Quality systematic approach to identifying, controlling, and improving the quality of products or services that affect them.
Emphasis is placed on preventing problems from occurring rather than merely remedying them after they have occurred.
Continuous Improvement
The pursuit of higher quality standards through continuous improvement of processes and procedures, with all members involved in quality management activities. Make every member have quality consciousness.
Data Decision Making
Make decisions based on data and facts rather than intuition or guesswork. Focus on customer needs and expectations to ensure that products and services meet or exceed customer expectations.
Process Control
Monitor and control key processes to ensure process stability and predictability. Identify and evaluate risks that may affect quality, and develop appropriate preventive and countermeasure measures.
Quality Meaning
Increase customer satisfaction:
By ensuring the quality of products and services, customer satisfaction and loyalty can be increased, leading to increased repeat purchases and word-of-mouth recommendations.
Enhance market competitiveness:
High-quality products or services can help a company stand out in a competitive market and attract more customers.
Reduce costs:
Production costs and operating costs can be reduced by preventing errors and reducing rework.
Improve efficiency:
Optimizing processes and reducing waste can increase productivity and resource utilization.
Risk Management:
Potential losses and liabilities can be reduced by identifying and controlling risks that can affect quality.
Compliance Assurance:
Ensuring that products and services comply with relevant laws, regulations and industry standards avoids lawsuits and fines.
Continuous Improvement:
Quality management encourages a culture of continuous improvement, enabling the organization to progress and adapt to changes in the marketplace and technology.
Employee Involvement and Motivation:
By involving employees in quality management activities, you can increase their job satisfaction and loyalty, while stimulating their potential for innovation and improvement.
Brand image and reputation:
High-quality products and services help to build and maintain a favorable brand image and market reputation.
Market share growth:
By providing high quality products, companies can increase market share and attract new customers.
Supply chain management:
By managing quality in the supply chain, the efficiency and reliability of the entire supply chain can be ensured.
Customer Relationship Management:
Quality management helps to build and maintain good relationships with customers, which is essential for long-term business development.
Innovation and R&D:
A continued focus on quality can drive an organization to invest more resources in product development and innovation to meet market demands.
International market access:
Many international markets require products to meet specific quality standards, and quality management helps organizations enter these markets.
Employee Training and Development:
Quality management provides a framework through which employees can learn new skills and improve their personal career development.
Quality Assurance
- Quality Planning:
Determine quality objectives and requirements.
Develop quality policies and procedures.
Planning quality management system. - Supplier Management:
Evaluate and select qualified suppliers.
Monitor supplier performance.
Work with suppliers to improve quality. - Process control:
Define and optimize production and service processes.
Implement process monitoring and measurement.
Ensure process consistency and stability. - Review:
Conduct regular internal and external audits. Audit results are used to improve the quality management system.
- Product and Process Validation:
Verify that products and processes meet specified requirements.
This includes design validation, process validation and product validation. - Quality Training:
Provide necessary training to improve the quality awareness and skills of employees. - Improve:
Continuously improve product and service quality. Use methods such as the PDCA (Plan-Do-Check-Act) cycle. - Customer Feedback:
Collect and analyze customer feedback.
Improvement of products and services based on feedback. - Data Analysis:
Collect and analyze quality-related data.
Use statistical tools to analyze data.
- Risk Management:
Identify and assess risks that may affect quality.
Develop risk mitigation measures. - Compliance:
Ensure products and services comply with all relevant laws, regulations and standards. - Documentation and Records Management:
Maintain quality related documents and records.
Ensure accuracy and traceability of documentation. - Control:
Inspecting and testing products to ensure quality standards are met. This includes incoming inspection, in-process inspection and final product inspection. - Corrective and Preventive Action:
Takes corrective action for identified quality problems.
Prevent potential quality problems.
Quality Control
Statistical Process Control (SPC):
The use of statistical techniques to monitor production processes to identify and control process variation.
Sample Inspection:
Randomly selecting a sample from the total for inspection to infer the quality of the entire batch.
Whole lot inspection:
Inspection of all products to ensure that each unit meets quality standards.
Process Capability Analysis:
Evaluating the ability of a manufacturing process to consistently produce a product that meets specifications.
Quality Audit:
An independent assessment of an organization’s quality management system to ensure that it meets standards and regulatory requirements.
Continuous Improvement:
Continuously identifying improvement opportunities to enhance product quality and process efficiency.
Process Validation:
Ensures that the manufacturing process consistently produces a product that meets specifications.
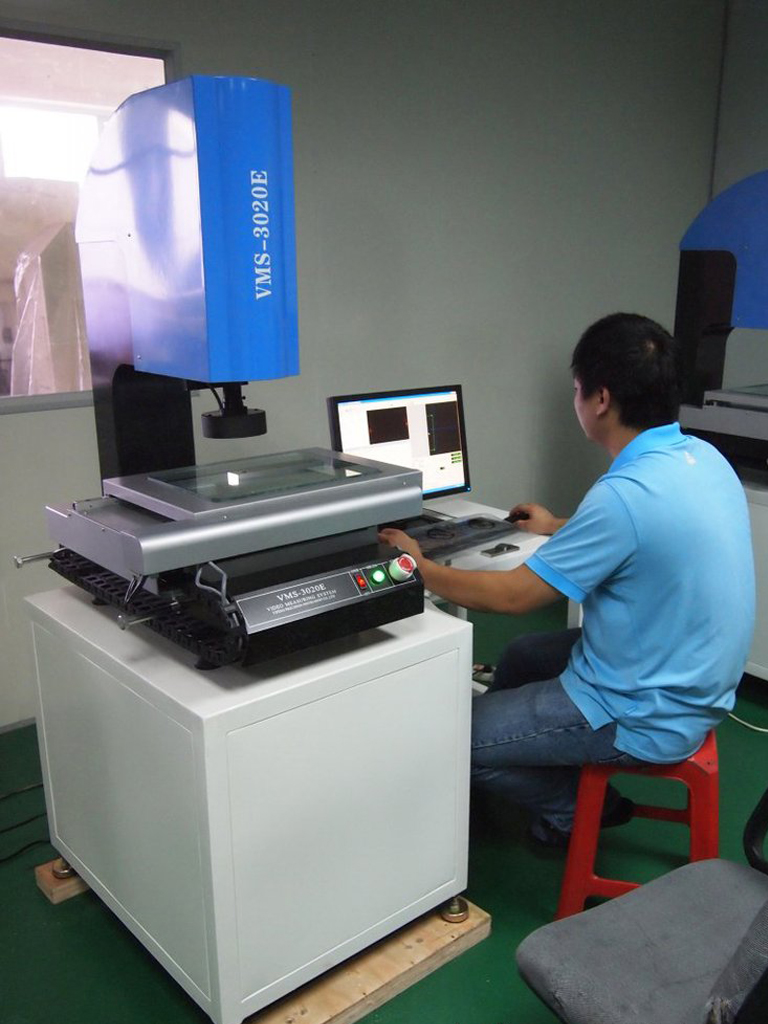
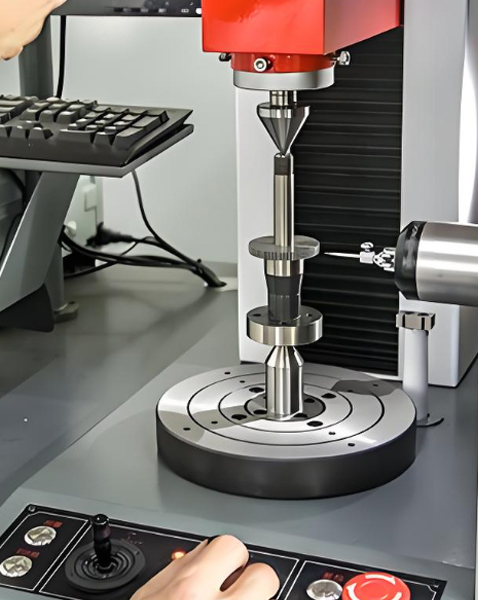
Quality policy
objective setting:
Define the quality objectives and requirements for the product or service, which should be consistent with market needs and the competitive environment to ensure that the product or service meets customer expectations
Planning:
Formulate specific strategies and plans for achieving quality objectives, including determining the organizational structure of quality management, developing quality management processes and standards, etc.
Control:
Monitoring and controlling the quality of a product or service during its development, including sampling, testing and evaluating raw materials, production processes and final products to ensure that the quality of the product meets quality standards and customer needs.
Management System:
Establish an applicable quality management system, including organizational structure, division of responsibilities, workflow, etc., in order to ensure that the product or service is effectively controlled and supervised during development, production, and delivery.
Improvement:
Improving the quality level of products or services through continuous quality management activities, including identifying quality problems by analyzing quality data and customer feedback, and taking appropriate improvement measures.
Quality Planning
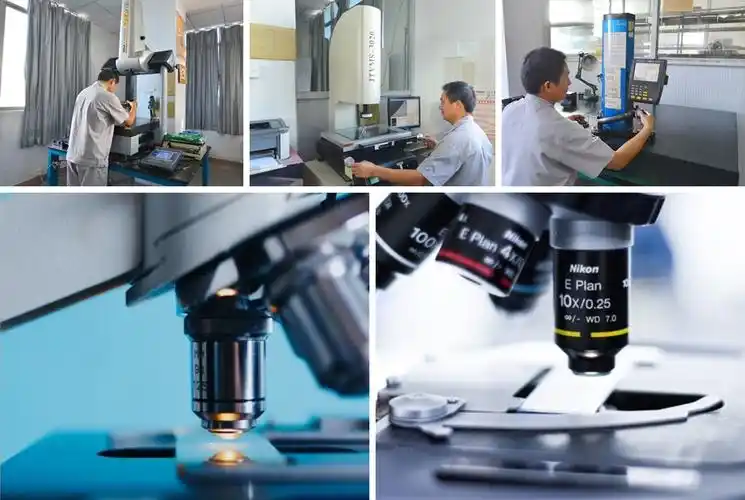
With decades of proven experience, our team is prepared to help you achieve your goals and beyond.
All Hands on Deck
The values, attitudes, behaviors, and beliefs that implement quality. Involves how the organization defines, understands, and pursues quality, as well as its commitment to quality through daily decision-making.
Manufacturing Quality
A strong quality culture improves organizational efficiency and effectiveness, enhances customer trust, improves market competitiveness, and contributes to the long-term success of the organization.
Quality Definition
1
Prevention Costs
Including quality management activities and administrative costs, quality improvement measures, quality education and training costs, new product review costs, quality information costs and process control costs.
2
Appraisal Costs
Used to assess whether the product meets the specified requirements of the costs. This includes departmental administrative costs, materials, processes and finished product inspection costs, testing equipment maintenance costs.
3
Internal Failure Costs
Products do not meet the requirements before leaving the factory to pay the costs, such as waste loss, repair costs, downtime losses and re-inspection costs.
4
External Failure Costs
After the product does not meet the requirements of the factory, resulting in claims, repairs, replacement or loss of reputation and pay the cost.