Spray
Spray color, make the world more wonderful! AF Industrial Co., Ltd. spray services, with superb skills and a deep understanding of color, to ensure that every spray to meet your product needs.
Spraying Process
Spraying is a coating method by spraying gun or dish atomizer, with the help of pressure or centrifugal force to disperse the paint into fine droplets, evenly coated on the surface of the coated object. It can be divided into air spraying, airless spraying, electrostatic spraying and other forms, widely used in metal painting, automobile manufacturing and other fields.
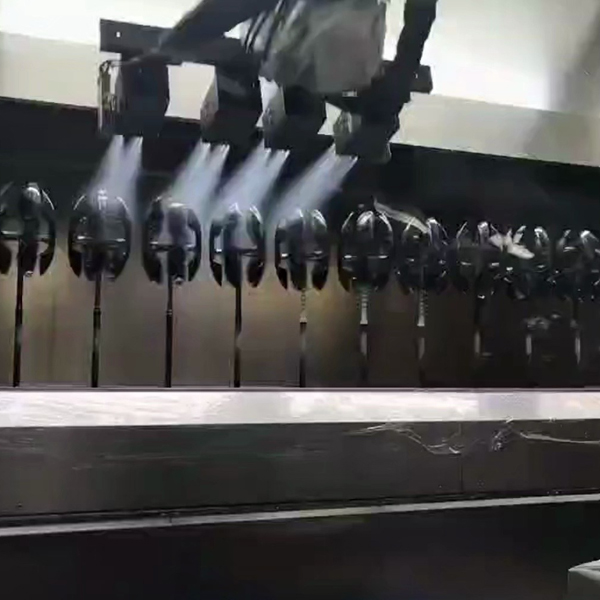
Cleaning and Pretreatment
The workpiece is cleaned and pre-treated. This includes steps such as feeding, pre-degreasing, degreasing, and washing to ensure that the surface of the workpiece is clean and free of impurities. After cleaning, the workpiece is passivated and then dried and cooled.
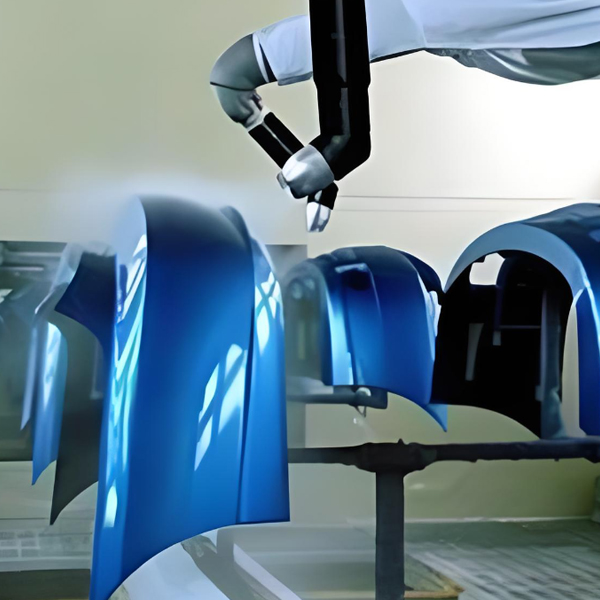
Spray
The workpiece is mounted on the support table of the coating line for spraying. This step is the heart of the spraying process and the workpiece is sprayed with the desired paint.
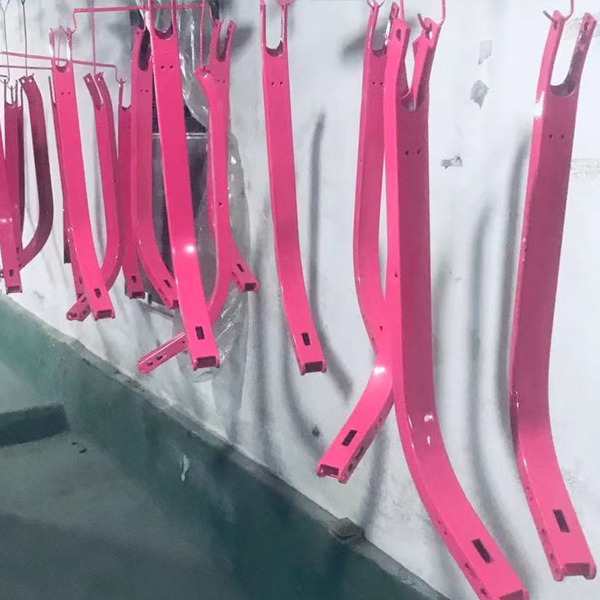
Drying and Curing
The workpiece needs to be dried and cured. This usually includes pre-drying, drying, cooling and other steps to ensure that the paint can cure sufficiently to form a strong coating.
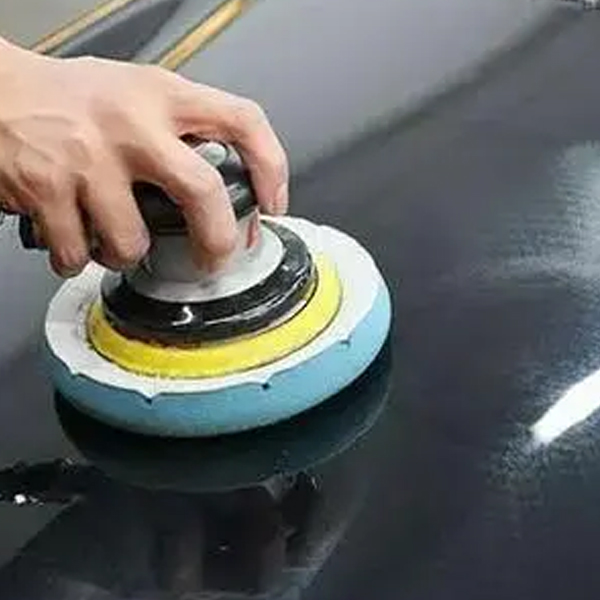
Aftertreatment
The sprayed workpiece will undergo post-treatment, including waxing and polishing, to improve the finish and beauty of the surface.
Customized Spraying Service
AFI Industries Ltd. provides customized spraying services for customers. We provide customers with common paints, special paints, waterborne coatings and self-spraying coatings to provide customers with a full range of personalized choices from color, gloss, texture to pattern to meet the beauty of the product and surface protection, so as to meet the needs of customers.
About Spraying
Before spraying, the surface of the object needs to be thoroughly cleaned and pre-treated, including the removal of oil, rust and old paint, as well as sanding and rough treatment to ensure the adhesion and uniformity of the coating. After spraying, the coating forms a uniform and smooth protective film, which not only enhances the beauty of the object, but also provides protection against corrosion, rust and wear, significantly improving the durability and appearance of the product.meet the quality needs of customers.
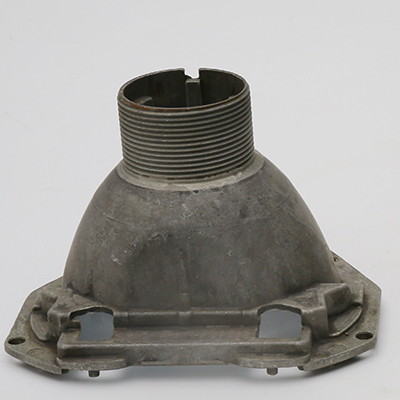
Before Spraying
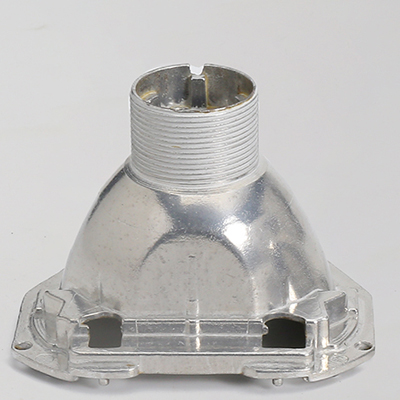
After Spraying
Spraying Equipment
Spraying equipment is used in the painting industry to evenly spray paint on the surface of the object equipment, they are diverse, suitable for different application scenarios and needs. AFI Industries Co., Ltd. has a wide range of spraying equipment to meet the needs of customers for spray type, spray area and coating quality.
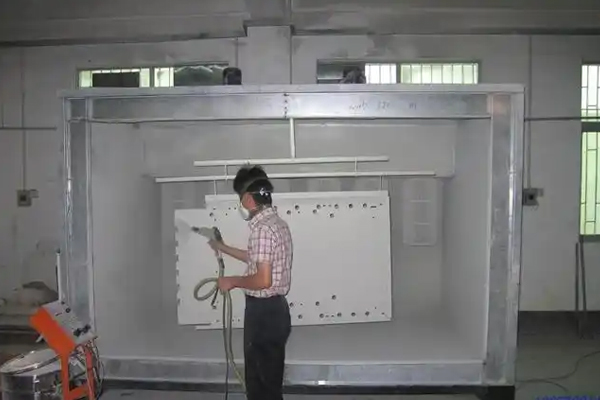
Hand Gun
Manual spray guns are flexible and suitable for use on surfaces of various sizes and shapes.
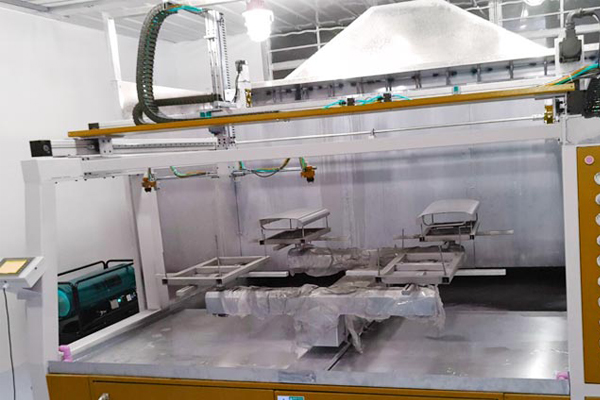
Automatic spraying equipment
Automatic spraying equipment is an efficient and accurate painting technology that is widely used in many industries.
Spraying Material
The types of spraying materials mainly include: metal spraying, plastic spraying, wood spraying, ceramic spraying and automobile spraying.
Automobile spraying: Automobile spraying is an indispensable part of automobile manufacturing and maintenance. It not only provides a beautiful appearance to the car, but also protects the body from corrosion and outside damage. Automotive coatings generally use high-performance coatings to ensure long-lasting color and luster in complex environments.
Metal spraying: Metal spraying is a process of atomizing molten metal or other materials and then spraying them to the surface of the object through the air stream. This spraying technology is widely used in the manufacturing industry, especially in corrosion protection and decorative appearance needs. Common metal spraying materials include aluminum, zinc, copper and other alloys.
Plastic spraying: Plastic spraying is to treat plastic particles through a special process to make them present a uniform coating, which is often used for decoration and protection of daily necessities. Due to its light weight, wear resistance and corrosion resistance, plastics are widely used in automotive interiors, home decor and outdoor facilities. Common plastic spraying processes include thermoplastic powder spraying and electrostatic powder spraying.
Wood spraying: Wood spraying is mainly used in furniture manufacturing and interior decoration industry. By spraying the wood surface, it can not only enhance the visual effect of the wood product, but also provide protection and extend its service life. Common wood spraying materials include paint and water-based coatings.
Ceramic spraying: Ceramic spraying is mainly used to make surface decoration and protective layer of ceramic products. Because of its high hardness, wear resistance and good chemical stability, ceramic materials are widely used in the fields of architecture, artwork and daily ceramics. Ceramic spraying technology can give products a unique appearance and texture.
Spray Testing Equipment
Spraying inspection equipment is an important tool for ensuring spraying quality, improving production efficiency and optimizing spraying process. AFI Industries Co., Ltd. has a variety of testing equipment, through real-time monitoring and data analysis, so that the quality of spray products to meet customer quality requirements.
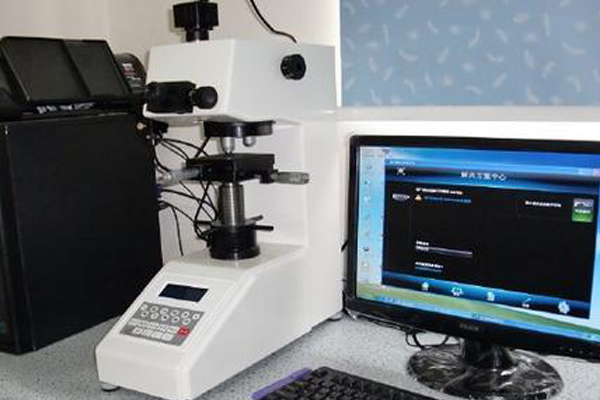
显微镜
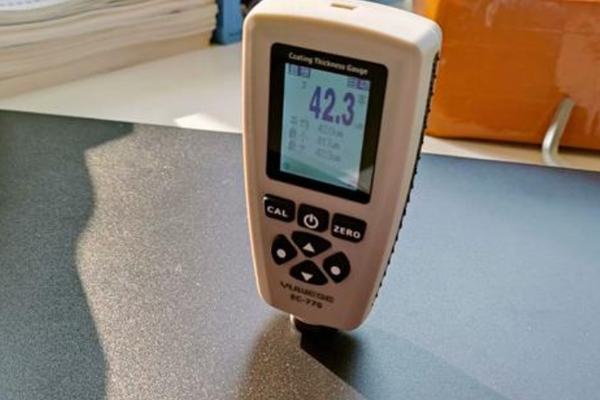
膜厚计
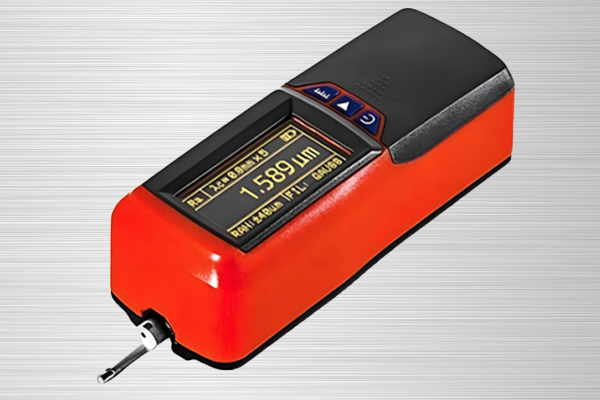
光洁度计
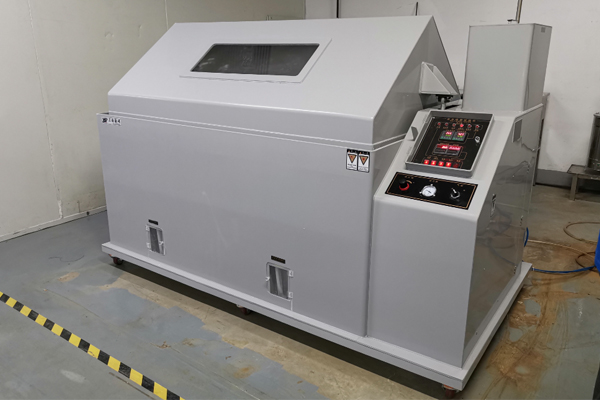
盐雾测试机
We Promise
Your satisfaction and trust is our eternal pursuit, let us work together to create excellent quality and service, witness every moment of success
Frequent Asked Questions
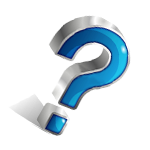
It is a heat treatment process that heats and then rapidly cools a metal to increase its hardness and strength.
Because it can greatly affect the final properties of a metal by changing its molecular structure.
Quenching is commonly used for iron, steel, aluminum, and some alloys, but can also be used for non-metallic materials such as glass and polymers.
The process of heating a metal at a high temperature and rapidly cooling it causes a rapid change in the internal structure of the material, resulting in smaller, more uniform grains, which can increase the hardness and wear resistance of the metal.
Depending on the material and the desired properties of the product, the quenching methods that can be selected include air、oil、water, and salt quenching.
Metals can warp or crack during rapid cooling, as well as develop internal stresses that can affect the final shape and strength of the metal. It is important to carefully control and monitor the quenching process to avoid these problems.