Lost Wax Casting Service
From design to finished product, AFI Industrial Co., Ltd provides customers with one-stop service for lost wax casting with excellent quality and a good reputation to meet customer needs efficiently.
Custom Lost Wax Casting Project
AFI Industrial Co., Ltd. is a large precision machining plant with strong machining capabilities. We provide precision lost wax castings for automotive, rail transit, construction machinery, daily hardware, agricultural machinery, and many other fields, and for the diversified needs of the world’s high-end customers with final finished parts, including precision machining, precision casting, surface treatment, heat treatment, assembly and other overall solutions and one-stop services. So that customers can quickly get a variety of high-quality parts and components products.
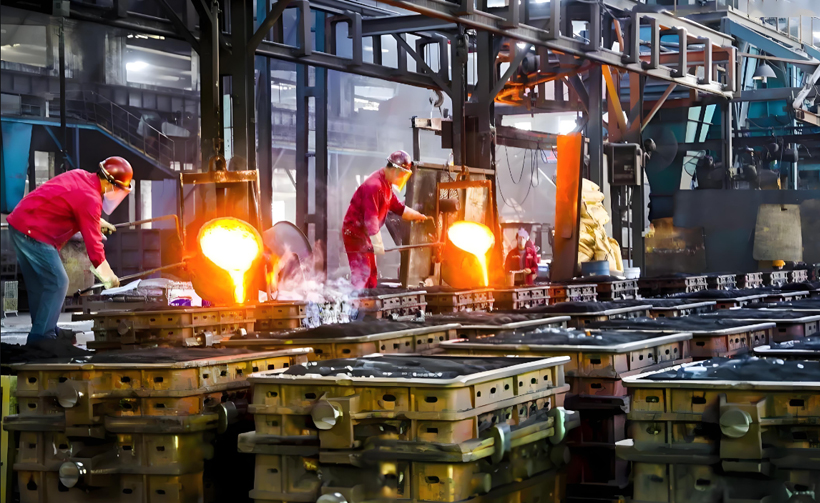
Lost Wax Casting Workshop
Professional lost wax casting technology, to provide customers with customized precision casting.
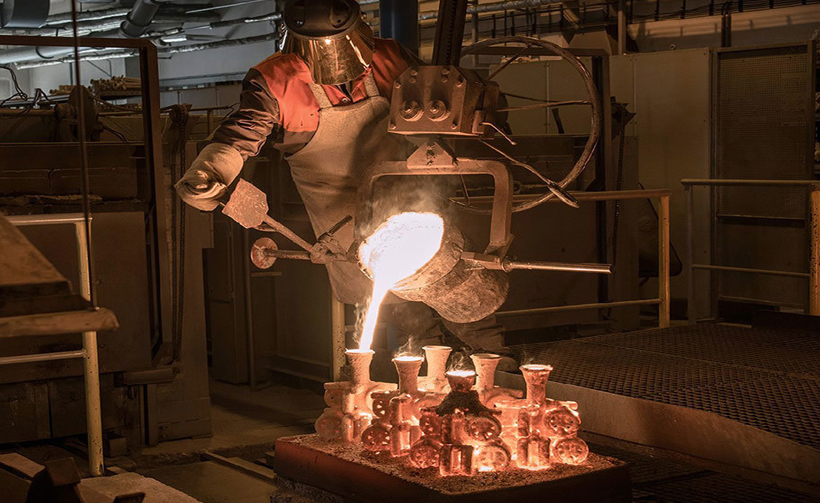
Casting Process
The castings have high precision and uniform dimensional standards, which can meet the quality requirements of customers.
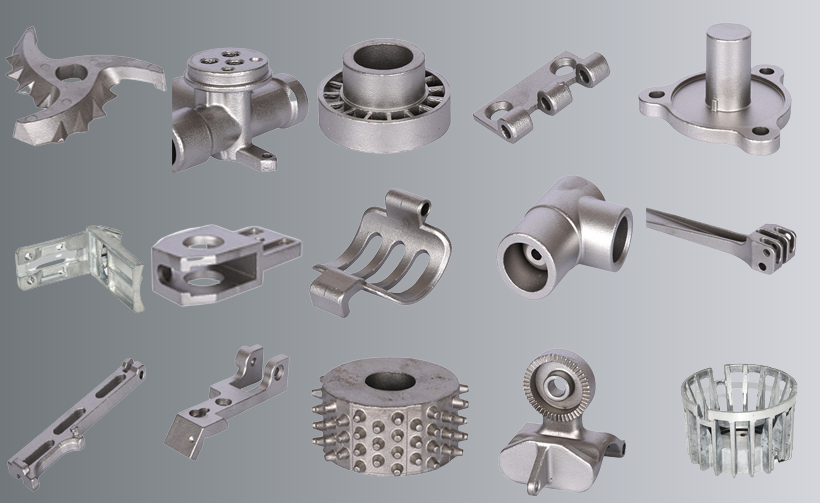
Lost Wax Casting Parts
Lost wax casting parts have high precision, and excellent quality, and can be customized.
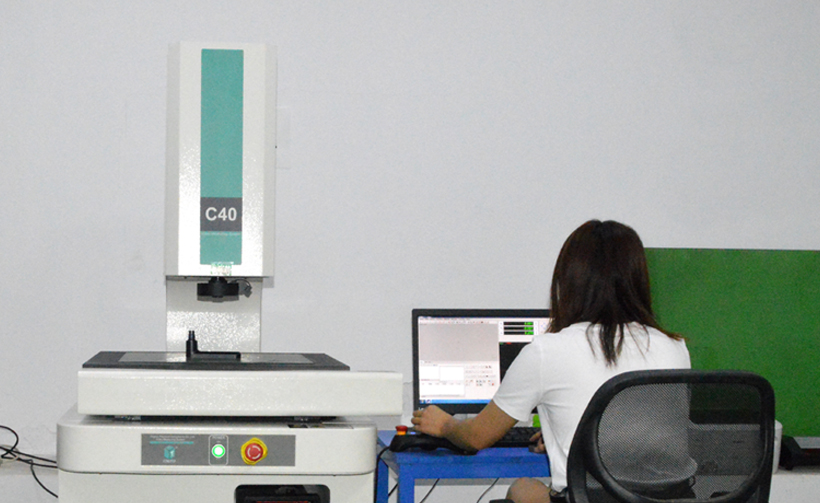
Lost Wax Casting Inspection
Precise inspection equipment and professional personnel ensure that customers get high-quality products.
Custom Lost Wax Casting Service
AFI Industrial Co., Ltd. is committed to providing customers with customized, high-quality precision lost wax casting services.
Starting from the wax model making, our craftsmen use their superb skills to ensure that each wax model is accurate. Then, during the mold shell manufacturing process, the thickness and uniformity are strictly controlled. For casting materials, we ensure that the metal materials used meet high-quality standards and can meet the requirements of different customers for strength, hardness, corrosion resistance, etc.
During the casting process, the temperature and time are precisely controlled to ensure that the molten metal can fill the cavity so that customers can get lost wax castings with extremely high dimensional accuracy and smooth surfaces.
I believe that choosing our company’s precision lost wax casting service is choosing professionalism, quality, and peace of mind.
Precision Lost Wax Casting
Lost-wax casting is a precise metal forming process, and its core advantage lies in accurately replicating complex shapes. Craftsmen make wax molds according to the design, coat them layer by layer with ceramic-based refractory materials to form a composite shell. After melting the wax at high temperature, a precise cavity is obtained. After injecting the metal solution and cooling, a casting with a surface finish of Ra3.2 and a tolerance of ±0.1mm is obtained.
This process is particularly adept at manufacturing parts with complex inner cavities, such as aviation turbine blades, artificial joints and watch movements, and can perfectly present fine patterns at the 0.5mm level. Compared with sand casting, its finished products can directly achieve a mirror-like effect. The dimensional error of repeated casting is less than 0.3%, and no secondary processing is required. These technological advantages make it an irreplaceable core technology in the field of precision manufacturing and play a key role in the production of high-end industries and medical devices.
Lost Wax Casting Process
Lost wax casting has existed for thousands of years, and AFI company’s technicians use modern technology in combination with ancient wax casting methods to produce a wide range of precision castings to meet our customers’ quality needs.

Lost Wax Casting Molds
The metal mold is highly accurate and can be made in any shape. Meet customer needs for various products.
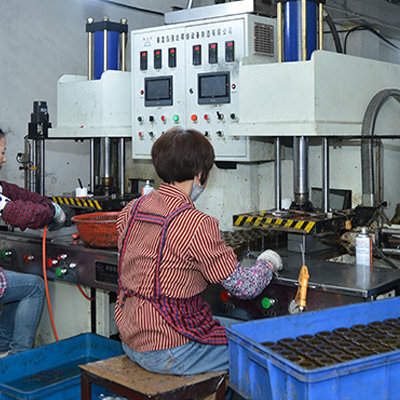
Wax Mold Production
Wax mold surface quality is high precision and can be mass-produced for customers.
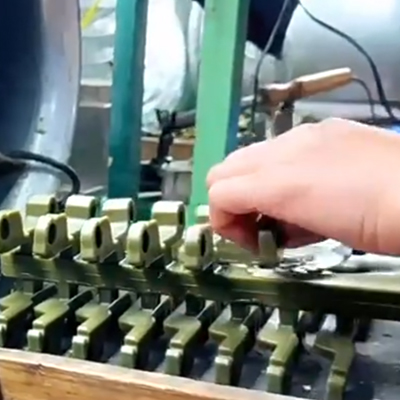
Wax ModuleTree
The wax tree is stable in structure and easy to paste operation, providing a barrier for the successful casting of high-quality metal products.
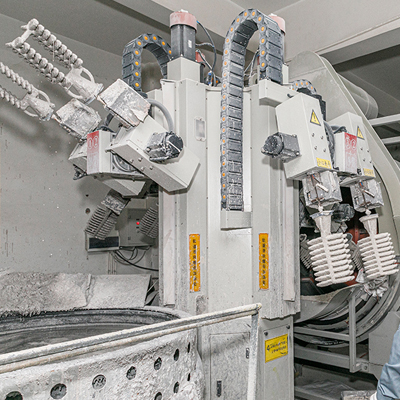
Shell Fabrication
The wax mold is coated with paste and dried and hardened to form a wax shell. After melting the wax with heat, the blank core shell is left.
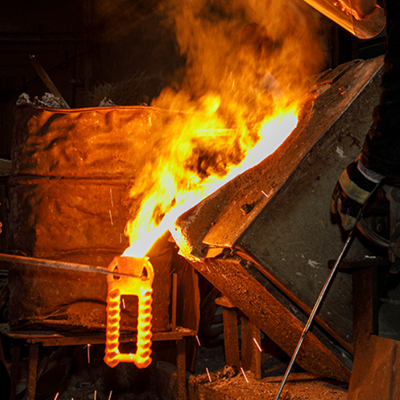
Casting
The metal solution fills the cavity to ensure the integrity of the product shape.
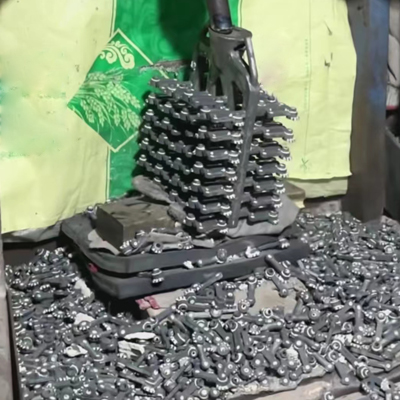
Sand Cutting
After removing the sand shell outside the casting, the casting is cut to ensure that the casting is not damaged to obtain a product with a smooth surface.
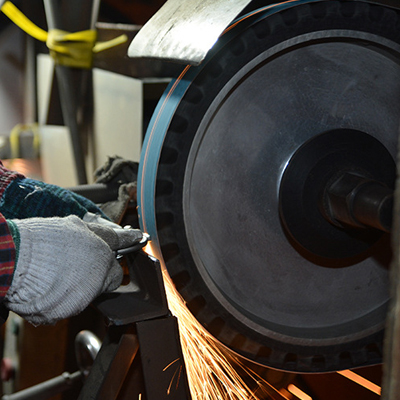
Grinding Sprue Finishing
The surface of the casting is polished to remove burrs and rough parts to make the surface of the casting smooth and smooth lines.
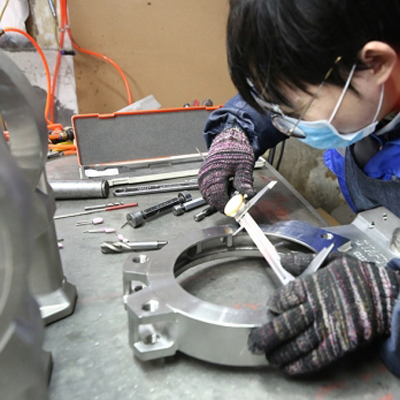
Detection
Strict inspection of product size and appearance, to ensure that the quality of lost wax casting metal products can meet customer requirements.
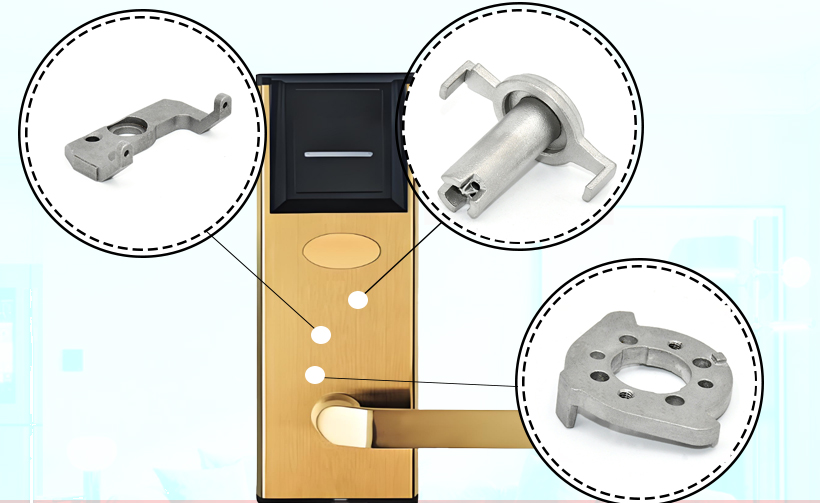
Sample Development of Lost Wax Castings
AFI company’s rapid casting prototyping services provide customers with sample development. Ideal for designers and engineers, our prototyping capabilities allow you to quickly test and improve your designs, helping you launch new products in the shortest possible time and gain a leading position in the market.
Custom Precision Lost Wax Casting
AFI Industrial Co., Ltd. adopts the working principle of lost wax casting and uses lost wax casting tools to fully analyze and manufacture customers’ products. It can meet the strict requirements of complex projects, provide reliable support for various equipment, and improve overall performance. It meets the requirements of customers for products.

Lost Wax Casting Drawing
After receiving the customer’s drawings, our technical team will conduct a drawing review and process planning to ensure that each processing link meets the requirements of the drawings, and the product size accuracy is controlled within ±0.01mm. Our quality control system ensures that the mass-produced products are consistent with the samples and meet all the technical requirements of customers.
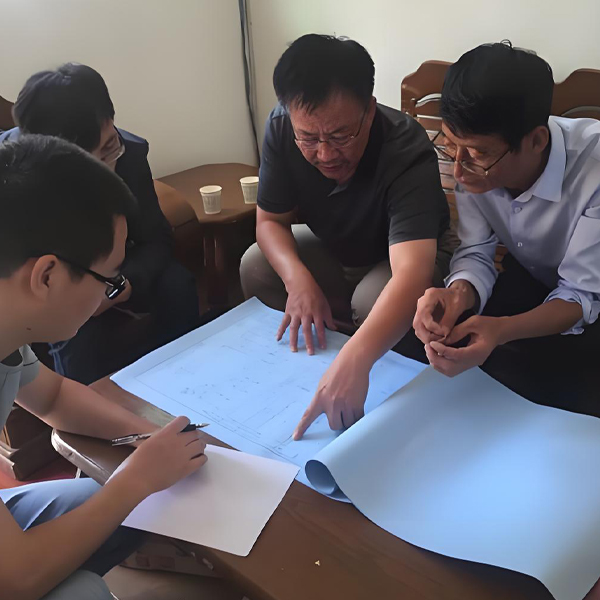
Lost Wax Casting Designs
The engineering team carried out three-dimensional tolerance analysis based on the GD&T standard. They selected the base material in combination with the ASTM material database, optimized the technical parameters through CAM programming, and simultaneously formulated the three-coordinate inspection procedures to ensure the control of μ-level form and position tolerances.
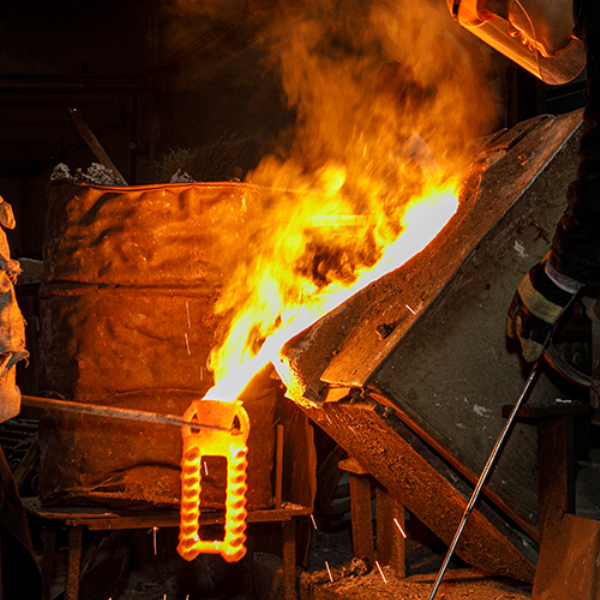
Liquid Metal Casting
Our technical team, relying on years of processing experience, strictly adheres to standardized process flows and uses intelligent numerical control systems to precisely control processing parameters, ensuring that each product meets the dimensional accuracy and surface finish requirements of the drawings, providing customers with stable and reliable precision parts processing services.
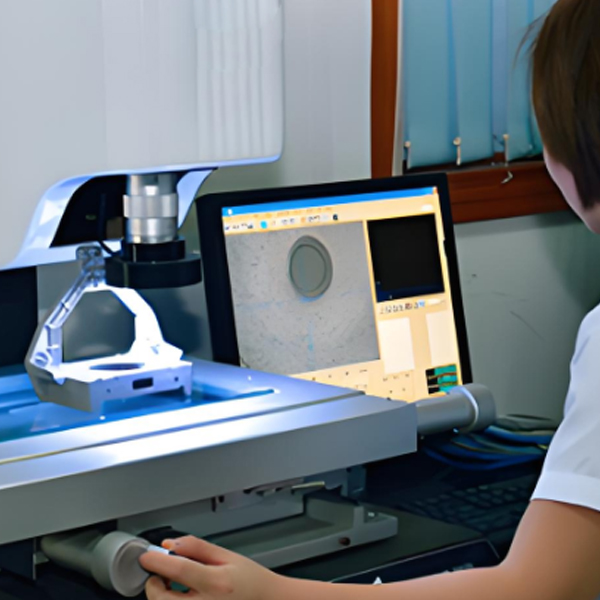
Lost Wax Castings Measurement
From incoming material to the manufacturing process to delivery, quality inspection personnel test the products according to the drawings to ensure that the products fully meet the quality requirements of customers.
Custom lost wax casting materials
AFI Industrial Co., Ltd offers customers a wide range of lost-wax cast metal materials, including stainless steel, copper, aluminum, carbon steel, alloy steel, iron, magnesium, and precious metals. Meet your diverse needs.
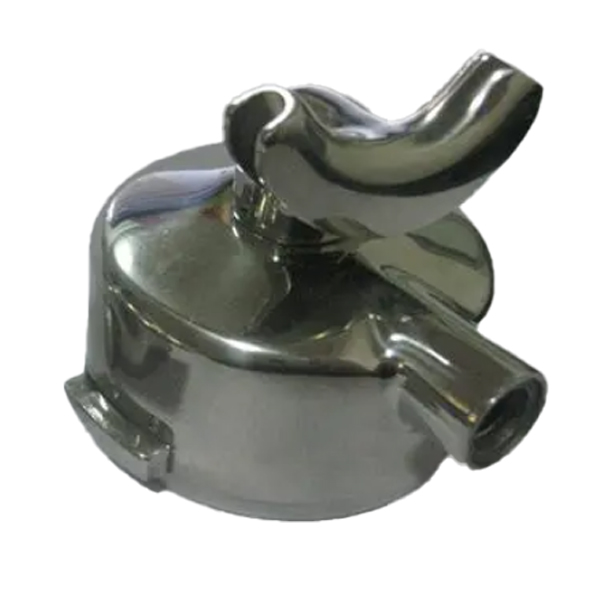
Stainless steel has good corrosion resistance, strength, and toughness, and it is suitable for manufacturing a variety of mechanical parts, building hardware, kitchen accessories, lighting accessories, valves, and pipe fittings. Common stainless steel models such as 304 and 316 are widely used in dewaxing casting.
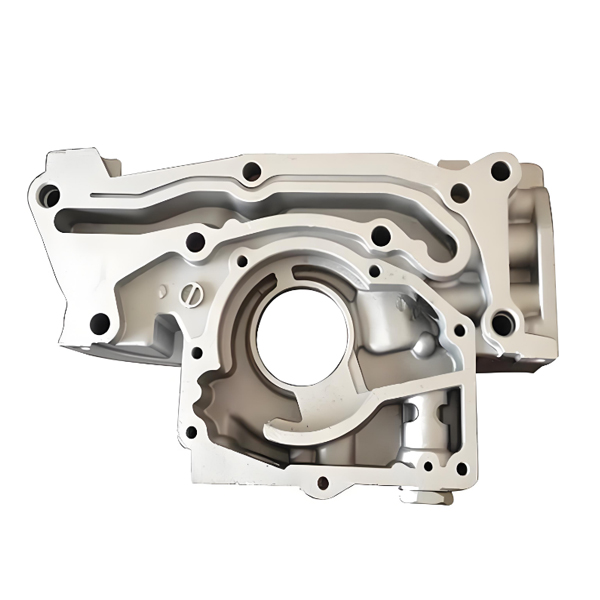
Aluminum has the characteristics of low density, lightweight, good thermal conductivity, and corrosion resistance. Lost wax-cast aluminum is often used in the manufacture of aerospace parts, automotive parts, electronic equipment casings, etc.
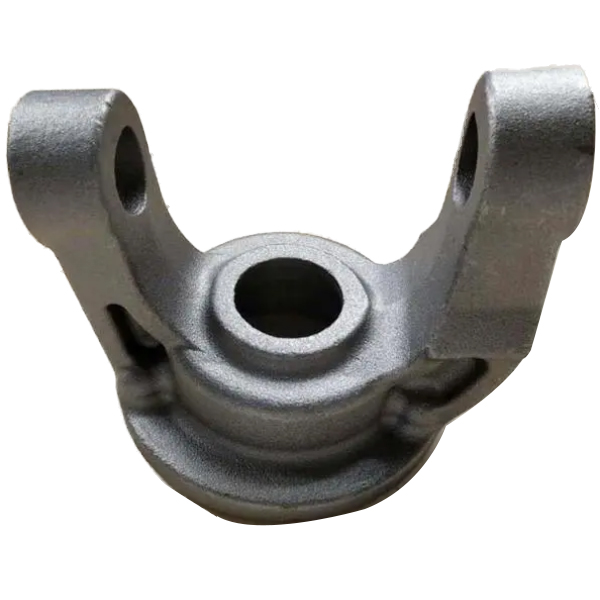
Carbon steel is relatively low in price, has good strength and machinability, and can be used to manufacture some parts with higher strength requirements and less demanding corrosion resistance requirements, such as mechanical structures and building components.
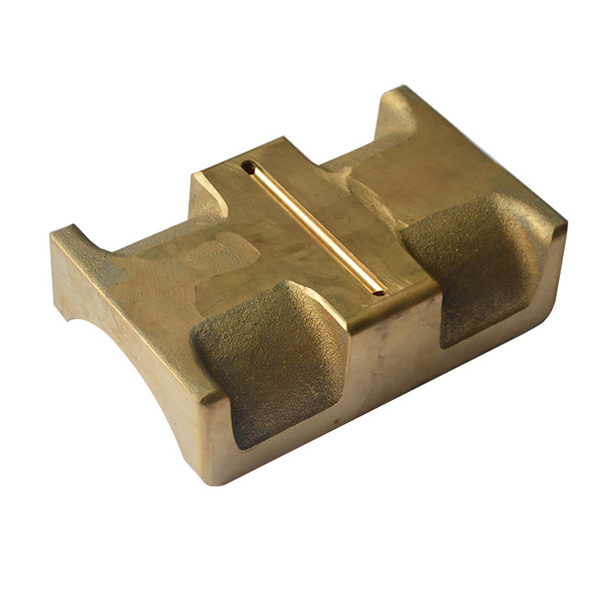
Copper includes brass, bronze, red copper, etc. Lost-wax cast copper has excellent electrical conductivity, thermal conductivity and ductility, and is often used to manufacture electrical components, pipe fittings, decorative handicrafts, etc. For instance, lost-wax cast bronze is often used to make some exquisite statues, while lost-wax cast red copper and lost-wax cast brass can be used to make handicrafts and electrical switch parts.
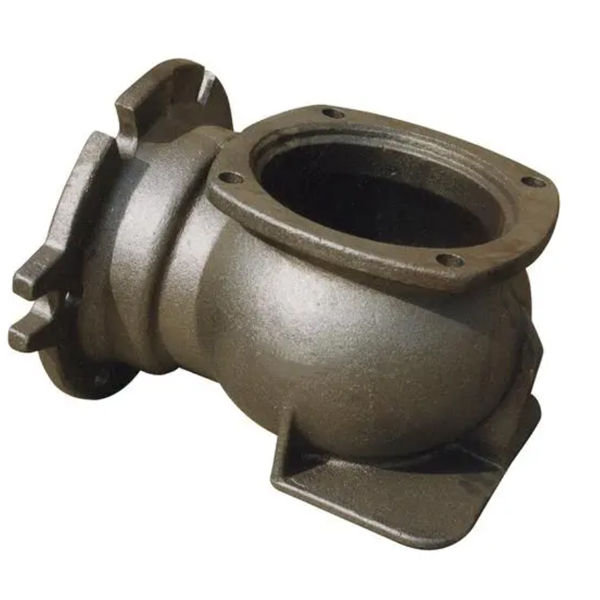
Alloy steel with added elements such as chromium, molybdenum and nickel has a strength of 1000-2000 mpa, is wear-resistant, heat-resistant and corrosion-resistant, and is used in key components such as aero engines and automotive crankshafts.
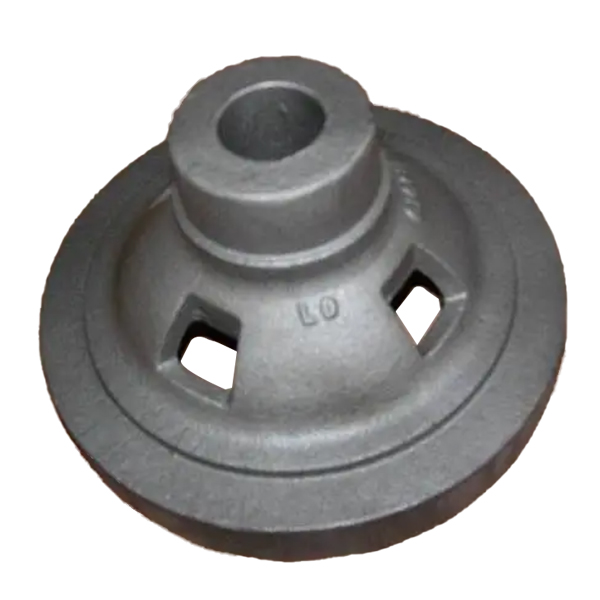
Steel is a material made by adding carbon and some other alloying elements (such as manganese, chromium, nickel, etc.) to iron. It has high strength, good toughness and is particularly easy to process.
Due to the highly flexible properties of steel and its relatively low price, it is used in construction, mechanical manufacturing, aerospace, shipbuilding and various aspects of our daily life.
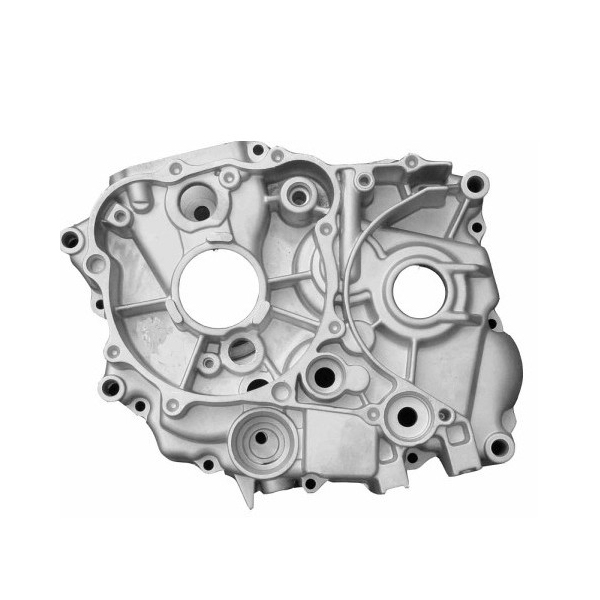
Titanium alloys feature high strength (tensile strength 900-1400 mpa), low density (4.5g/cm³), corrosion resistance and biocompatibility, and are used in the manufacturing of aviation structural components, artificial joints and high-end sports equipment, among other fields.
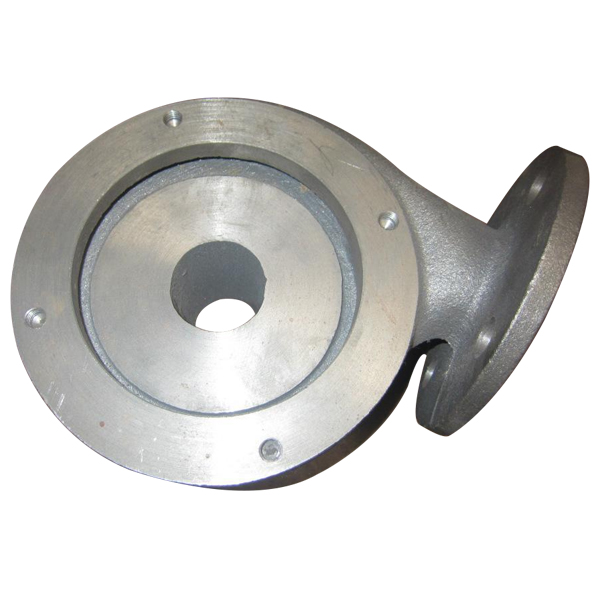
The main precious metal materials commonly used in lost wax casting are gold, silver, platinum, palladium, and so on.
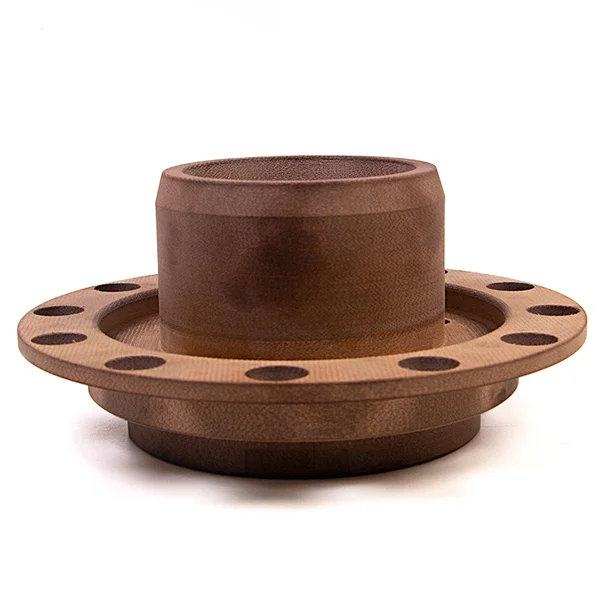
CNC turning wood is easy to process, the material is light and strong, and it is a good heat insulation and electrical insulation materialhogany.
- camphor wood
- Chinese fir
- yellow pineapple wood
- Liu An wood
- basswood
- oak
- catalpa wood
Custom Surface Treatment
AFI Industrial Co., Ltd offers customers a wide range of lost-wax cast metal materials, including stainless steel, copper, aluminum, carbon steel, alloy steel, iron, magnesium, and precious metals. Meet your diverse needs.
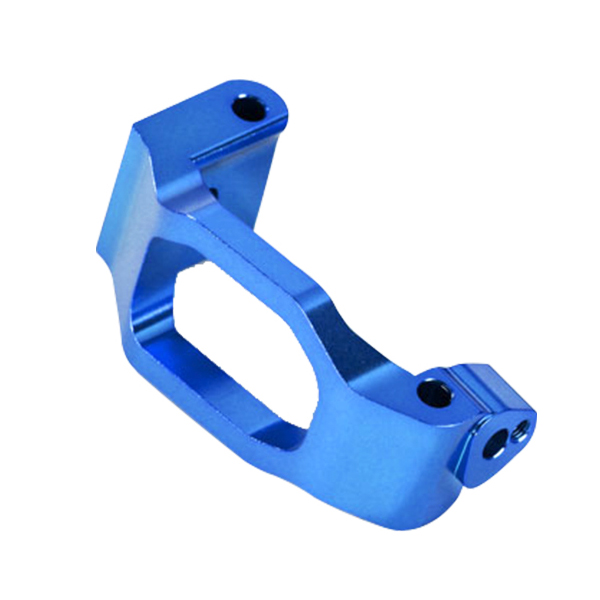
Anodizing: Our technicians immerse metal products in electrolytes such as sulfuric acid, chromic acid or oxalic acid. The surface of the products undergoes an oxidation reaction, forming an oxide film, thereby completing the anodic oxidation reaction of the products. This surface treatment is mainly used for aluminium and its alloys, and can also be applied to metals such as titanium and magnesium. It can enhance the corrosion resistance and wear resistance of the product. We offer customers a variety of color options to meet the diverse appearance requirements of the product. Anodizing processes are widely applied in fields such as aerospace, automotive industry, architectural decoration, consumer electronics casings, and medical devices.
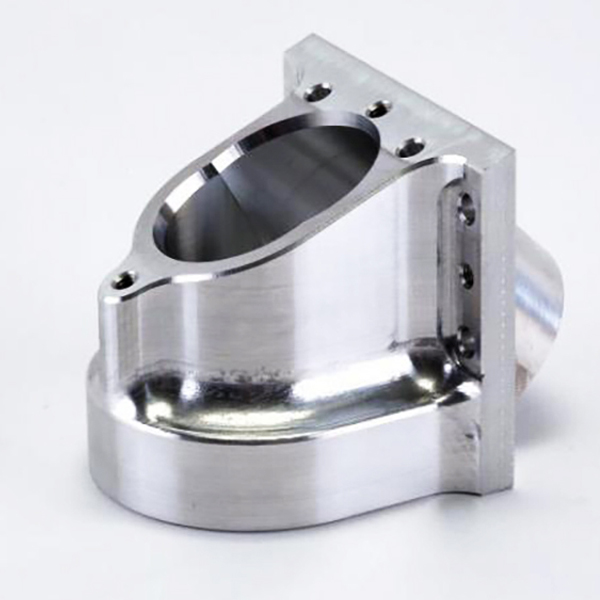
Electroplating is the process of reducing metal ions in the electroplating solution and uniformly depositing them on the surface of the product to form a dense and strong metal coating. Electroplating can significantly enhance the corrosion resistance, electrical conductivity, and aesthetic appeal of metal products, and thus is often used in fields such as automobiles, electronics, and home appliances.
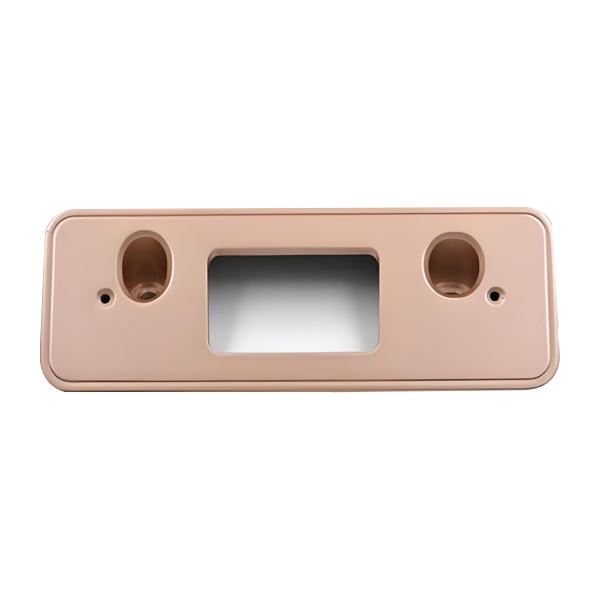
Spraying is a commonly used surface treatment technology, there are various spraying methods, air spraying with its flexible operation, high coating quality and low cost advantages, widely used in automobiles, air tools, electrical equipment and other areas of hardware parts.
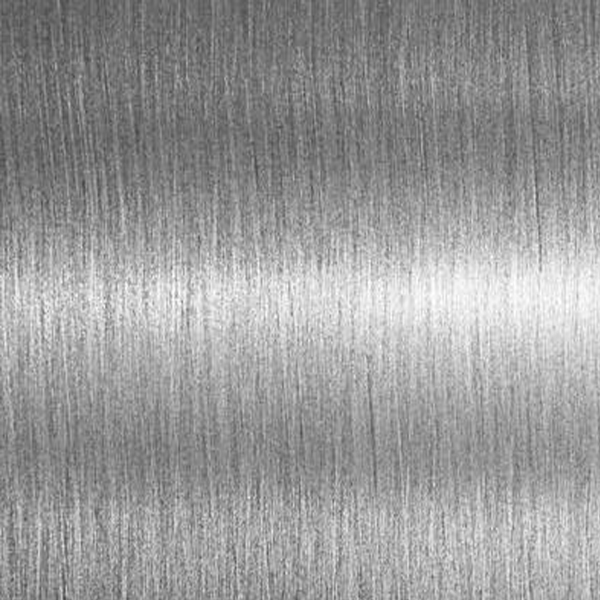
Brushed is a surface treatment method that forms lines on the surface of the workpiece by grinding the product to play a decorative effect. Because the surface drawing treatment can reflect the texture of metal materials, it has been loved by more and more users and is more and more widely used.
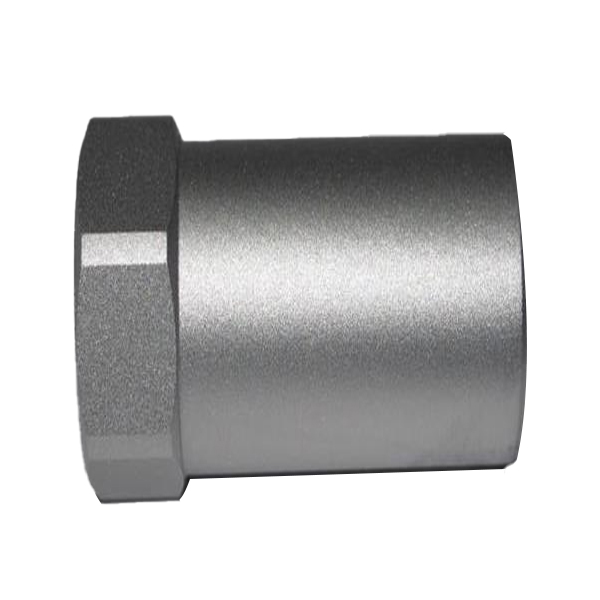
Sandblasting is a process for surface treatment of workpieces. The compressed air is used as the power to form a high-speed jet beam to spray the spray material (copper ore, quartz sand, emery, iron sand, sea sand) to the surface of the workpiece to be treated at high speed so that the appearance or shape of the workpiece surface is changed.
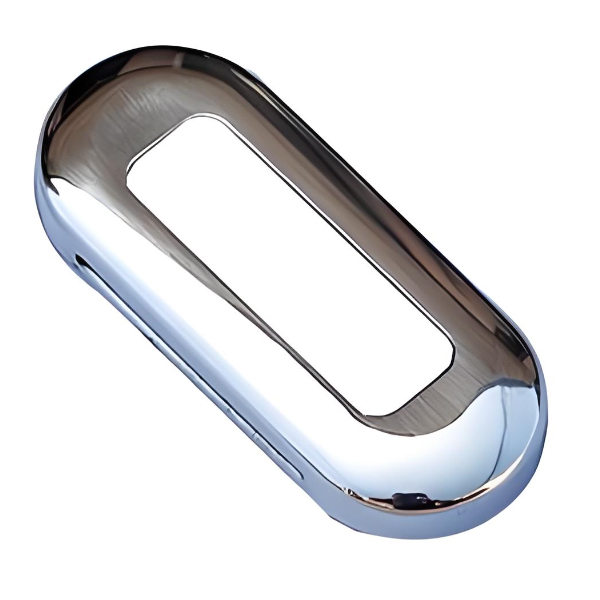
Polishing is a process that removes microscopic protrusions on the surface of materials through physical, chemical or electrochemical methods, making them smooth, flat or even achieving a mirror-like effect. It is widely used in fields such as precision parts processing, automobiles, and medical equipment.
Mass Production
AFI Industrial Co., Ltd. castings annual production capacity of 4000 tons, can be professional manufacturing of stainless steel, carbon steel, alloy steel, nickel base alloy, and other materials of precision castings, can guarantee the quality of the first to meet the needs of customers in different quantities.
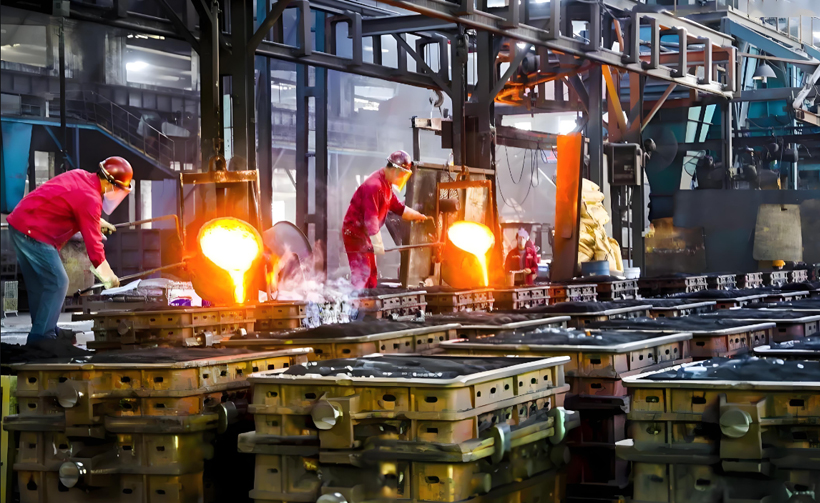
Dimensional Tolerance
AFI Industries Co., Ltd. castings can achieve dimensional accuracy of approximately 25.4mm±0.10mm in length, which means that the tolerance is about 0.8-1% of the product size, ensuring that each part is always accurate and fits perfectly with the other parts.
How to Start Your Order
Send your drawings
Process discussion, quotation
Make a sample
Volume produce
Shipment & Payment
Shipping
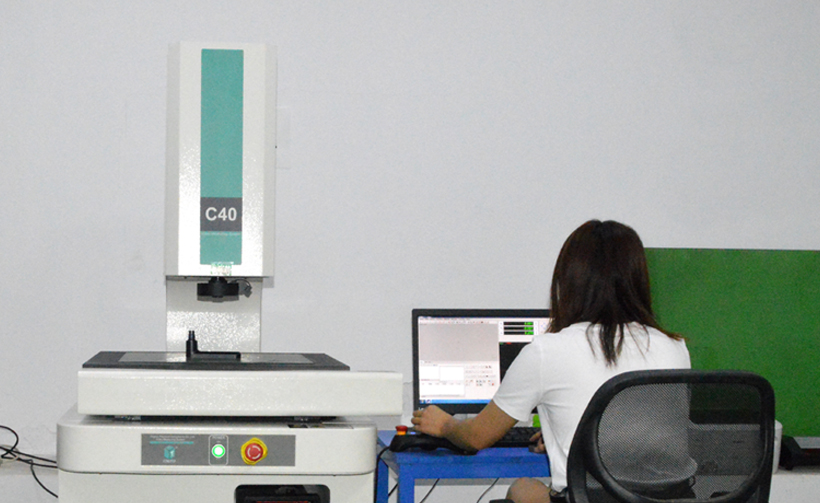
Checkout
AFI Industrial Co., Ltd. has established a quality management system for CNC parts, equipped with professional testing equipment and a senior quality inspection team. We conduct all-round inspections at every stage in accordance with the customer’s drawings and technical standards to ensure that all products meet 100% of the customer’s quality requirements and industry standards.
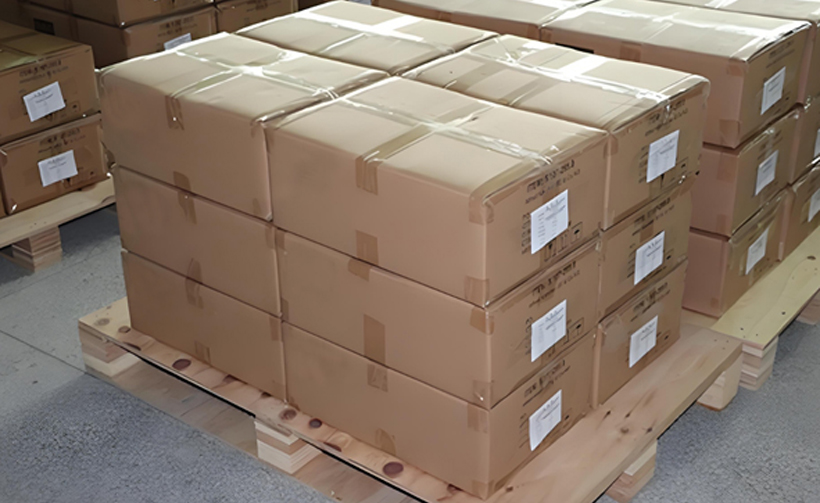
Shipment
AFI Industrial Co., Ltd. collaborates with many well-known logistics partners worldwide. We will carefully package your products based on their characteristics and requirements, and then select the most cost-effective and fastest transportation plan for you to ensure the safe and punctual delivery of your goods.
Our Promise
With our services, you will get a trusted supplier. In the coming days, we will continue to improve our professional degree, expand our credibility, and let you get the following harvest!

Quality Guarantee
We provide a full range of checks to ensure that the dimensions are accurate and the appearance meets customer specifications during the lost wax casting.

Quick Response
After receiving the order, we respond quickly within 2 hours, quote within 4 hours, and deliver according to quantity within 3-15 days.

Custom Material
We will according to the needs of customers, carefully select high-quality raw materials, customized to meet customer needs for all kinds of products.

Custom Surface Treatment
We can apply a variety of surface treatments to manufactured products according to customer requirements, including electroplating, anodizing, etc.

Arbitrary Size
We can produce products strictly in accordance with the dimensions on the drawings provided by customers, ensuring that every dimension is precise and error-free, fully meeting the quality standards.

Unlimited Quantity
Whether you need samples or mass production, we can precisely manufacture according to your requirements, ensuring that the quality of each product remains consistent.
Brand We Cooperated with
AFI Industrial Co., Ltd. has specialized in precision parts processing for 15 years and possesses multiple high-precision five-axis turning centers. We have passed the ISO9001 quality system certification. We have long been providing key components for the automotive and home appliance industries. We have rich mass production experience in products such as transmission valve bodies and heat dissipation components. Our product quality is stable and reliable, with a defect rate controlled below 0.05%.
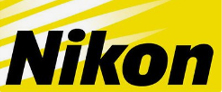
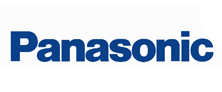
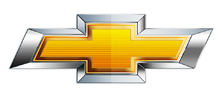
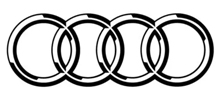
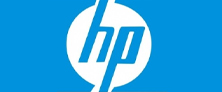
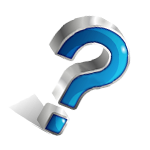
Frequent Asked Questions
The main difference between direct lost wax casting and indirect lost wax casting is the way the wax model is made. Direct lost wax casting is to use wax to make a mold directly, and then cast the product; indirect lost wax casting is to first make a metal original mold, use the metal original mold to make a silicone mold, and then use the silicone mold to inject wax to get a wax film.
Wax molds need to have a low shrinkage rate, high strength and easy removal. We often use a mixture of paraffin, beeswax and synthetic wax to ensure the forming accuracy and demolding integrity.
Post-treatment of lost-wax casting includes cutting gates and risers, sandblasting cleaning, heat treatment (such as annealing and strengthening), machining correction and surface treatment (such as electroplating and polishing) to enhance the performance and appearance of the finished product.
Carbon steel, stainless steel, aluminum alloy, copper alloy, etc., they are especially suitable for high-temperature alloys (such as aviation blades).
We need to improve the air permeability of the gating system and the shell to prevent air holes, regulate the cooling rate and the support structure to prevent deformation, strictly inspect the shell and the dewaxing process to enhance its surface quality, and precisely control the wax mold shrinkage rate and mold size to ensure accuracy.