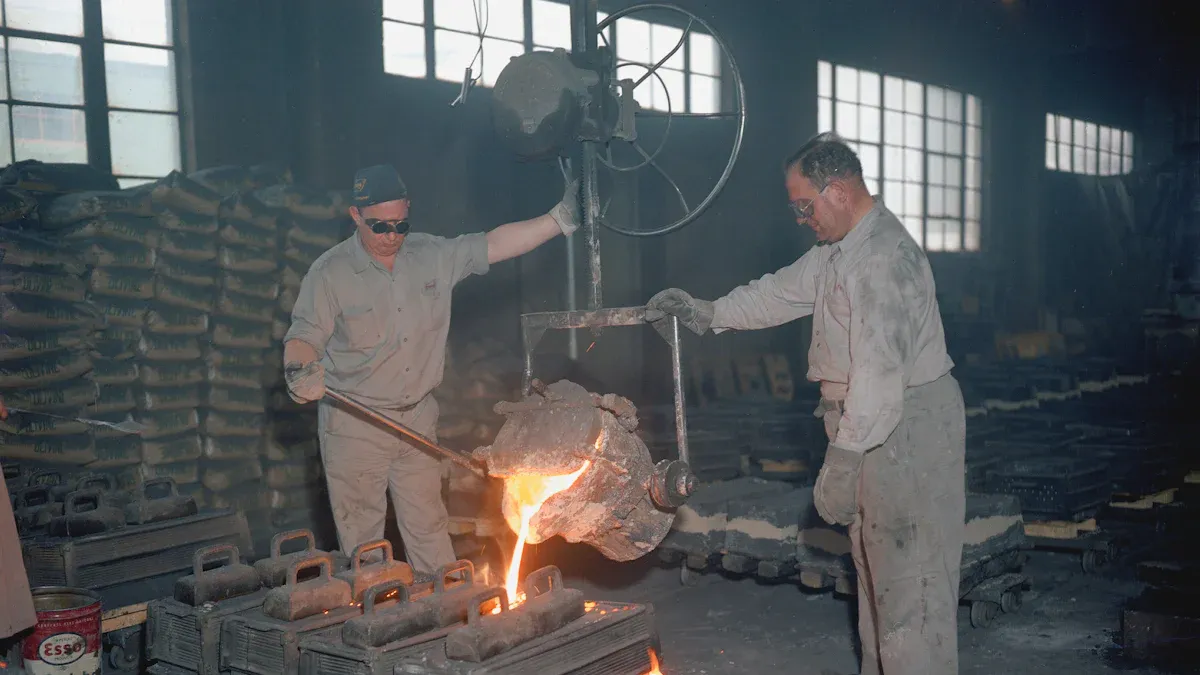
When you pick sand casting for your project, you get more choices in design and materials. This method works for making a few or many parts. You can save money, get parts fast, and trust the results. But, you might see some limits in how smooth the surface is and how exact the size is. Knowing these things helps you choose the best casting method. AFI Industrial Co., Ltd. uses many years of skill and new technology in every sand cast job.
Key Takeaways
- Lets you make many shapes. You can use many metals for small or big parts.
- This method saves money, especially for test parts and small to medium batches. Tooling costs are low and you can change molds fast.
- You can use the sand again in the process. This makes sand casting better for the environment and helps save resources.
- Often the surface is rougher than otherwise crafted. You may need to take extra steps to make the part smooth.
- The size of parts can change a bit. Some machining may be needed to get the right size.
- Problems like porosity and shrinkage can happen. Good mold design, sand control, and using special software can help stop these problems.
- Ideal for projects that require quick changeovers, different materials and higher precision. However, not optimal for very smooth or super-precise parts.
- Good quality checks and modern tools help make sure parts are the same. They also help lower waste and mistakes.
Process Overview
Sand Casting Process
Sand casting lets you make metal parts in many shapes and sizes. You can use this process for easy or hard designs. Here is what happens during sand casting:
Mold Creation
First, you make a pattern that looks like your finished part. You put the pattern in a box called a flask. Next, you pack sand around the pattern to make the mold. The sand must be strong but also soft enough to take out the pattern. You add channels called gating systems to help the molten metal flow into the mold.
Tip: Using computer tools like CAD and casting simulation software helps you design better molds. These tools can show problems before you start making parts.
Melting and Pouring
Table of Contents
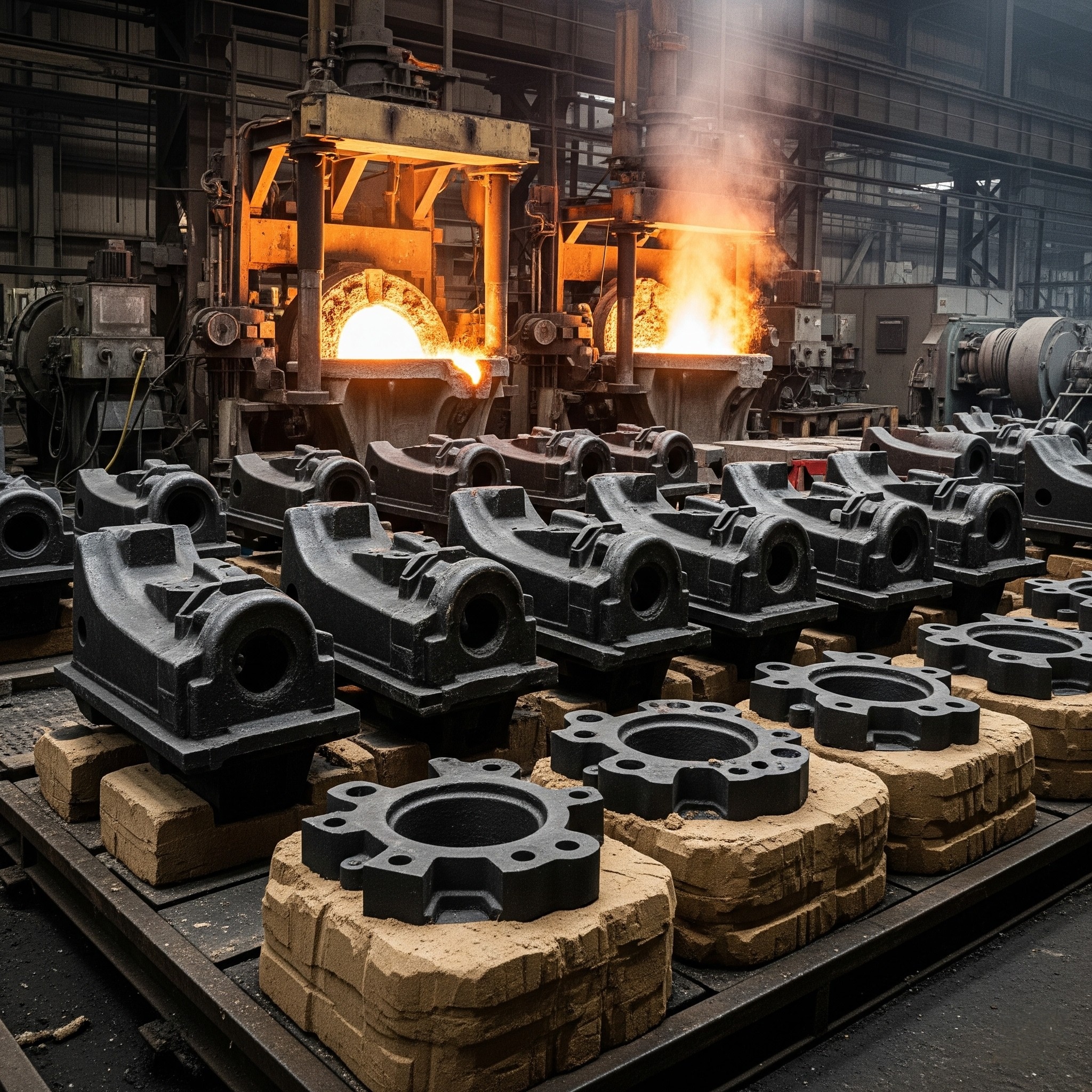
Then, you heat the metal until it melts. You pour the hot metal into the sand mold through the gating system. You must keep the metal at the right temperature to stop problems. Pouring the metal is quick but very important.
Cooling and Finishing
After pouring, the metal cools down and gets hard inside the sand mold. How long it takes depends on the size and shape of the part. Big parts can take days to cool. When the metal is hard, you break the mold to get the part out. You cut off extra metal and clean the part. Many foundries use the sand again, which helps the environment.
Step | Description | Time Parameters | Temperature Parameters |
---|---|---|---|
Pattern Making | Put the pattern in place, dust it, fill and pack sand around it. | Setup: about 1 hour; Drying: up to 12 hours | N/A |
Mold Creation | Make the gating system, fill with sand, and pack it. | N/A | N/A |
Melting and Pouring | Pour melted metal into the mold. | Only a few moments | Keep metal at the right temperature |
Solidification and Cooling | Metal cools and gets hard in the mold. | Time changes; big parts need days | Metal cools from hot to solid |
Finishing and Shakeout | Break the mold, take out the part, clean and finish it. | N/A | N/A |
Sand Recycling | Separate and fix the sand so it can be used again. | N/A | N/A |
Materials Used
You can pick from many materials for sand casting. The sand mold uses different sands and binders to keep its shape. Here are some common choices:
- Green sand: Made from silica sand, bentonite clay, and water. It is soft and cheap.
- Dry sand: Like green sand but uses chemicals instead of water. It is good for parts that need to be very exact.
- Binders: Clay or chemicals help the sand stick together.
- Additives: Coal dust and other things make the surface smoother and help remove the mold.
For the metal part, you can use:
- Ferrous metals: Gray iron, ductile iron, malleable iron, mild steel, stainless steel, and alloy steel.
- Non-ferrous metals: Aluminum, zinc, lead, and copper.
The sand and metal you choose change how strong, smooth, and good your part will be.
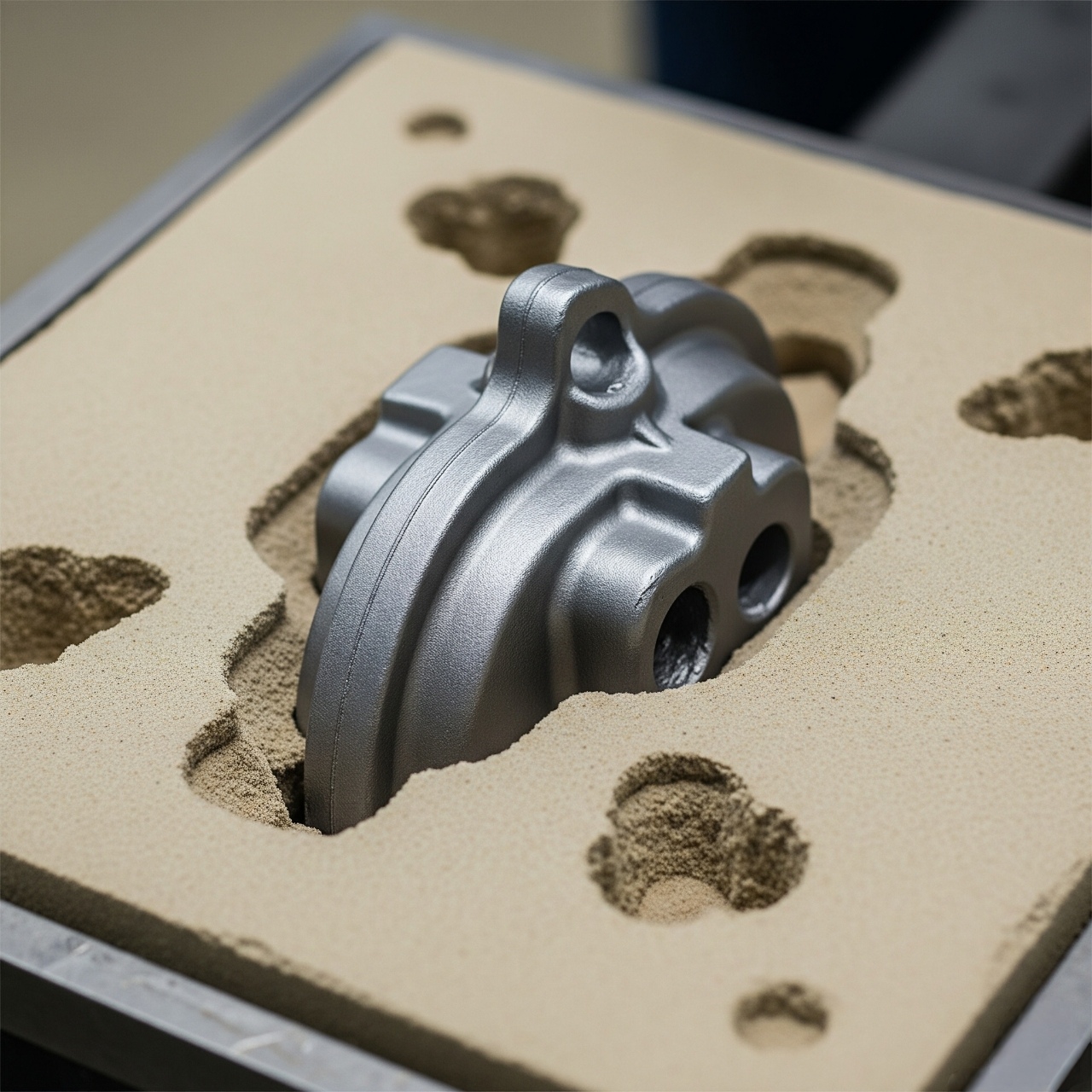
Materials for casting
Material Category | Main Alloy Type/Grade (Example) | Main Chemical Composition (Approximate Range) | Key Characteristics | Typical Application |
Cast Iron | Gray Cast Iron | C: 2.5-4.0%, Si: 1.0-3.0%, Mn: 0.5-1.0%, (minor S, P) | Good damping, excellent machinability, poor ductility/toughness | Machine beds, cylinder blocks, pipes, casings |
Ductile Iron | C: 3.0-4.0%, Si: 2.0-3.0%, Mn: 0.2-0.6%, Mg: 0.03-0.08%, (rare earth elements) | High strength, good toughness, ductility close to steel | Automotive parts (crankshafts, connecting rods), agricultural machinery parts, valves, fittings | |
Malleable Iron | C: 2.0-3.0%, Si: 0.8-1.4%, Mn: 0.2-0.5% | Ductile and tough after annealing treatment | Automotive and tractor parts, pipe fittings, valves | |
Cast Steel | Carbon Cast Steel | C: <0.6%, Si: <0.8%, Mn: <1.8% | Strength and hardness increase with carbon content; ductility and toughness decrease | Gears, hubs, locomotive and rolling stock parts, couplings |
Alloy Cast Steel | Carbon steel with added Cr, Ni, Mo, V, etc. | Specific properties like wear resistance, heat resistance, corrosion resistance | Stainless steel castings, heat-resistant grates, high-manganese steel parts | |
Aluminum Alloys | A356 | Si: 6.5-7.5%, Mg: 0.25-0.45%, Fe: <0.20%, Cu: <0.20% | Excellent castability, weldability, and corrosion resistance; lightweight | Aerospace components, automotive wheels, chassis parts |
A380 | Si: 7.5-9.5%, Cu: 3.0-4.0%, Fe: <1.3% | Good flowability and mechanical properties; common die-casting alloy | Automotive parts, electronic equipment housings, tool components | |
Copper Alloys | Brass | Cu: >50%, Zn, (may contain Pb, Sn, etc.) | Good flowability and castability, easy to machine | Valves, faucets, plumbing fittings, decorative items |
Bronze | Cu: >50%, Sn (tin bronze), or Al (aluminum bronze), Si (silicon bronze), etc. | High strength, wear resistance, corrosion resistance, or good self-lubrication | Bearings, gears, propellers, pump bodies, artistic castings | |
Magnesium Alloys | AZ91 | Al: 8.5-9.5%, Zn: 0.4-1.0%, Mn: >0.13% | Ultra-lightweight, high specific strength, but relatively poor corrosion resistance | Aerospace components, lightweight automotive parts, electronic product casings |
Application
Metal casting is used in many industries because it is hard wearing and saves money. This process is suitable for automobiles, airplanes and large mechanical parts. For example, engine blocks, housings, brackets and large mechanical parts can be manufactured. Sand casting accounts for about 45% of all metal castings, which shows its importance. You can use it for small or large jobs, which is why many people choose this method.
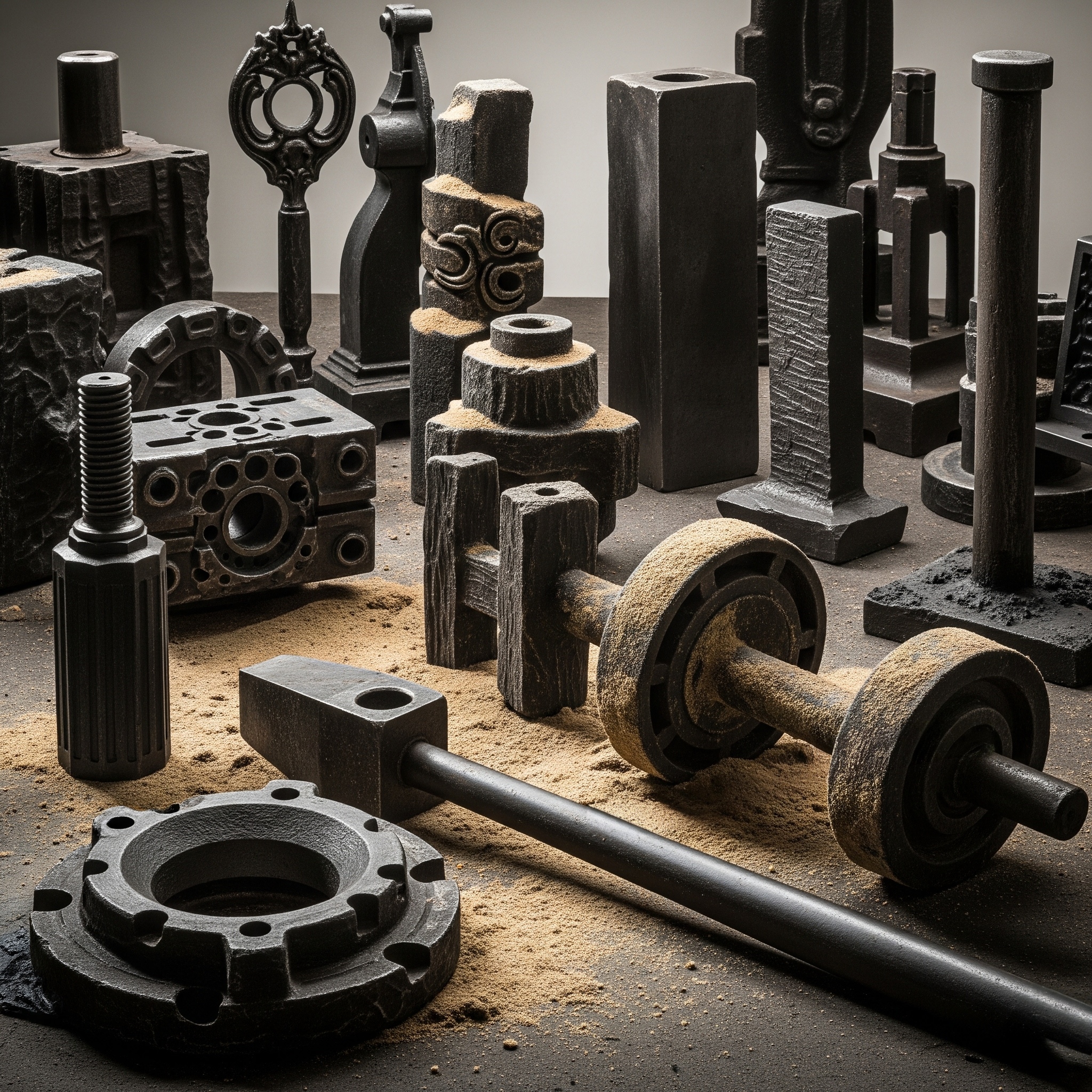
benefits of using sand casting
Design Flexibility
Sand mold casting has many design options. You can make shapes that are difficult to make by other methods. It allows you to make parts with thin walls or special curves. You can make both small parts and large parts, such as gears or large machine tool column architectures.
- You can change your design fast by changing the sand mold. This helps you try new ideas quickly.
- Making a prototype is very easy and the low mold costs and inexpensive. You can test different versions before making the final part.
- Digital tools like CAD and CAM help you make molds that fit your design. Automation and 3D printing help you make detailed molds with good accuracy.
- Many industries use sand casting to make parts with special shapes and details.
For example, car companies made engines lighter by 15% using sand casting. Airplane companies made turbine blades with special cooling channels. These show how sand casting helps make better parts and new ideas faster.
Material Versatility
Sand casting lets you use almost any metal. You can use iron, steel, aluminum, copper, and many alloys. This means you can pick the best metal for your needs, like strong or light metals.
Sand casting works well with metals that melt at high heat, like iron and nickel alloys. You can control the quality by changing the sand mix, water, and how hard the mold is. Testing and computer tools help you get the right finish and strength for each metal. This makes sand casting a good choice for jobs that need different metals.
Prototype casting is easier because you can try your design in many metals. This saves time and money before you pick the final metal.
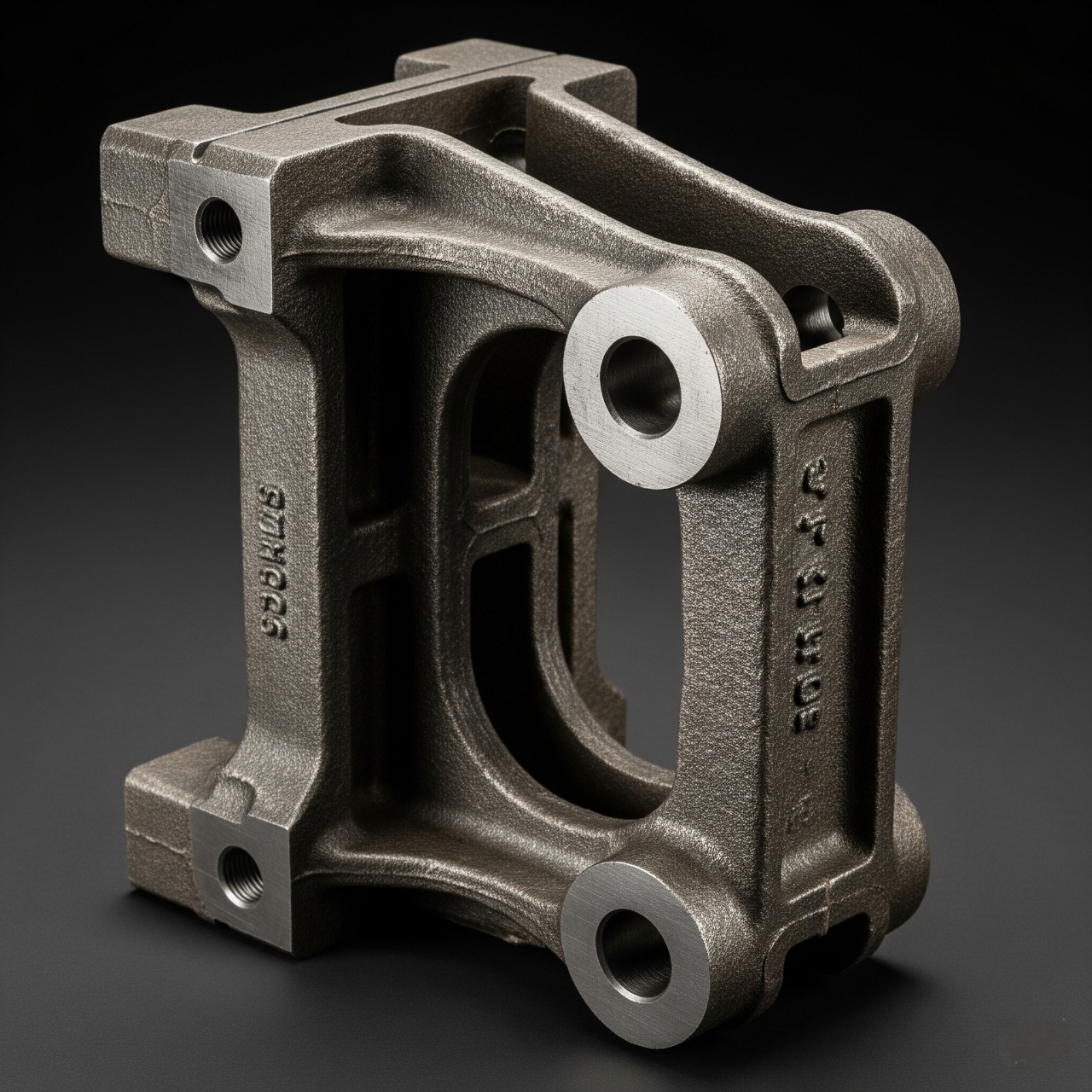
Cost Advantages
Sand mold casting is less expensive than many other methods. Since sand molds are cheap and easy to make, you don't have to spend much on tools. This is the ideal application why many companies use this process for prototypes and small production runs.
Cost Factor | Sand Casting | Investment Casting | Aluminum Die Casting |
---|---|---|---|
Tooling Costs | Moderate | High | High |
Material Costs | Moderate | Moderate to High | Moderate to High |
Production Volume | Low to High | Low to Medium | Moderate to High |
Part Complexity | Moderate to High | High | Moderate to High |
Lead Times | Moderate to Long | Moderate to Long | Moderate to Short |
You can use sand molds more than once, which saves money over time. Labor and energy costs stay low because the tools are simple. For small and medium jobs, sand casting gives you good quality for the price. You can also change your tools fast and cheap, so you can meet new customer needs.
Sand casting saves money at the start, makes prototypes fast, and works for both simple and hard parts. These reasons make sand casting a smart pick for many projects.
Scalability
Sand casting can be used for small or big jobs. You can make just one part or thousands of parts. This makes sand casting very flexible. New technology like 3D printing helps make molds and cores. It removes old limits and lets you go from one part to many parts fast.
- You can make a prototype or lots of parts with the same method.
- Special ceramic sand helps keep the parts good, no matter how many you make.
- Machines help place patterns, put molds together, cool, and finish parts. This keeps each part the same, even if you make more.
- Sensors check temperature, moisture, and sand packing while you work. This keeps quality the same from start to finish.
- Computer programs help you design better molds and control metal flow. This means fewer mistakes and saves time.
- Good rules for mixing sand make strong molds that let air out. This cuts waste and helps you make more parts.
Sand casting works for hard shapes and many metal types. This is why it is good for both testing and making lots of parts. You do not need to spend much on tools or machines to make more parts. You can get test parts fast and start making more quickly. These things help you keep up with what customers want.
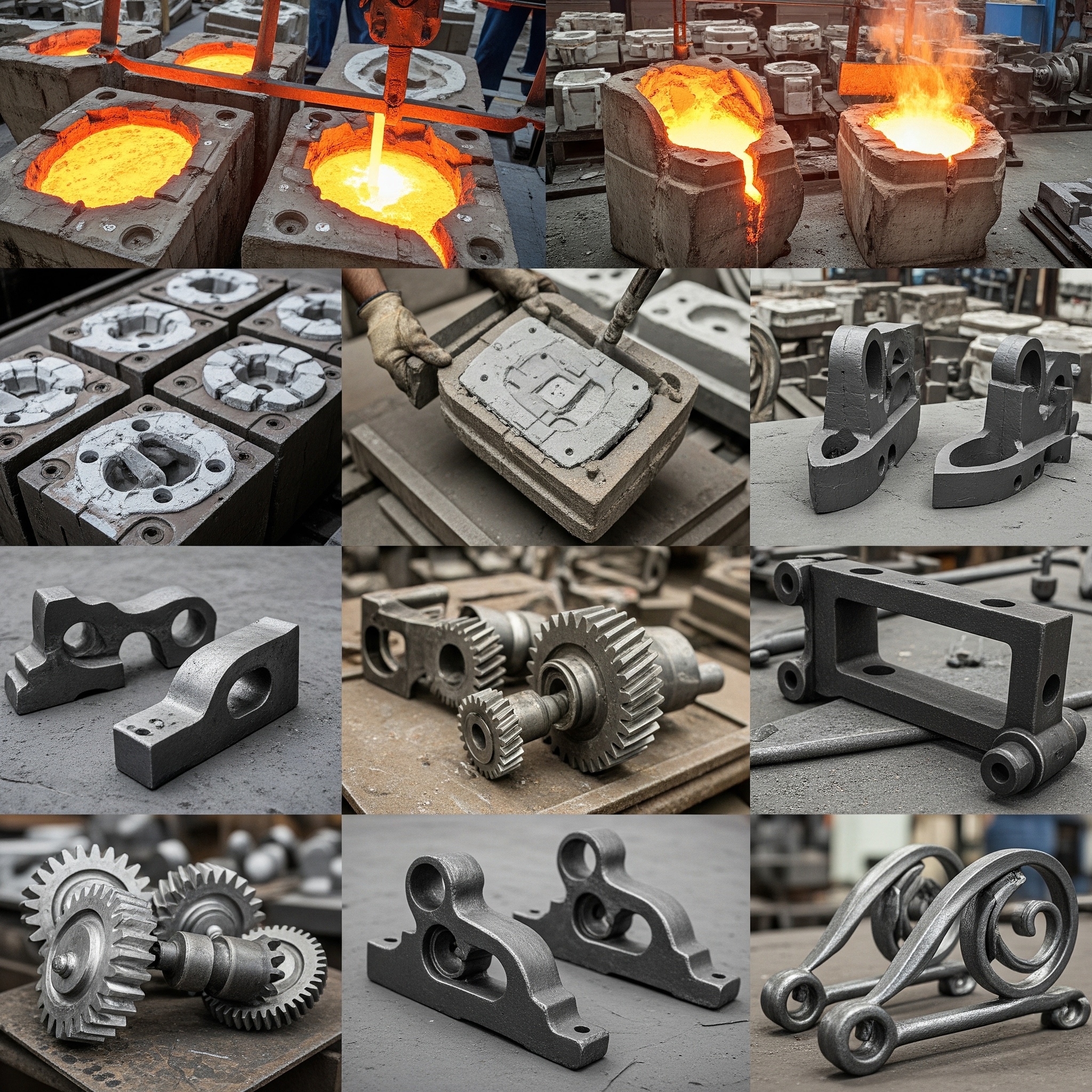
Sustainability
Sand casting is good for the environment if you use energy and materials wisely. Studies show sand casting can lower harm to nature when you manage waste and energy well. A carbon model checks energy, materials, and gases at each step. This helps you find ways to lower pollution and make your process better.
A study on aluminum sand casting shows good results. Using hydropower can cut pollution by about 40%. Reusing sand can lower solid waste by 91%. These changes can cut total pollution by 67%. Sand casting helps you make things in a way that is better for the earth.
Here are some important facts about sand casting and the environment:
Metric | Description | Importance |
---|---|---|
Energy Efficiency | How well energy is used in making parts | Lowers costs and helps the environment |
Waste Management | How well waste is reduced and recycled | Makes work safer and better for nature |
Carbon Footprint | Total greenhouse gases made | Shows how much you affect the environment |
Compliance with Environmental Regulations | Following rules for the environment | Keeps you legal and helps the planet |
Most of the sand can be used again. This means less waste and saves materials. When you pick sand casting, you choose a way that cares about both quality and the earth.
Sand Casting Advantages and Limitations
Surface Finish
Sand casting lets you make many designs. But, you should think about the surface finish. Sand cast parts often feel rougher than parts made with other methods. This is because sand grains leave small marks on the metal. You might see tiny bumps and dips on the surface. People measure roughness using RMS values. A lower RMS number means a smoother finish.
You can make the surface smoother by using finer sand grains or special resin coatings. For example, shell sands with more resin make smoother surfaces. How you pack the mold also matters. Machines and jolt-squeeze methods give a better finish than hand packing. The metal you use changes the look too. Aluminum castings usually look smoother than iron or steel. This is because aluminum melts at a lower temperature.
Tip: If you want a smoother part, ask for extra steps like grinding, sandblasting, or coating. These steps help you meet strict looks or performance needs.
A rougher surface may need more work after casting. This is a main disadvantage of sand casting if you need a very smooth part. But, you can balance sand grain size and packing to get the best result for your project.
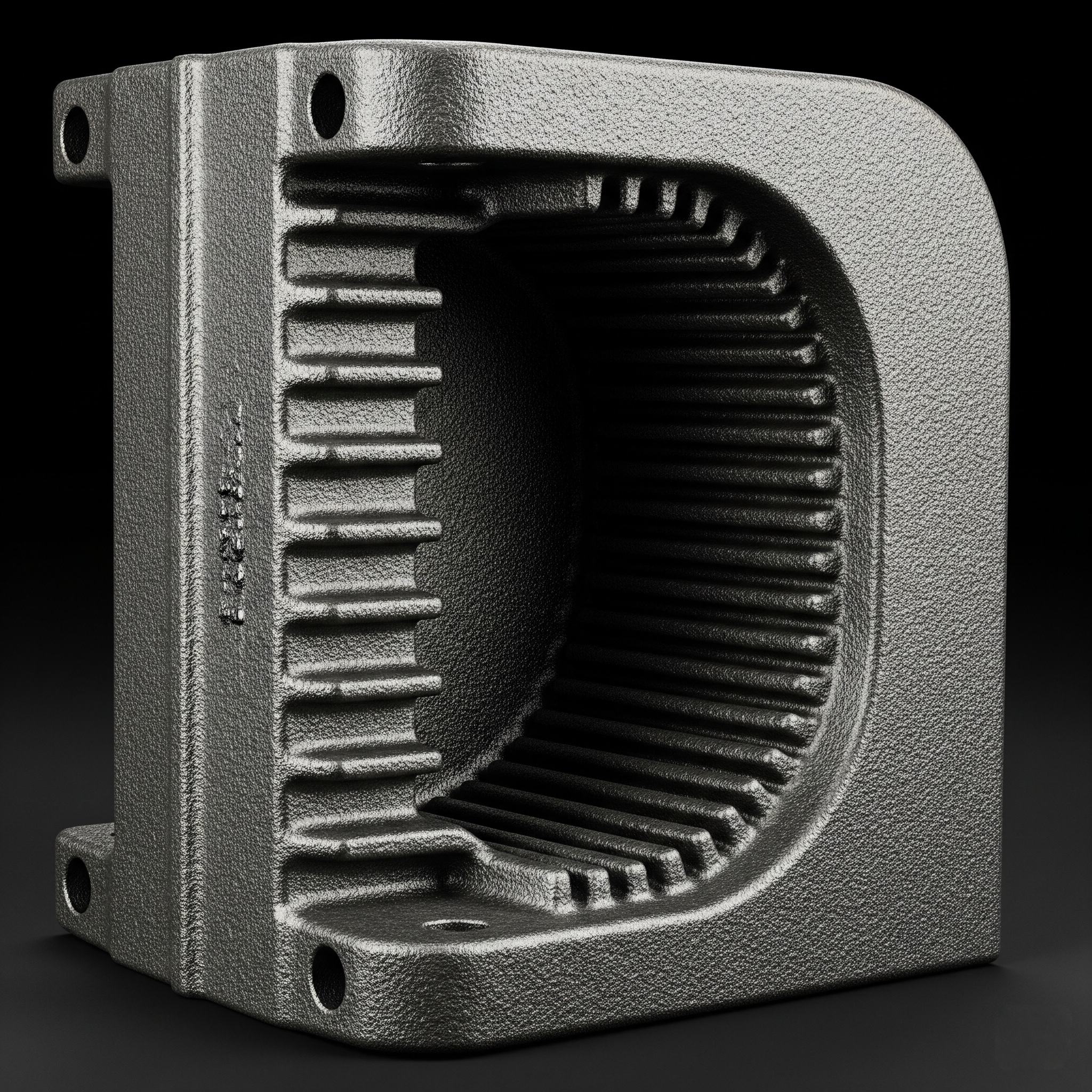
Dimensional Accuracy
Dimensional accuracy means how close your part is to your design. In sand casting, you might see small differences between the drawing and the finished part. These differences come from how the sand mold is made, how the metal cools, and how the part is handled after casting.
You can use tools like calipers, micrometers, and 3D scanners to check the size of your parts. Fast 3D scanning lets you compare the part to your CAD model. This helps you find mistakes quickly. Ceramic sand cores give better accuracy than regular sand, especially for hard shapes.
Things that affect accuracy include:
- Shrinkage when cooling
- Mold shift or bending
- Handling after casting
- Pattern and mold design
You can get better accuracy by using machines, careful mold design, and checking parts often. AFI Industrial Co., Ltd. uses advanced tools and strict checks to keep parts within tight limits. Still, you may need some machining after casting to get the best precision. This is another disadvantage of sand casting, especially for parts that need exact sizes.
Mechanical Properties
Mechanical properties show how strong and tough your sand cast parts are. These depend on the metal you pick, the mold type, and the casting process. You want your parts to handle stress, bending, and hits during use.
Mechanical tests, like bending and compression, show how parts act under force. These tests measure strength, hardness, and how much a part bends before breaking. Stresses can form inside the part as it cools. These come from uneven cooling or shrinking. You can use computer tests and load tests to check for these hidden stresses.
You can make parts stronger by controlling the sand mix, moisture, and pouring temperature. The right moisture in the sand helps stop cracks and makes the mold stronger. Naturally bonded sand molds often work better for aluminum alloys. Heat treatments and surface finishing after casting also make parts stronger and tougher.
Note: If your part needs to handle heavy loads or tough jobs, talk to your casting provider about the best metal and process. Careful control of each step helps you avoid problems like lower strength or hidden defects.
The advantages and limits of sand casting depend on what you need. You save money and get design freedom, but you must manage surface finish, accuracy, and strength. By knowing these things, you can make the best choice for your project.
Defects and Challenges
When you use sand casting, you can run into problems. Some common problems are porosity, shrinkage, blow holes, cold shuts, misruns, and sand inclusions. These problems can make your parts weaker or lower their quality. Most of these issues happen because of how you design the gating and feeding system or how you control the sand and metal.
A study showed that almost 90% of casting problems come from bad gating and feeding system design. If you do not design these systems well, you might get more shrinkage, porosity, or parts that do not fill right. The sand you use is also important. If the sand has too much clay or the wrong grain size, you can get sand inclusions or rough surfaces. For example, using sand with 52.7% clay caused many problems, but you should use much less clay.
You can look at the table below to see the main types of defects and what causes them:
Defect Type | Main Cause | How to Reduce Risk |
---|---|---|
Porosity | Poor sand permeability, high moisture | Control sand mix and moisture |
Shrinkage | Bad gating/feeding design | Use proper risers and feeders |
Blow Holes | Gas trapped in mold | Improve sand venting |
Cold Shuts/Misruns | Low pouring temperature, slow fill | Keep metal hot, pour quickly |
Sand Inclusions | Too much clay, coarse sand | Use correct sand grain and binder |
You can lower the chance of defects by using casting simulation software. This software lets you test your design before making the mold. You can also control the sand better, check the pouring temperature, and look at molds before pouring metal. These steps help you avoid extra work or wasted materials.
AFI Industrial Co., Ltd. uses advanced simulation and strict controls to help you get good castings. Their team checks sand quality, mold design, and pouring steps at every stage. This helps you get strong and high-quality parts.
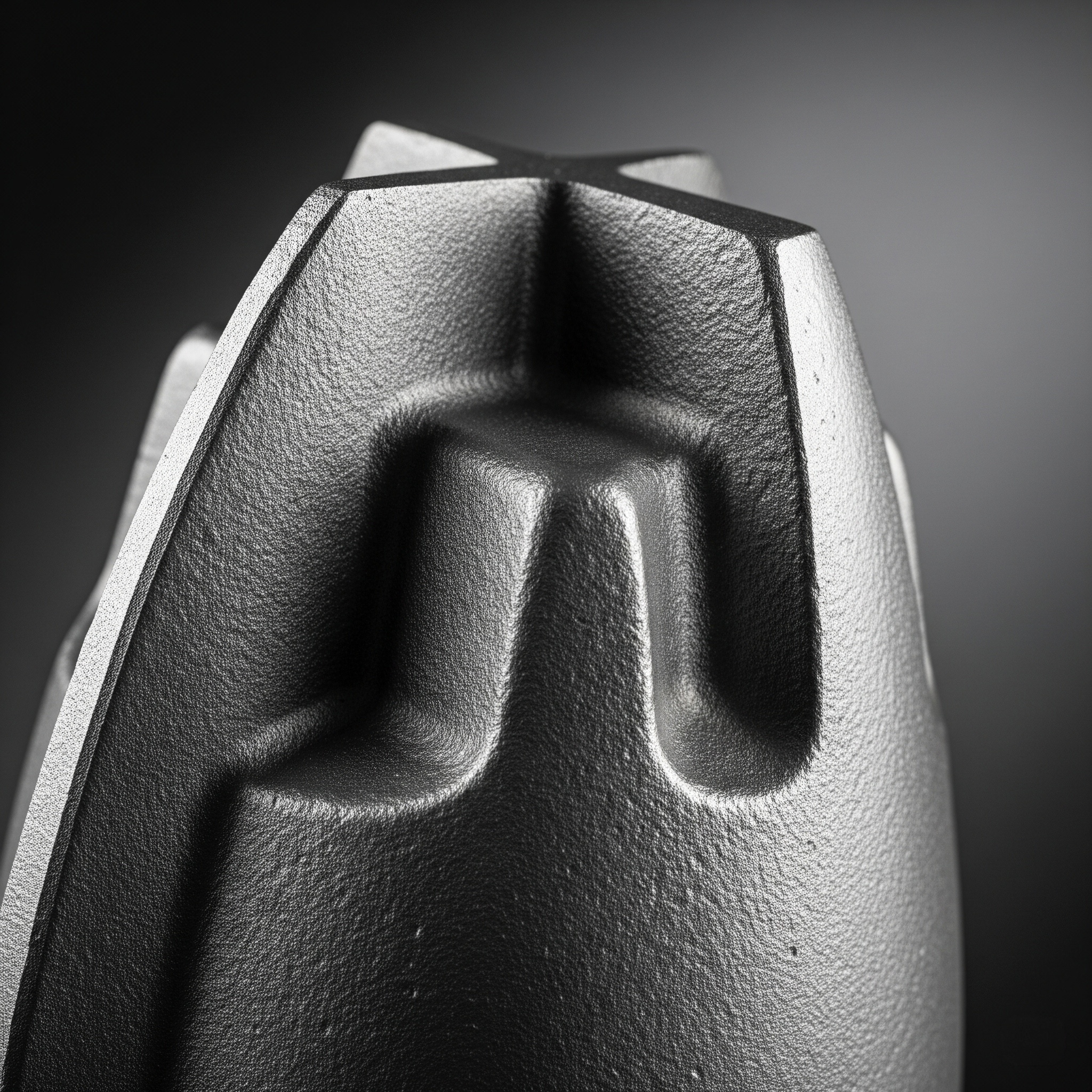
Pattern and Mold Management
Taking care of patterns and molds helps you make better castings and avoid problems. You need to think about how you design, build, and care for your patterns and molds. Here are some good tips you can follow:
- Add draft angles (1-3 degrees) to your patterns. This makes it easier to take the pattern out of the sand.
- Use fillets and rounded corners. These help stop cracks and lower stress in your castings.
- Put parting lines in smart places. This helps metal flow better and lowers the chance of problems.
- Design core prints carefully. Good core prints keep cores in place during casting.
- Make your patterns a bit bigger to allow for metal shrinkage as it cools.
- Pick the right material for your patterns. Wood, plastic, or metal can work, depending on how many parts you need and how hard the shape is.
- Check and fix your patterns often. This keeps them in good shape and helps you avoid mistakes.
Modern tools make pattern and mold management easier. You can use CNC machines or 3D printers to make patterns with high accuracy. Simulation software lets you see how metal will flow and cool in your mold. This helps you find problems before you start casting.
You should also check your molds for cracks, porosity, or parts that did not fill right. Use 3D scanning or X-ray tools to find hidden problems. Checking and fixing your molds often keeps them working well and helps you make good parts every time.
AFI Industrial Co., Ltd. uses these new techniques to help you get the best results. Their team uses strong materials, modern machines, and careful checks at every step. This helps you avoid problems and keeps your casting process smooth and reliable.
Sand Casting vs Other Methods
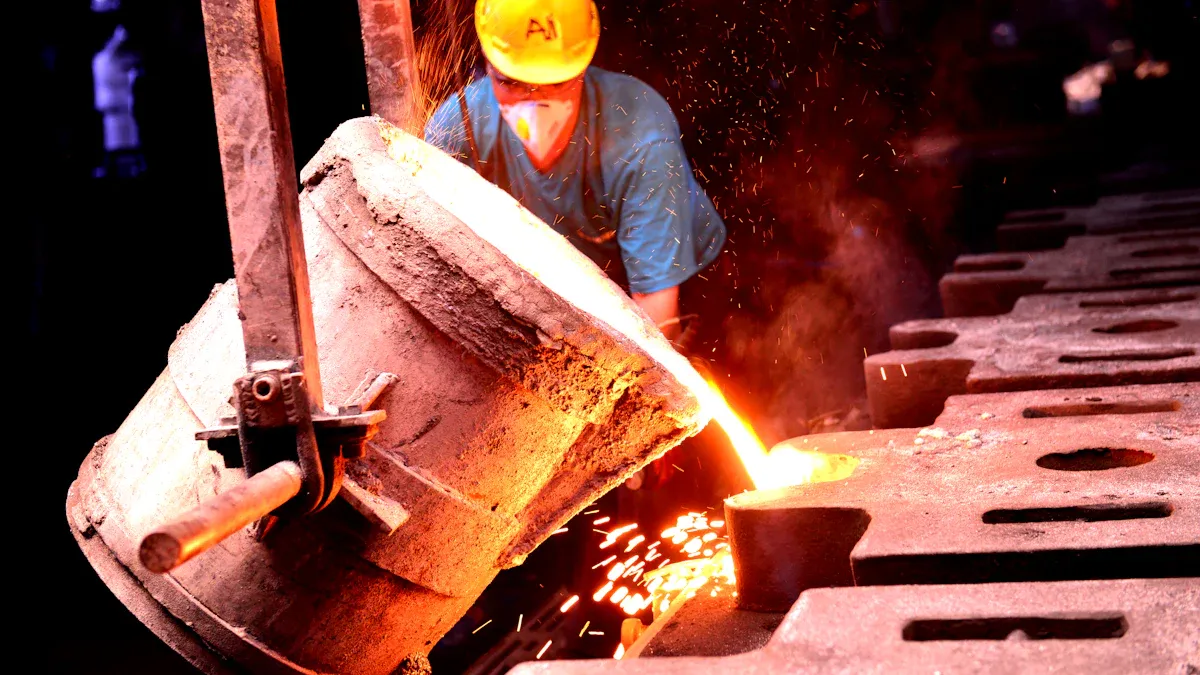
Die Casting Comparison
Sand casting and die casting are different in many ways. Sand casting is good for making a few parts or big parts. You can change your design without spending a lot. The tools for sand casting do not cost much. Die casting uses metal molds and high pressure. This makes parts with smooth surfaces and exact sizes. Die casting costs more at first but is better for making lots of parts fast.
Here is a table that shows how they compare:
Performance Metric | Sand Casting | Die Casting |
---|---|---|
Cost-effectiveness | More cost-effective for low-volume production | Higher initial tooling cost, better for high volumes |
Surface Finish | Rougher surface finish | Smoother surface finish |
Dimensional Accuracy | Lower, needs more finishing | High, minimal finishing needed |
Production Speed & Volume | Slower, mold remade each run | Faster, highly automated, high volumes |
Strength & Durability | Prone to porosity, less fatigue resistance | Denser, stronger castings |
Environmental Impact | More waste and emissions | Less waste, higher energy use |
Design Complexity | Handles large, complex parts | Best for detailed features, tight tolerances |
Customization | Ideal for one-off or low-volume runs | Suited for repeat runs with reusable molds |
Repairability | More repairable | Less repairable |
Pick sand casting if you want to save money and need only a few parts. It is also good if you want to change your design. Choose die casting if you need many parts that look nice and fit together well.
Investment Casting Comparison
Sand casting and investment casting are not the same. Sand casting is simple and works for big parts. It does not cost much and you get your parts faster. But, you may need to do more work to make the part smooth or the right size.
Investment casting is good for small parts with thin walls. It makes parts with smooth surfaces and exact sizes. You can use many metals and change designs fast with wax patterns. But, it costs more and takes longer, especially for big parts.
- Sand Casting Advantages:
- Easy way to make big parts
- Costs less to make
- Parts are ready faster
- Sand Casting Disadvantages:
- Parts feel rough
- Not as exact, needs more work
- Investment Casting Advantages:
- Makes small, tricky shapes
- Parts are smooth and exact
- Works with many metals
- Investment Casting Disadvantages:
- Costs more money
- Takes more time
- Not good for big parts
Pick investment casting if you need small, detailed parts that must be very exact. Sand casting is better for big, simple parts when you want to save time and money.
Permanent Mold Casting Comparison
Permanent mold casting uses metal molds again and again. This way gives you parts that are smoother and more exact than sand casting. The parts are stronger because the metal cools quickly. But, the molds cost more, so this way is best if you need many parts.
Here is a table to help you compare:
Aspect | Sand Casting | Permanent Mold Casting |
---|---|---|
Linear Tolerance | 0.030 inch for first inch + 0.002/inch | 0.015 inch for first inch + 0.002/inch |
Concentricity Tolerance | 0.050 inch for diameter up to 5 inch + 0.005/inch | 0.025 inch for diameter up to 5 inch + 0.003/inch |
Surface Finish (RMS) | 300-560 (nonferrous), 560-900 (ferrous) | 200-420 (smoother surface) |
Tooling Cost | Low, ideal for low-volume | Moderate, ideal for moderate volume |
Use sand casting if you only need a few parts or want to test your design. Pick permanent mold casting if you need many parts that must be smooth and exact. Sand casting lets you use more metals and make hard shapes. Permanent mold casting is better for making lots of strong, high-quality parts.
When to Use Sand Casting
Ideal Scenarios
Pick sand casting if you want to save money and use many metals. This method works for both easy and hard shapes. It is good for making test parts or small groups of parts. You do not need to spend a lot on tools. If you need more parts later, you can make them too.
Many companies use sand casting for medium or big parts. For example, it is used for pump impellers, engine blocks, and machine housings. Using computer programs helps you make better molds and castings. You can change how fast and hard the metal goes in. This helps stop problems like air bubbles and holes. It also makes mold making faster and parts better.
Sand casting is good if you need to watch your spending. You can look at old casting jobs to guess the cost for new ones. This helps you pick the best way to make your part. Sand casting is smart if you want good quality, fast work, and low prices.
If you care about the earth, sand casting can help. Using special sands can cut down on bad gases. You can use the sand again and pick clean energy. These things make sand casting a good choice for companies that want to help the planet and get good parts.
Tip: Sand casting is best if you need tricky shapes, want to use many metals, or need cheap test parts and small batches.
When to Avoid
Do not use sand casting if you need perfect surfaces or very exact sizes. Sand molds can cause small mistakes or weak spots. These problems can make your parts less strong or safe. If you need parts for planes or medical tools, sand casting may not be right.
Studies show sand molds can have flaws that make parts weak. Bad vents in the mold can even cause explosions. Even with safety steps, some risks stay if you cannot control the mold well. Do not use sand casting if any mistake could cause danger or failure.
Pick other casting ways if you need:
- Very smooth parts that need little extra work
- Super exact sizes
- Strong, perfect parts for important jobs
- The safest parts with almost no risk from casting
Note: Always check what your project needs for quality and safety before picking sand casting. If you cannot have any mistakes, look at other casting methods.
Cost and Quality Factors
Cost Drivers
It is important to know what makes sand casting cost more. Many things can change how much you pay for each part. If you learn about these, you can make smart choices and keep your spending low.
- Raw Materials: The kind and amount of metal you pick changes the price. You also need to think about the sand, binders, and additives for the mold.
- Labor and Machine Time: Workers spend time making molds, pouring metal, and finishing parts. This adds to your costs. How long machines run and how often they work also matter.
- Design Complexity: Parts with thin walls or tricky shapes take more time and effort. If your design is hard, it can use up to 80% of your total cost. Plan your design carefully to save money.
- Post-Treatment: After casting, you might need to clean sand off, fix the surface, or reshape the part. These steps depend on what your part looks like and how good it needs to be.
- Energy and Equipment: Running furnaces and machines uses power and fuel. If you work all day and night, you can make more parts and lower the cost for each one.
- Management and Overhead: You also pay for managers, buildings, and shipping. These costs depend on how heavy and how many parts you order.
- Yield and Scrap: If you throw away a lot of parts or need to fix them, your costs go up. Making less waste helps you save money.
Tip: You can spend less by making your machines work better, getting good deals on energy, and using cost models to find problems. Checking your process against others helps you see where to save.
Quality Control
Quality control makes sure your parts are always good. You want to stop scrap, fixing mistakes, and defects because these cost more and slow you down. A strong quality system helps you give customers parts they can trust.
- Inspection Methods: You should look at parts, test them in different ways, and check random samples. These steps help you find problems early.
- Statistical Process Control (SPC): Use charts to watch pouring temperature and other steps. For example, you can track each batch with X-bar and R charts to see changes quickly.
- Process Capability: Check if your process stays close to your specs. Numbers like Cp and Cpk show if your process is steady. If Cp is above 1.33, your process is doing well.
- Continuous Improvement: Teach your team, reward good work, and help everyone work together. This builds a culture of quality and keeps standards high.
- Defect Reduction: Using SPC and better testing can cut mistakes by 30% and help you find more defects. Some foundries have dropped defect rates from 5% to 1% in important parts like engine blocks.
- Quality Circles: Get your workers to help solve problems and make things better. Their ideas and experience can help a lot.
Quality Control Parameter | Monitoring Frequency | Statistical Method / Benchmark |
---|---|---|
Pouring Temperature | Every batch | Control charts (X-bar, R charts) |
Dimensional Measurements | Random samples per run | Cp, Cpk (Cp > 1.33 = high capability) |
When you focus on quality, you spend less by making less waste and fixing fewer mistakes. You also earn trust from your customers and get a better name in the market.
common defects and solutions
Defect Prevention
You can stop most casting problems by using the right steps and tools. Many factories see the same problems, like porosity, shrinkage, gas bubbles, and rough surfaces. These problems often happen because of temperature changes, bad molds, or mistakes when pouring metal.
Here are some ways to lower defects:
- Always use the same casting steps. This keeps your results steady.
- Use sensors to watch temperature, pressure, and pouring speed as you work.
- Check molds, patterns, and sand often. Look for cracks or damage.
- Use X-ray or ultrasonic tests to find hidden problems inside castings.
- Write down what happens in each casting run. This helps you see what works.
- Teach your team how to spot and stop defects. Skilled workers find problems fast.
- Check and fix your tools and molds often. This stops mold shift or loose pins.
- Use tools like fishbone diagrams or the 5 Whys to find the real cause of defects.
- Make sure you get good sand and metals from your suppliers.
- Ask everyone to share ideas to make the process better.
Tip: Lean Total Quality Management and Total Productive Maintenance help you track and cut defects. Use Statistical Process Control charts to watch your process and catch problems early.
A new study showed that using a special binder on sand molds cut porosity by 66.7%. Porosity dropped to 3.73%, and the alloy did not react with the mold. This shows that changing your process can really help casting quality.
Surface Improvement
You can make the surface of sand cast parts better with a few steps. Flaws like pinholes, burrs, scabs, and rough spots can happen if you use coarse sand or pack the mold badly. These flaws can change how your part looks and works.
Try these ways to get a smoother surface:
- Use finer sand or resin-coated sand for smoother molds.
- Put coatings on molds to stop metal from sticking or reacting.
- Control sand moisture and how tightly you pack it to stop cracks and veins.
- Use machines to pack and shake molds for an even surface.
- After casting, use sandblasting, grinding, or polishing to smooth rough spots.
- Check each part by looking and using tools to find surface problems early.
- Keep molds and patterns clean and in good shape.
A strong quality control system helps you find and fix surface problems fast. Non-destructive tests and regular checks keep your process working well. When you work on both stopping defects and making surfaces better, you fix the most common sand casting problems.
Note: Keep training your team and watching your process to keep making your casting quality better.
Sand casting lets you pick many designs and materials. You can make a few or many parts. This way helps you save money, especially for small jobs. It also makes less waste. One company saved $57,000 each year by using sand casting instead of machining. But, sand casting parts can feel rough and may not be as exact as other ways. Think about how smooth and accurate you need your parts to be. If you want help, talk to AFI Industrial Co., Ltd. > You can also read guides or ask casting experts for more information.
Summary of the advantages and disadvantages of sand casting
Advantages of Sand Casting
- Cost-effectiveness: Inexpensive materials and lower tooling costs, especially for high-volume production.
- Versatility in size and complexity: Can produce parts from ounces to tons, including intricate internal and external shapes.
- Excellent material flexibility: Compatible with nearly any alloy (iron, steel, aluminum, brass, bronze, etc.).
- Ability to produce large and heavy parts: Ideal for large components in industries like automotive and heavy machinery.
- Good surface finish and dimensional accuracy: While not as precise as some other casting methods, sand casting can still achieve acceptable levels for many applications, and secondary machining can further improve these.
- Recyclability of molding materials: The sand used in the process can often be reconditioned and reused, which is environmentally friendly and reduces material waste.
- Adaptability to design changes: It's relatively straightforward to modify patterns for design adjustments, offering flexibility during the development phase.
- Reduced lead times for prototypes: Compared to more complex tooling methods, sand casting can produce prototypes relatively quickly, speeding up product development cycles.
Disadvantages of Sand Casting
- Lower dimensional accuracy and surface finish: Often requires additional machining to meet precise specifications, increasing post-processing costs and time.
- Potential for casting defects: Susceptible to issues like sand inclusions, gas porosity, blowholes, and misruns, which can compromise part quality and strength.
- Labor-intensive: Can involve significant manual effort for mold preparation and core setting, particularly for complex parts, leading to higher labor costs and longer production cycles.
- Tooling wear: Patterns can degrade over very long production runs, requiring periodic maintenance or replacement, which adds to long-term expenses.
- Environmental considerations: The process can generate dust and require proper disposal of spent sand and binders, raising environmental concerns if not managed correctly.
- Limitation on thin sections: Achieving very thin wall sections can be challenging due to the relatively lower fluidity of molten metal in sand molds compared to other casting methods.
- Rougher surface finish: Generally produces a coarser surface compared to investment or die casting, necessitating more extensive post-processing for aesthetic or functional requirements.
FAQ
Sand casting works with many metals. You can use cast iron, steel, aluminum, copper, and different alloys. This means you can choose the best metal for your project.
Sand cast parts are usually pretty accurate. Advanced controls help make them better. Most parts meet normal size limits. If you need very tight fits, you might need extra machining.
You can make complex shapes with sand casting. It allows for undercuts, thin walls, and inside spaces. You can also change molds fast if you want a new design.
Getting a prototype can take about 3 days. Making lots of parts can take up to 15 days. The time depends on how big, tricky, or many parts you need.
Sand casting can be good for the environment. You can recycle sand and use less energy. Many foundries follow rules to lower pollution and save resources.
Many industries use sand casting. It is common in cars, planes, building, machines, and electronics. Sand casting works for both small and big parts in these fields.
Most sand cast parts need extra steps after casting. You may need to clean, grind, or treat the surface. These steps help the part look better and work well.
Quality is checked with special tools and careful steps. Skilled workers use 3D scanning and other tests. AFI uses these checks to make sure every part is good.