Yield strength and tensile strength are the two most important properties of steel, which directly affect the safety and life of the product. However, many people cannot distinguish between the true meaning and the difference between the two. This article will explain the performance, application, and difference between these two types of steel in detail.
The tensile strength of steel refers to the maximum stress value that the material can withstand in a tensile test, that is, the value obtained by dividing the maximum tensile force that the material can withstand before breaking by the original cross-sectional area. It represents the ability of steel to resist tensile fracture and is an important indicator for measuring the mechanical properties of steel.
The yield strength of steel refers to the stress value at which the steel begins to undergo permanent deformation under tensile load. In simple terms, it is the maximum “safe” stress that the steel can withstand. If this value is exceeded, the steel will undergo irreversible plastic deformation and cannot return to its original shape.
Key Takeaways
- Yield strength and tensile strength are both important in choosing safe and strong steel. The stress-strain curve shows the yield strength at which the steel begins to deform permanently. It also shows the tensile strength at which the steel eventually breaks. Engineers use these two values to check the strength and safety of steel. Research shows that the yield strength of most steels is usually between 100 MPa and 1000 MPa.
Table of Contents
Difference Between Yield Strength and Tensile Strength
Key Distinction
You need to understand the main difference between yield strength and tensile strength when you work with steel. Yield strength tells you the point which steel starts to bend or stretch and does not return to its original shape. Tensile strength shows you the maximum force steel can handle before it snaps or breaks.
Think of yield strength as the warning sign. When you reach this point, the steel will not go back to its old shape. Tensile strength is the final limit. If you keep pulling, the steel will break apart.
Researchers have tested different types of steel, such as 1018, 4140, and 6150. They found that yield strength is always lower than tensile strength. For example, in one study, the average yield strengths were 73 Ksi, 137 Ksi, and 204 Ksi for these steels. The tensile strengths were higher at 83 Ksi, 149 Ksi, and 219 Ksi. This shows a clear difference between yield strength and tensile strength. No matter the steel type, yield strength marks the start of permanent change, while tensile strength marks the breaking point.
You can see this difference in numbers, too. Mild steel has a yield strength of around 250 MPa, but its tensile strength can reach 400 to 700 MPa. High-strength steels can have yield strengths over 600 MPa and tensile strengths over 1000 MPa. These numbers prove that the difference between yield strength and tensile strength is real and important.
Plastic Deformation vs Fracture
When you pull on a piece of steel, it first stretches a little and then returns to its shape. This is called elastic deformation. If you pull harder and reach the yield strength, the steel starts to change shape forever. This is plastic deformation. The steel will not return to its original form, even if you stop pulling.
If you keep pulling past the yield strength, the steel will stretch more and more. When you reach the tensile strength, the steel cannot take any more force. It breaks apart. This is called a fracture.
- Scientists have found that plastic deformation begins at very small strains, often between 0 and 1%. At this stage, the steel’s inside structure starts to change.
- Fracture happens later, when the steel has stretched as much as it can. The way the steel breaks can show if it failed in a brittle or ductile way.
- In tests, steel samples often show a “cup and cone” shape after breaking, which means they failed in a ductile way at the tensile strength point.
Yield Strength of Steel
Yield Strength Definition
You need to know what yield strength means before you can use steel safely. Yield strength tells you the maximum load a piece of steel can handle before it changes shape forever. If you pull or push on steel and stay below this limit, the steel will snap back to its original form. Go past this point, and the steel bends or stretches for good.
Gibbs Interwire, a trusted expert in metals, explains that yield strength is the highest load a material can take before it gets a permanent set. ScienceDirect also says that yield strength is the stress which plastic deformation starts in a metal. This point marks the change from elastic behavior, where steel returns to its shape, to plastic behavior, where it does not.
How Yield Strength Is Measured
You can measure yield strength in a few ways. The most common measures of strength use a tensile test. In this test, you pull a steel sample until it stretches and then breaks. The machine records how much force the steel can take at each step.
The yield strength is the point which the steel starts to bend and does not return to its original shape. Some labs use a newer method called instrumented indentation testing (IIT).
This test presses a hard tip into the steel and measures how the steel reacts. Studies show that IIT gives results that match the classic tensile test. Both methods help you find the true yield strength of steel, so you can trust the numbers when you choose materials for your project.
Yield Point on Stress-Strain Curve
When you look at a stress-strain curve, you see how steel reacts to force. The curve starts with a straight line. This part is the elastic region. Here, stress and strain rise together, and the steel returns to its shape when you remove the load.
The end of this straight line is the yield point. At the yield point, the steel begins to stretch without needing more force. For mild steel, you often see an upper and lower yield point. These points show where plastic deformation starts. After the yield point, the curve bends, and the steel will not return to its original shape.
If the curve does not show a clear yield point, you can use the offset method. Draw a line parallel to the elastic part of the curve, but move it over by a small amount (usually 0.2%). Where this line meets the curve, you find the yield strength. This method helps you find the yield strength even when the curve is not clear.
Tip: Always check the yield point on the stress-strain curve before using steel in a project. This step helps you avoid permanent damage and keeps your work safe.
Tensile Strength of Steel
Tensile Strength Definition
Tensile strength shows how much force steel can withstand before breaking. When you pull steel, it stretches a little. If you keep pulling, it will reach its limit. This limit is called tensile strength. You need to know this so the steel does not snap in use. Many jobs need strong steel to keep things safe. For example, bridges, planes, and cars all use steel that must hold up under big forces.
Note: Tensile strength of steel is the most stress it can take before breaking. This number helps you pick the right steel for your project or tells you if you need something stronger.
Many jobs need steel with high tensile strength:
- Construction uses it for bridges and tall buildings.
- Aerospace needs it for parts in planes and rockets.
- Car makers use it for frames and safety parts.
- Wind turbines need it for their blades.
- Ships and sea buildings use it for strength in water.
Measuring Tensile Strength
You find tensile strength by doing a special test. First, you make a steel sample shaped like a dog bone. You put the sample in a testing machine. The machine pulls on the steel until it breaks apart. You write down the force and how much it stretches. The biggest force before it snaps is the tensile strength. You get the value by dividing the force by the sample’s starting area. The answer is in units like megapascals (MPa).
Here is an easy way to see the steps:
- Make a standard steel sample.
- Put the sample in the test machine.
- Pull the sample with more and more force.
- Write down the force and how far it stretches.
- Find the biggest force before it breaks.
- Divide the force by the area to get tensile strength.
Most labs use rules like ASTM E8 to make sure tests are fair. The test also gives you other numbers, like yield strength and how much steel can stretch before it breaks.
Ultimate Tensile Point
The ultimate tensile point is the highest spot on the stress-strain curve. At this spot, steel holds the most force it ever can. After this, the steel gets thinner in one place. This is called necking. Soon after, the steel breaks apart. This point is very important for engineers. It shows the top limit for tensile strength of steel. If you build a bridge or a building, you must keep forces below this point.
Here is a table to help you see the difference between tensile strength and yield strength:
Property | Tensile Strength | Yield Strength |
---|---|---|
Measurement point | At fracture (maximum stress before breaking) | At permanent deformation (start of plasticity) |
Stress level | Higher value than yield strength | Lower value than tensile strength |
Role in design | Defines the maximum load before catastrophic failure | Defines the maximum load before permanent deformation |
Accuracy | Can be calculated with 100% accuracy | Requires proof stress for ductile materials |
Stress-Strain Curve
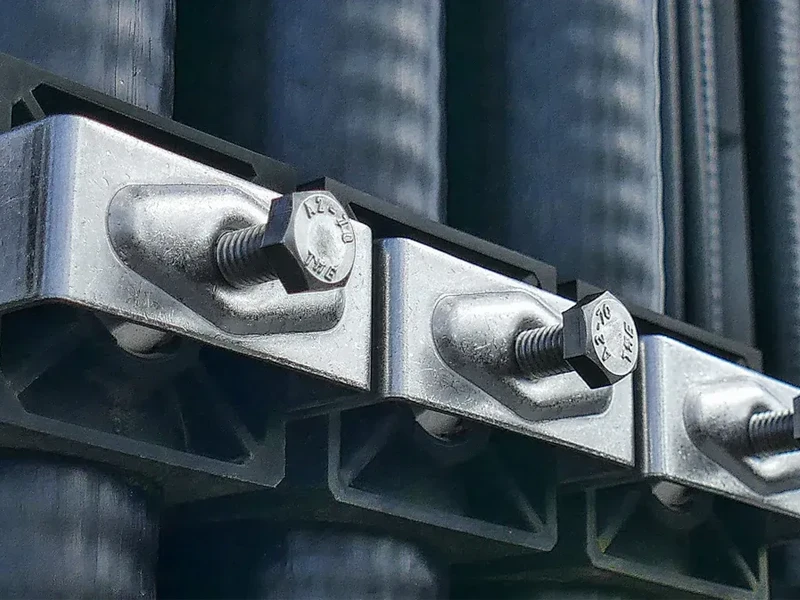
Overview
When you test steel, you often use a stress-strain curve to see how it behaves under force. This curve comes from a tensile test, where you pull a steel sample and measure how much it stretches before it breaks. The stress-strain curve shows you every stage of steel’s response, from the first stretch to the final snap.
You start in the elastic region. Here, steel stretches a little and returns to its original shape when you let go. This part of the curve is a straight line. Next, you reach the yield point. At this stage, steel begins to change shape forever. The curve bends, showing the start of plastic deformation. As you keep pulling, the steel enters the plastic region. It stretches more, and the curve rises, but not as steeply. You may notice strain hardening, where steel gets stronger as it stretches. After this, the curve reaches its highest point, called the ultimate tensile strength. Past this point, the steel gets thinner in one spot, a process called necking. Soon after, the steel breaks.
The stress-strain curve gives you a complete picture of steel’s strength and flexibility. You can see how much force steel can take before it bends or breaks.
Experimental graphs from tensile tests best show the full stress-strain curve for steel. These graphs reveal all the important regions: elastic, plastic, strain hardening, necking, and fracture. Scientists use these curves to study how different steels perform. For example, hot rolled and cold rolled steels show different curves because of how they are made.
The stress-strain curve also helps you compare different types of steel. Look at the chart below. It shows test results for A36 mild steel and C1018 hard steel. You can see differences in ductility, strength, and how much each steel can stretch before breaking.
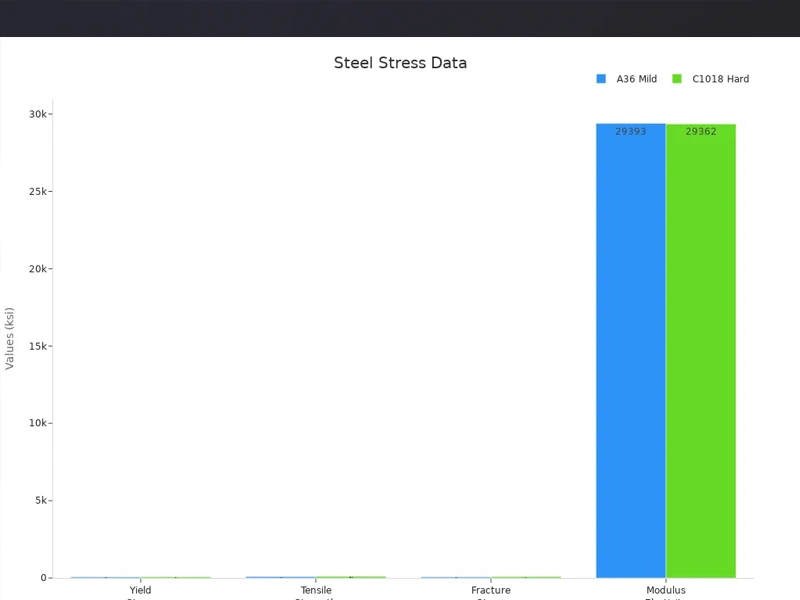
This chart shows that A36 steel can stretch more before breaking, while C1018 steel is stronger but less ductile. These differences matter when you choose steel for buildings, bridges, or cars.
Yield Point vs Ultimate Point
On the stress-strain curve, two points stand out: the yield point and the ultimate tensile point. You need to know what each means.
- The yield point marks where steel starts to bend or stretch permanently. If you stay below this point, steel returns to its shape. Go past it, and you get a permanent change. This is where yield strength comes in.
- The ultimate point is the highest spot on the curve. Here, steel holds the most force it ever can. This is the tensile strength. After this, steel gets weaker and soon breaks.
You can use these points to judge how safe and strong your steel is. For example:
- If you design a bridge, you want to keep the stress below the yield strength so the steel does not bend.
- If you build a car, you want steel with high tensile strength so it can handle crashes without snapping.
The stress-strain curve helps you see both points. You can spot the yield point as the curve starts to bend. The ultimate point is the peak of the curve. These points guide you in picking the right steel for your job.
Remember: The yield point tells you when steel starts to change forever. The ultimate point tells you the most force steel can take before breaking. Both are key for safe and smart engineering.
Comparison
Table of Differences
You can see the main differences between yield strength and tensile strength by looking at them side by side. This table helps you compare their definitions, how you measure them, and what they mean for steel:
Aspect | Yield Strength | Tensile Strength |
---|---|---|
Definition | Force causing permanent deformation (onset of plasticity) | Force causing material to break (maximum stress before failure) |
Stress Measurement | Minimum stress to cause permanent deformation | The maximum stress material can withstand before breaking |
Position on Stress-Strain Curve | Always lower value, appears first (elastic to plastic transition) | Always lower value appears first (elastic to plastic transition) |
Intermolecular Forces | Stronger than the applied stress at the yield point | Weaker than applied stress at tensile point |
You can also compare real numbers for different steels:
Metal Type | Yield Strength (MPa) | Ultimate Tensile Strength (MPa) |
---|---|---|
Steel (A36) | 250 | 400 – 550 |
Stainless Steel (304) | 215 | 505 |
This side-by-side view shows that yield strength always comes before tensile strength on the stress-strain curve. Yield strength tells you when steel starts to bend for good. Tensile strength tells you the maximum force a steel can take before it breaks.
Behavior Under Load
When you load steel, it reacts in different ways depending on the force. Here is what happens:
- Yield strength marks the point where steel starts to bend and will not return to its original shape. This point is sensitive to the steel’s microstructure, like grain size and what elements are mixed in.
- If you keep loading the steel, it stretches more. Tensile strength is the highest force the steel can handle before it snaps. Changes in the steel’s makeup, like how much carbon or manganese it has, can change how it behaves at both points.
- Yield strength depends a lot on the grain boundaries inside the steel. If you add things like carbon, you can make the steel stronger at the yield point, but it might become less stretchy.
- Tensile strength depends more on things like how many carbides are in the steel. If you change these, you might lower the tensile strength without changing the yield strength much.
Engineering Relevance
You use both the yield strength and the tensile strength of steel when you design safe and strong structures. Here is why they matter:
- Yield strength helps you make sure steel parts do not bend or change shape when you use them. You want bridges, buildings, and machines to keep their shape under normal loads.
- Tensile strength helps you avoid sudden breaks. You need this for things like cables, beams, and bolts that must not snap under heavy loads.
- Engineers pick steel grades based on these strengths. For example, high-rise buildings use steel with high yield strength to stay upright. Bridges use steel with high tensile strength to handle heavy traffic and wind.
- In cars, you want body panels to bend a little (high yield strength) but not break (high tensile strength). In airplanes, you need both strengths to keep parts safe during flight.
- Real-life failures, like the Tacoma Narrows Bridge collapse, show why you must understand both strengths. Using the right steel keeps people safe and saves money.
Always check these two material properties of yield strength and tensile strength when you choose steel for any project. This step helps you build things that last and keep people safe.
Importance
Material Selection
When you choose steel for a project, you need to know both the yield strength and tensile strength. Yield strength tells you the point which steel starts to bend and does not return to its original shape. Tensile strength shows you the maximum force steel can take before it breaks. These two numbers help you pick the right steel for the job.
If you work on a building or a bridge, you want steel that will not bend or break under heavy loads. For low-stress jobs, you can use steel with lower yield and tensile strength. For high-stress or high-impact jobs, you must pick steel that has higher values. This choice keeps your project safe and strong.
Engineers use the stress-strain curve to see how steel behaves under force. This curve helps you predict if the steel will hold up or fail. You can use this information to make smart choices about durability, safety, and cost. For example, in construction, you need steel with enough yield strength to support the weight of the building and resist wind or earthquakes. In cars and planes, you need steel that will not snap under sudden forces.
Tip: Always check both yield strength and tensile strength when you select steel. This step helps you avoid costly mistakes and keeps your project safe.
Safety
Safety depends on knowing the strength of your steel. If you use steel with the wrong yield or tensile strength, your structure could bend or break. This risk can lead to accidents or even disasters. You must match the steel’s strength to the job’s needs.
Here is a table that shows how different types of steel are used for safety in real-world projects:
Steel Type | Yield Strength Range (MPa) | Application and Safety Relevance |
---|---|---|
Mild Steel (Low Carbon) | 200 – 350 | Used in non-load-bearing structures; lower strength needs safety factors to prevent permanent bending. |
Medium Carbon Steel | 350 – 450 | Used for shafts and gears; strength data ensures safe operation under stress. |
High Carbon Steel | 600 – 700 | Used in cutting tools and springs; high yield strength is key for safe performance under load. |
Stainless Steel | 200 – 700 | Used in many areas; strength data helps balance safety and corrosion resistance. |
Tool Steel | 500 – 2200 | Used for tools; high strength is vital for safety and performance. |
Maraging Steel | 1400 – 2400 | Used in aerospace and defense; exact strength data is critical for safety. |
Performance
Yield strength and tensile strength also affect how well steel performs in different jobs. You want steel that can handle the forces it will face every day. Many industries rely on these properties to make sure their products work as planned.
- Construction: High-tensile steel cables in bridges, like the Golden Gate Bridge, support heavy loads and keep the structure safe.
- Aerospace: Airplane wings and landing gear use steel with high yield and tensile strength to handle strong forces during flight.
- Automotive: Car frames use high-strength steel to protect you in a crash.
- Medical Devices: Stents need steel that bends but returns to shape, so they work inside your body.
- Manufacturing: Steel beams and machines need the right strength to last and work well.
- Oil and Gas: Drilling and pipelines use steel that can handle high pressure and tough conditions.
You can see that yield and tensile strength are not just numbers. They shape how steel works in the real world. When you understand these strengths, you can choose the best steel for safety, reliability, and top performance.
Using Strength Data
Reading Specifications
You need to know how to read steel specifications before you can use strength data. Steel specifications tell you what kind of steel you have and what it can do. Most engineers use standards from ASTM, a group that sets rules for materials like steel. ASTM codes use a letter and a number. For example, “A36” means a type of steel for building. The letter “A” stands for ferrous metals, which include steel.
When you look at a steel specification, you might see several types of ASTM standards:
- Specification: Lists the required properties for the steel.
- Test Method: Explains how to test the steel.
- Classification: Groups steels by type.
- Practice: Gives steps for using or testing steel.
- Guide: Offers advice for choosing or using steel.
- Terminology: Defines words used in the standards.
You should also know that ASTM standards focus on the properties of the steel, not just what it is made of. This helps you find the right steel for your job, even if the chemical makeup changes a little. ASTM standards make sure steel is strong, safe, and works the same way every time.
Here is a table that shows how engineers use different mechanical properties in practice:
Mechanical Property Category | Description | Role in Engineering Practice |
---|---|---|
Tensile Properties | Includes tensile strength, yield strength, elongation, and reduction of area | Guide material selection and quality checks |
Impact Properties (Toughness) | Measured by energy absorbed in impact tests | Show how well steel resists breaking |
Fatigue Properties | Show how steel holds up under repeated loads | Help predict how long steel will last |
Hardness and Hardenability | Measure resistance to dents and how deep hardness goes after heat treatment | Affect performance and design choices |
Tip: Always check the ASTM code and the mechanical properties listed in the specification. This helps you pick steel that meets your needs and follows safety rules.
Choosing Steel
You need to choose steel that matches your project’s needs. Start by looking at the strength data in the specification. The most important numbers are tensile strength, yield strength, elongation percent, reduction in area percent, and hardness. These numbers tell you how much force the steel can take, how much it can stretch, and how tough it is.
Engineers use a step-by-step process to pick the best steel:
- Check the strength data for each steel grade.
- Compare the numbers to what your project needs.
- Look at how the steel was treated, like quenching or tempering.
- Pick the steel grade and heat treatment that gives you the best mix of strength, toughness, and cost.
You can use a method called multi-criteria decision making. This method helps you weigh each property, like strength and hardness, so you do not just pick the strongest steel but the one that fits your job best. For example, if you build a bridge, you want steel with high yield strength and good toughness. If you make tools, you might need higher hardness.
Common Misconceptions
Yield Strength vs Hardness
Many people think yield strength and hardness mean the same thing. You might see a high hardness number and believe the steel is always strong. This is not true. Yield strength tells you how much force steel can take before it bends for good. Hardness measures how well steel resists dents or scratches.
- Hardness depends on several things, like yield strength, tensile strength, and elastic modulus.
- You can find a loose link between yield strength and hardness, but the connection is not strong. The numbers often scatter when you compare them.
- Tensile strength matches up better with hardness, but even then, you cannot swap the numbers directly.
- When you test yield strength or tensile strength, you get results that are very close to the true value—within about 1%. Hardness tests can change a lot because of different machines, how people run the test, or even small changes in the steel.
- Hardness tests are less reliable for finding out how strong steel is. You should use yield strength tests for better accuracy.
Tip: Do not use hardness as a shortcut for yield strength. Always check the real yield strength if you want to know how much force steel can take before it bends.
Tensile Strength vs Toughness
You may also think tensile strength and toughness are the same. They are not. Tensile strength is the highest force steel can take before it breaks. Toughness is the total energy steel can absorb before it snaps. You find toughness by looking at the whole area under the stress-strain curve from a tensile test.
Toughness depends on both strength and ductility. For example, a steel with high strength but low ductility can have the same toughness as a steel with lower strength but higher ductility. You see this when you compare different steels. Some steels stretch a lot before breaking, while others break quickly but hold more force. Both can absorb similar amounts of energy before they fail.
Researchers use special tests to measure these properties. Tensile tests show you the maximum stress steel can handle. Impact tests, like the Charpy test, show how much energy steel can absorb before breaking. These tests prove that tensile strength and toughness are not the same. Toughness tells you how steel acts under sudden hits or crashes, while tensile strength only shows the breaking point under slow pulling.
Remember: High tensile strength does not always mean high toughness. Always check both values when you need steel for safety or impact resistance.
Common Myths About Steel Strength
You might hear that billet aluminum is always stronger or more durable than steel. This is not true. Look at the table below:
Property | Billet Aluminum | Steel (Carbon & Stainless) |
---|---|---|
Density | Much lower (lighter) | Much higher (heavier) |
Tensile Strength | Moderate (270–700 MPa) | Higher (520–850 MPa) |
Wear Resistance | Moderate | High (especially hardened steel) |
Fatigue Resistance | Moderate | High |
Corrosion Resistance | Excellent | Varies (good in stainless steel) |
You can see that steel often has higher tensile strength, better wear resistance, and better fatigue resistance. Steel works better for heavy loads and repeated use. Advanced high-strength steels can even match or beat aluminum’s strength-to-weight ratio.
Summary
Key Takeaways
You have learned the core differences between yield strength and tensile strength of steel. These two properties help you understand how steel behaves under force and why it matters for safety and design.
- Yield strength tells you when steel starts to bend and does not return to its original shape.
- Tensile strength shows the maximum force a steel can take before it breaks.
- You use both values to choose the right steel for buildings, bridges, cars, and many other projects.
- Yield strength usually comes first on the stress-strain curve, while tensile strength is the highest point before fracture.
- When you increase the speed of loading (strain rate), both yield and tensile strength go up, but steel becomes less stretchy and more likely to break suddenly.
Remember: Yield strength is your warning sign. Tensile strength is the final limit. Both keep your designs safe and strong.
Key Numbers and Facts
You can see how different types of steel react to changes in strain rate and loading. The table below shows some important results:
Steel Type | Strain Rate (1/s) | Yield Strength Increase (%) | Fracture Behavior | Notes |
---|---|---|---|---|
St37 | 0.001 to 0.1 | 30% | Ductile at low rate, brittle at high rate | Yield strength very sensitive to strain rate |
St52 | 0.001 to 0.1 | 6% | Similar to St37 | Less sensitive than St37 |
A36 (annealed) | ~0.01 | 27% | N/A | Room temperature data |
A36 | 1 | 45% | N/A | Higher strain rate, higher yield strength |
A36 | 10 | 65% | N/A | Very high strain rate |
A572 | 10 | 40% | N/A | Higher strength steel |
You should also know that the elastic modulus of ST37 steel is about 210 GPa, and Poisson’s ratio is around 0.3. These numbers help you predict how steel will stretch and compress under load.
Practical Insights
- You can estimate ultimate tensile strength from yield strength with about 80% accuracy using regression models.
- Yield strength also helps you predict the yield-to-tensile ratio with about 65% accuracy.
- Welded steel zones behave differently. The base metal has the highest sensitivity to loading speed, while the weld metal is the strongest but less sensitive.
Tip: Always check both yield and tensile strength before you pick steel. These numbers help you avoid costly mistakes and keep your projects safe.
You now have the key facts to make smart choices about steel strength. Use these takeaways to guide your next project and ensure safety, performance, and reliability every time.
You now understand that yield strength tells you when steel bends and does not go back, while tensile strength is the point where steel breaks. Both numbers are important for safe building. Studies found that yield strength changes a lot with small stretches, so it is harder to measure. Tensile strength does not change as much. Important research shows:
- Yield strength is 17–19 times more affected by small stretch changes than tensile strength.
- Using chemical information helps make better guesses for both numbers.
- Tensile strength tests give more steady and trusted results.
FAQ
Accordion content.
Yield strength tells you when steel starts to bend and does not return to its original shape. Tensile strength shows the maximum force a steel can take before it breaks. You need both numbers to pick safe and strong steel.
You use yield strength to stop steel from bending. You use tensile strength to stop steel from snapping. Both help you design safe bridges, buildings, and machines.
Yes! You can heat-treat steel or add elements like carbon or manganese. These changes make steel stronger. You should always check the new strength values after any treatment.
Not always. High tensile strength helps steel resist breaking. Sometimes you need steel that bends a little before breaking. You must match the steel’s strength to your project’s needs.
You pull a steel sample in a machine until it bends or breaks. The machine records the force. You find the yield strength at the first permanent bend. You find tensile strength at the breaking point.
No. Yield strength measures when steel bends for good. Hardness measures how well steel resists dents or scratches. You need both tests for a full picture of steel’s properties.
If you use steel with low ductility or load it too fast, it can snap suddenly. You should always check both yield and tensile strength to avoid sudden failures.
You find strength data in steel specifications, like ASTM standards. These documents list yield strength, tensile strength, and other key properties. Always read the specs before you choose steel.