Manual pipe bending is often the most cost-effective tube bending solution for small batch production. CNC tube benders and hydraulic tube benders offer high precision and flexibility, making them ideal for complex or tight-radius projects. Each method suits different requirements, so it’s important to consider material, shape, and cost before making a decision. AFI Industrial Co., Ltd. is a trusted partner for custom tube bending, consistently delivering excellent results with cost-effective tube bending solutions for small batch production.
Key Takeaways
- Manual tube benders are the cheapest and easiest way. It works best for small jobs. It is good for soft metals and simple shapes.
- CNC pipe bending uses computers to make exact bends. It is great for tricky shapes and medium-sized batches.
- Hydraulic pipe bending is strong and fast. It works well for thick or hard pipes. It is good for small to medium jobs that need power and control.
- Picking the right bending method depends on the pipe material. It also depends on how hard the bend is, the job size, and your budget. This helps save time and money.
- AFI Industrial Co., Ltd. gives expert advice and advanced machines. They offer flexible services to help customers get good bends. You do not need to buy costly equipment.
- Setting up carefully and checking quality lowers mistakes and waste. This cuts extra costs and makes parts better.
- Using the right tools and taking care of them stops problems like wrinkles and cracks. This saves money and keeps pipes strong.
- AFI helps with custom orders from one pipe to many. They work fast and help with design to fit different project needs.
Table of Contents
Pipe Bending Methods
Manual Bending
Manual tube benders uses a simple tool you move by hand. This way works well for small jobs and when you need to work at the job site. Manual benders are small and light, so you can carry them easily. Many people pick manual bending because it costs less and is easy to set up. You do not need power or big machines for this. However, this is sometimes done with the aid of pneumatic structures.
- Both new and skilled workers can use bending machine with little practice.
- The tool makes bends that look the same, so pipes stay strong and flow stays smooth.
- Manual bending is good when you only need a few parts or need to change things fast.
- It is a simple way to save money on pipe bending for small batches.
CNC Bending
CNC Tube Benders use computer controlled machines. These machines bend pipes into precise shapes according to set instructions, bending demands. CNC pipe bending machines are widely used in areas such as automotive manufacturing, aircraft manufacturing, and medical devices.
- CNC machine production bending process is always the same and very precise, so the bending result won’t leak or break.
- Using machines saves on worker costs and makes things faster.
- Workers can save programs for jobs they do again, so it is easy to make the same thing many times.
- CNC bending can make hard shapes and tight bends, which are needed for tough jobs.
- AFI Industrial Co., Ltd. uses top CNC benders to give custom and flexible pipe bending.
Hydraulic Bending
Hydraulic pipe bending uses liquid power to bend pipes. This way gives both strength and control, so it works for many kinds of pipes and shapes. Hydraulic benders can be part-automatic or all automatic.
- Hydraulic machines push harder than hand tools, so they can bend thick or tough pipes.
- They let you control the bend well, so you waste less and each part matches the plan.
- Workers can use screens and set programs to make bending easier and quicker.
- Hydraulic bending is good for small or medium jobs that need to be done the same way each time.
- AFI Industrial Co., Ltd. uses the best hydraulic benders with CNC to do hard jobs and give steady results.
Tip: Pick the right pipe bending way by thinking about how big the job is, what the pipe is made of, and how hard the shape is. AFI Industrial Co., Ltd. gives smart advice and great tools to help you choose the best way for your job.
Cost-Effective Pipe Bending Solutions for Small Batch Production
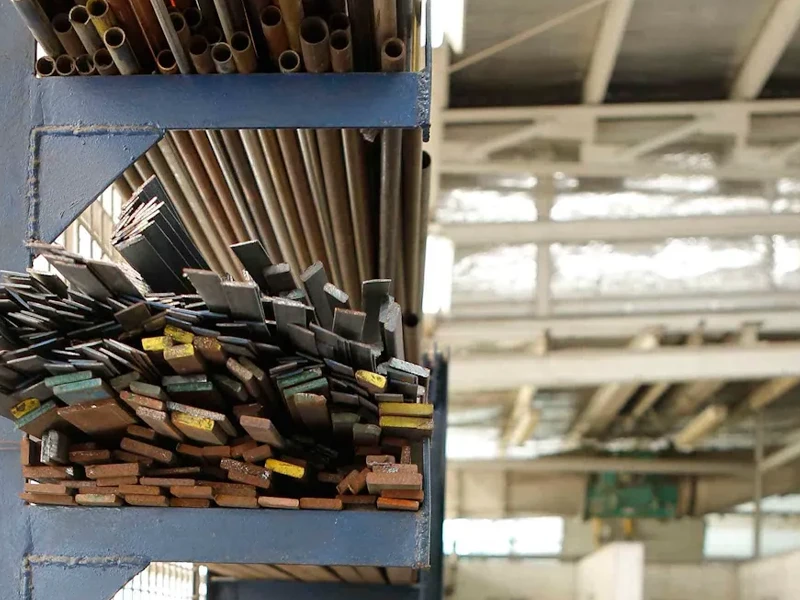
Equipment and Setup Costs
Manual bending tools are the least expensive to buy and install. You can buy a manual pipe bender for a fraction of the cost. This tool is good for small production volumes or when you need to get started quickly. CNC benders and hydraulic benders require specialised machines. These machines have a higher initial cost, but are more controllable and bend more accurately. Companies such as AFI Industries, Inc. use these automation machines. They can bend a variety of tubes and shapes. For smaller jobs, AFI helps customers save on high start-up costs by offering flexible services. Customers don’t have to buy expensive machines to get the job done with AFI’s tube bending tools!
Note: Picking the right tool saves money and time, especially for small orders.
Labor and Training
Manual bending is easy to learn. Most workers can use a hand bender after a short lesson. This way does not require special skills or computer use. CNC and hydraulic bending need trained workers. These workers must know how to set up machines and use programs. Learning takes longer and costs more. AFI’s team has skilled workers for both CNC and hydraulic benders. Customers do not need to train their people. AFI’s experts do the bending and make sure every part is right.
Cost per Part
Manual bending is cheap for very small batches. If you only need a few bends, this way saves money. CNC and hydraulic bending get cheaper as you make more parts. These machines are suitable for high volume production for fast and accurate tube bending. The price for each part goes down when you buy more at once. AFI Industrial Co., Ltd. picks the best way for each job to save money. Their system lets customers order any amount, from one to hundreds. AFI’s process reduces waste, lowers costs, and shortens the production cycle, even for products with hard shapes or small curvatures.
Method | Equipment Cost | Training Needed | Cost per Part (Small Batch) | Best For |
---|---|---|---|---|
Manual | Low | Low | Low | Simple, few parts |
CNC | High | High | Medium-Low | Complex, repeat orders |
Hydraulic | Medium-High | Medium | Medium | Thick pipes, precision |
AFI’s custom pipe bending service helps companies save money on small batch jobs. Customers do not pay for machines, training, or extra workers. They also get strong, well-made parts fast.
Tip: To get the best deal, work with a company like AFI Industrial Co., Ltd. Their skill and top machines help lower costs and make every order better.
Precision and Quality
Accuracy
Accuracy means each pipe bend matches the plan exactly, directly impacting bending quality. Manual tools can do well with easy shapes, but they may not be as exact. CNC and hydraulic machines are much more accurate. CNC benders, like those at AFI Industrial Co., Ltd., can bend pipes to within ±0.1°. This makes sure every pipe fits just right, ensuring superior bending quality.
Here is a table that shows how accurate different methods are:
Metric / Parameter | Compression Bending (CB) | Rotary Draw Bending (RDB) | Notes / Tolerance Details |
---|---|---|---|
Positional accuracy for cuts | ±6 mm (±1.5°) | ±6 mm (±1.5°) | Template, marking, and cutting misalignments |
Springback angle standard deviation | 0.142° | 0.043° | RDB shows smaller spread in springback angles |
Average springback difference | 0.2° to 0.6° | 0.2° to 0.6° | RDB has less variability |
AFI’s CNC machines also keep pipe sizes within ±0.01mm. This is very important for things like planes and medical tools. Even tiny mistakes can cause big problems. Workers use digital tools to check every bend. They make sure each part is just right.
Consistency
Consistency means every pipe in a group is the same. Manual bending can make small changes from one pipe to another. CNC and hydraulic machines use computers to keep every bend the same. AFI checks pipes while making them to catch mistakes early.
- CNC back gauges put pipes in the right spot for each bend.
- Pressure is set for the pipe material, so bends stay the same.
- Workers use angle finders and lasers to check bends.
- Checks during work help find problems fast.
Mandrel and rotary draw bending help keep pipes smooth and even. Good tools and the right oil help make bends better. AFI checks materials, watches the process, and looks at finished pipes. This helps them get a 99.5% good rate for bending.
Complex Bends
Complex bending processes have tight curves, many angles, or go in different directions. Manual tools have trouble with these bends. CNC and hydraulic machines can do these hard bends very well. AFI’s CNC benders can make bends in many directions and test designs before making them. This saves time on new parts.
Pipe Bending Method | Performance Data / Features | Accuracy and Complexity Support |
---|---|---|
CNC Bending | Positioning accuracy of ±0.1°; repeatable multi-plane bends; CAD integration | Supports complex, repeatable bends with minimal error |
Mandrel Bending | Maintains circular cross-section; tight radii as small as 1D | Handles thin-wall and tight-radius bends without deformation |
Induction Bending | Precise temperature and pressure control | Maintains material strength during complex bends |
AFI’s machines can bend pipes with curves as small as 0.3mm. This helps make special parts for jobs that need both skill and careful work. Their team uses computer tools and checks bends as they go to make sure each one is perfect.
Tip: If your project needs very exact or tricky bends, CNC and hydraulic bending from AFI Industrial Co., Ltd. are the best choice. Their skilled team and top machines help you get great results every time.
Tolerance Standard
Tolerance standards are rules for how close pipes must be to the plan. These rules help pipes fit and work well in their final spot. AFI Industrial Co., Ltd. follows strict tolerance standards for every part.
- Tolerances are the allowed size difference from the plan. This helps parts fit together without gaps or being too tight.
- The weld seam should be at the neutral axis, on top or bottom of the bend. This helps stop cracks, especially in sharp bends.
- The wall factor is the pipe’s outer diameter divided by its wall thickness. Thin walls need more support so they do not wrinkle or collapse.
- The outside of a bend can get up to 33% thinner. This depends on the bend radius and the tools used.
- Bend radius is measured by the pipe’s diameter. For example, a 2D bend radius for a 3-inch pipe means a 6-inch curve. Bigger numbers make bending easier.
- Drawings for each part show the material, size, tolerance, and weld seam spot. These details help workers and make quality checks easier.
AFI uses advanced machines to keep tight tolerances. Their CNC benders can bend angles within ±0.1° and pipe sizes within ±0.01mm. This control helps meet the needs of aerospace and medical device jobs.
Here is a table with important tolerance standards and checks:
Specification Aspect | Details / Numerical Tolerances |
---|---|
Applicable Standards | ASME B16.49, ISO 15590-1, API 5L, ASTM, API 1104, BS 5750 Part 2 |
Weld Seam Orientation | Weld seam at neutral axis; no circumferential welds |
Bend Length | Minimum 500 mm (≤24″ diameter), 750 mm (>24″ diameter) |
Dimensional Tolerances | OD reduction ≤ 2.5% nominal diameter; max OD difference ≤ 5% overall, ≤ 1% within 4″ of end |
Wall Thickness | Not less than minimum specified; checked by ultrasonic methods |
Bend Radius Accuracy | Radius of curvature within ±10.5% |
Bend Flatness | Max deviation 5 mm per 45° arc |
Visual Inspection | 100% inspection for defects; repaired areas checked by special tests |
Hardness Testing | Surface hardness ≤ 250 Hv235; checked at several points |
Note: Meeting these standards helps AFI make pipes that last longer and work better in tough jobs. Their careful checks and advanced tools keep every part within the right limits.
Setup and Learning Curve
Manual Setup
Manual tube benders use simple tools. Workers place the pipe in the bender, set the angle, and pull the handle. This process does not need electricity or computers. Most people can learn manual setup in less than an hour. The steps stay the same for each job. Workers check the angle with a protractor or angle finder. They adjust by hand if the bend is not perfect.
Key points for manual setup:
- Tools are light and easy to move.
- No special training needed.
- Setup time is short.
- Mistakes can be fixed quickly.
Tip: Manual bending works best for simple shapes and small batches. Workers can start right away with little practice.
CNC Programming
CNC pipe bending uses computers to control the machine. Workers enter the pipe size, bend angles, and other details into the computer. The machine follows these instructions to make each bend. Learning CNC programming takes more time than manual setup. Workers must know how to use the software and read technical drawings.
Steps in CNC programming:
- Review the pipe drawing.
- Enter the bend data into the CNC system.
- Set up the pipe in the machine.
- Run a test bend and check the result.
- Adjust the program if needed.
A table shows the main differences:
Aspect | Manual Bending | CNC Bending |
---|---|---|
Setup Time | Very Short | Moderate |
Skill Needed | Low | Medium to High |
Repeatability | Low | Very High |
Note: CNC programming allows for complex shapes and high accuracy. Workers need more training, but the results stay the same every time.
Hydraulic Operation
Hydraulic pipe bending uses fluid power. Workers set the pipe in the machine and choose the right die. They adjust the pressure and set the bend angle on the control panel. Some machines use simple buttons, while others have screens with more options. Learning to use hydraulic benders takes a few days. Workers must understand safety rules and how to set the right pressure.
Hydraulic operation steps:
- Select the correct die for the pipe.
- Place the pipe in the machine.
- Set the bend angle and pressure.
- Start the machine and watch the bend.
- Check the finished pipe for accuracy.
Safety Alert: Always follow safety steps when using hydraulic machines. High pressure can cause injury if not handled correctly.
Hydraulic benders work well for thick pipes and repeat jobs. Workers can make many bends with the same settings. This method gives strong, accurate bends with less effort.
Best applications
Manual Bending
Manual pipe bending is best for easy jobs with soft metals. It works well for small batches. Workers often use this method for copper or aluminum pipes. These pipes are usually less than one inch wide. Manual bending is good for projects that need up to 50 bends each month. Many HVAC and plumbing jobs use this method because it is quick and cheap. Custom shops and teams make new things such as manual bending. They use it when they only need a few parts.
Here is a table that shows when manual bending is the best choice:
Factor | Manual Pipe Bending Ideal Scenario | Cost Benefit / Notes |
---|---|---|
Material | Soft metals like copper and aluminum | Suitable for OD < 1 inch tubes |
Application Volume | Low-volume production (≤ 50 bends/month) | Low upfront cost ($200–$800), budget < $1,000 |
Bend Complexity | Simple bends (e.g., 90° bends) | Cost-effective for simple bends |
Industry Examples | HVAC, plumbing, custom fabrication, prototyping | Avoids high capital investment |
Required Skill | Human force and skill needed | Flexible and low cost |
Tip: Manual bending helps save money on small, easy jobs. AFI Industrial Co., Ltd. can help you pick the right tools and ways for these projects.
CNC Bending
CNC pipe bending is great for jobs that need high accuracy. It is also good for jobs that need the same shape every time. This way is best for projects with tight rules, like in planes, cars, or medical parts. CNC machines can remember how to bend each pipe. This means every part comes out the same. They work well for both small and medium batches. CNC bending is good when the design has many bends or angles.
- CNC benders make very exact bends, as close as ±0.05 degrees.
- They make every part look the same, even in small groups.
- Fast work and automatic loading help get more done.
- Multi-axis bending lets you make hard shapes and use different materials.
- You can change jobs quickly, so CNC bending is good for custom, low-number runs.
CNC bending makes sure every pipe meets tough rules. For example, a car part maker used CNC bending for brake lines. All the lines matched, so there was less waste and better safety. AFI Industrial Co., Ltd. uses top CNC machines for round, square, and odd-shaped pipes. Their team gives advice and works fast for custom jobs.
Note: CNC bending is best for jobs that need to be very exact and the same every time. AFI’s CNC services help customers get great results, even for hard designs.
Hydraulic Bending
Hydraulic pipe bending is good for jobs that need both power and flexibility. This way works for thick pipes and tough metals like carbon steel, stainless steel, and copper alloys. Hydraulic benders work up to 30% faster than manual tools. They keep bends close to ±0.1°. These machines can bend pipes with loads from 10 to 100 tons. This makes them good for big, heavy jobs.
Performance Metric / Feature | Hydraulic Pipe Bending Data |
---|---|
Bending Speed | Up to 30% faster than manual benders |
Precision Tolerance | Around ±0.1° |
Load Capacity | 10–100 tons |
Energy Efficiency | 20–30% less power used |
CNC Integration | Up to 100 bend sequences per setup |
Average Time per Piece | 30–40% lower than manual |
Material Compatibility | Carbon steel, stainless steel, copper, aluminum |
Hydraulic bending is good for small orders with hard bends, like in power work, new energy, or chemical jobs. AFI Industrial Co., Ltd. uses both hydraulic and CNC machines. This helps them make strong, exact bends for special shapes and big pipes.
Tip: If your job has thick pipes or hard bends, hydraulic bending gives speed and power. AFI’s team helps you pick the best way for your needs. They make sure you get good quality and work done fast.
Decision Guide
Key Factors
Material
The kind of tube material is very important in pipe bending. Soft metals like copper and aluminum bend without much effort. Harder metals, such as stainless steel or carbon steel, need more force and special tools. Wall thickness and how bendy the metal is also matter. Thick pipes or stiff metals may need hydraulic or CNC bending. Picking the right way helps stop cracks and keeps the pipe strong.
Complexity
Complexity means how many bends or angles a tube needs. Simple bends are easy to do with manual tube benders. Tubes with tricky shapes, tight curves, or many directions need CNC or hydraulic tube benders. Projects with lots of angles or special shapes work better with automated bending. This makes sure every tube matches the plan.
Volume
Volume is about how many pipes you need for your project. Small jobs or just one pipe often use manual bending. Medium or big jobs are cheaper with CNC or hydraulic bending. Machines save time and make every pipe the same. AFI Industrial Co., Ltd. can help with any batch size.
Budget
The budget decides which way is best for your job. Manual bending costs less for tools and learning. CNC and hydraulic machines cost more but save money on big or hard jobs. Using AFI’s service means you do not have to buy expensive machines. This keeps your costs low and your quality high.
Selection Flowchart
Picking the right pipe bending way is easier if you follow the steps. Use these steps to find what your project needs:
- Check Material Properties
- Find out the pipe’s metal type, wall thickness, and how bendy it is.
- Figure out the bend allowance and deduction to waste less.
- Review Bend Parameters
- Look at the bend radius, angle, and straight part needed.
- Decide if you need tight curves or just simple bends.
- Match Bending Technique
- Use manual bending for soft metals and easy shapes.
- Pick CNC bending for tricky, repeat, or multi-directional bends.
- Choose hydraulic bending for thick pipes or tough metals.
- Control Speed and Force
- Set the right speed and force to stop wrinkles or cracks.
- Inspect Quality
- Check for surface problems and measure bend angles.
- Test if the pipe is still round and do pressure tests if needed.
- Keep records so you can check back later.
Tip: Every job is different. For expert help and custom answers, talk to AFI Industrial Co., Ltd.’s engineering team. Their know-how helps you pick the best way and get great results.
Common Mistakes
Underestimating Setup
Many people think pipe bending setup is quick and easy. In reality, skipping careful setup can cause big problems. Workers must check every detail before starting. They need to choose the right pipe size, material, and bending method. If they miss a step, the project can face delays and extra costs.
- Using the wrong pipe size often leads to cracks, leaks, or even pipe failure. This mistake means more money spent on repairs.
- Picking the wrong material can cause rust or corrosion. Pipes may leak and need early replacement.
- Using the wrong bending technique can create uneven bends, wrinkles, or cracks. These problems slow down production and lower quality.
- Choosing the wrong bend radius can deform or kink the pipe. Workers then need to redo the job, which wastes time and money.
- Measuring angles incorrectly results in uneven bends. This mistake can delay the project and increase costs.
Tip: Careful setup helps avoid costly mistakes. Always double-check pipe size, material, and bend angles before starting.
Overlooking Costs
Some teams focus only on the price of tools or machines. They forget about hidden costs that add up during production. Labor, training, wasted material, and rework all affect the final price. When workers do not plan for these costs, the project budget can quickly run out.
- Manual bending seems cheap at first, but mistakes can lead to high scrap rates.
- CNC and hydraulic machines need skilled workers. Training takes time and money.
- Wrong setup or poor quality control increases the number of rejected parts.
- Extra material waste and repairs raise the total cost per part.
A simple table shows how hidden costs can affect a project:
Cost Factor | Impact on Project |
---|---|
Training | Increases startup costs |
Scrap/Rework | Raises material costs |
Labor | Adds to total expenses |
Downtime | Delays delivery |
Note: Smart planning and quality checks help keep costs low and projects on track.
Wrong Method Choice
Choosing the wrong pipe bending method can cause many problems. Each method works best for certain materials, shapes, and batch sizes. When workers pick the wrong one, they risk poor quality and higher costs.
- Thin-walled pipes may buckle or crease if not supported well.
- Pipes can lose their round shape, making them weak.
- Bends may show creases or cracks, hurting both looks and function.
- Hard materials can break if stretched too much or not prepared properly.
- Inaccurate bends make assembly hard and can cause leaks.
- Springback can change the bend angle, leading to errors.
- Wall thickness may change, causing weak spots.
- Scratches or grooves on the surface shorten pipe life.
- Using the wrong machine often leads to many defects.
- High waste and rejected parts drive up costs and slow down work.
Wrinkling and other defects often come from using the wrong bending speed, pressure, or mold. Poor lubrication and worn tools also cause problems. Quality checks like measuring ovality, wall thickness, and surface finish help catch these issues early.
Tip: Always match the bending method to the pipe material, shape, and job size. This choice helps ensure strong, accurate, and cost-effective results.
Maximizing Cost-Effectiveness
Streamlining Setup
Making the setup faster is very important for saving money in pipe bending. When teams spend less time setting up, they can start working sooner. This means machines are used more and not left waiting. AFI Industrial Co., Ltd. uses smart planning and digital tools to make setup easy. Their rapid prototyping lets customers try out designs before making lots of parts. This saves both time and money.
Some good things about faster setup are:
- Setup time is 36% shorter, so machines can work more.
- Making things goes up by 26% because the setup is quicker.
- Tool setup work drops from 6% to 2%.
- Making programs takes less work, from 4% to 1%.
- Machine setup work goes down from 6% to 3%.
- Entering data is easier, from 15% to 2%.
- Checking parts is a little faster, from 6% to 5%, because there are fewer test pieces.
- Labor costs per part go down as workers spend more time bending.
- Less scrap is made, especially in small jobs, because test pieces are not needed with offline simulation.
AFI can change orders fast, which helps when small jobs need changes. This is important because small batch jobs often change.
Reducing Scrap
Making less scrap is a great way to save money in pipe bending. Scrap is wasted metal, and it costs more and slows down work. In metalworking, scrap is the biggest way material is lost. When companies make less scrap, they use less metal and save energy. This also means they do not need to buy as much new metal, which saves money and helps the planet. New ideas, like better tools and careful planning, help lower scrap. AFI Industrial Co., Ltd. uses accurate machines and checks quality to keep scrap very low. Their way makes sure each part is good, so fewer parts are thrown away.
Tooling Tips
Picking the right tools and taking care of them helps save money and make better parts. AFI’s team picks the best dies and mandrels for every job. They check tools before each run to stop mistakes. Using the right tool for the pipe and shape helps stop wrinkles and cracks. Keeping tools clean and sharp means fewer problems and less waste.
Here are some easy tips for tools:
- Pick a die that fits the pipe size.
- Use mandrels for tight bends to keep pipes round.
- Put oil on tools to stop rubbing and damage.
- Check tools often and change broken ones fast.
- Keep tools dry and clean so they do not rust.
AFI’s way uses expert help, fast testing, and flexible work. This helps customers get pipe bending that saves money and keeps quality high.
FAQ
Manual pipe bending costs the least for very small jobs. It works best for easy shapes and soft metals. CNC and hydraulic bending are better when you need exact bends or tricky shapes. AFI Industrial Co., Ltd. helps people pick the best way for each job.
AFI checks quality at three steps. They look at materials before bending. They watch the process while bending. They check finished pipes at the end. Their CNC and hydraulic machines keep bends very close to the plan. This helps them get a 99.5% good rate for bending.
Yes. AFI can make custom pipes fast. They use rapid prototyping and flexible work. They can finish orders in 3 to 15 days. They take both small and big orders.
AFI bends many metals, like:
- Aluminum
- Copper
- Carbon steel
- Stainless steel
- Alloy steel
They also bend pipes in shapes like round, square, oval, and rectangular
CNC pipe bending uses computers to control machines. The machines follow set programs to make bends. Manual bending uses hand tools and worker skill. CNC bending is more exact and makes the same bend every time, even for hard shapes.
Tip: CNC bending is best for jobs that need very close bends or lots of the same part.
AFI lets you order just one pipe if needed. This helps people who want a sample or only a few pipes.
Ordering more pipes at once if possible:
- Giving clear drawings and details
- Picking the right metal for the job
- Asking AFI’s engineers for help with design
- Ordering more pipes at once, if possible
AFI can treat pipe surfaces in many ways to make them look better or last longer. These ways include:
- Anodizing
- Electroplating
- Spraying
- Brushing
- Sandblasting
- Polishing
AFI uses smart control systems. Their machines keep pipe sizes within ±0.01mm and bend angles within ±0.1°. They check pipes often with digital tools to keep these standards.
Customers can talk to AFI Industrial Co., Ltd.’s engineering team. The team gives expert advice and quick answers for all pipe bending questions.
Note: For more info or a price quote, visit AFI Industrial Co., Ltd.’s website or contact their support team.