You want the best way for your intricately designed shapes project. Achieve the better result you want. Metal Stamping is good for making many parts. Stamping costs more at the start but makes shapes quickly. Sheet metal fabrication is better for small jobs. You get more choices and pay less at the start. At AFI Industrial, you get live updates and quality checks. Systems watch how long things take and how much they cost. This information helps you choose the best and cheapest way.
Table of Contents
Key Takeaways
- Metal stamping is good for big projects with many parts. It makes parts fast and costs less for each part after setup.
- Sheet metal fabrication is better for small jobs or custom work. It is easy to change designs and costs less to start.
- Metal stamping needs costly dies and takes longer to set up. But it makes the same parts quickly, and every part looks the same.
- Sheet metal fabrication can start fast and does not need special tools. But making each part takes more time.
- You can use many types of metals in fabrication. Stamping works best with metals that bend and cut easily.
- Both methods have strong quality checks. These checks help find problems early and make sure parts are good.
- Use stamping if your design will not change and you need many parts. Use fabrication if you want to change designs or need only a few parts.
- Using both methods together can save money and give more choices. Stamping can make shapes, and fabrication can help put parts together.
Metal Stamping
Overview
You want a process that is fast and reliable. Sheet Metal Stamping gives you both. This method uses dies and presses to shape flat metal sheets. Many industries use Metal Stamping because it makes lots of parts quickly. When you make many parts, the cost for each one is low. In 2024, the world market for Metal Stamping was USD 220.2 billion. In 2023, the automotive sector made up more than 34% of the money earned. Asia Pacific has the biggest market size. North America is growing the fastest. You can find Metal Stamping in aerospace, electronics, and industrial machines. This process does not waste much material. It is also good at saving money. Blanking is a main part of Metal Stamping. It makes up over 32% of the money earned and is growing fast. Automation and robots help make things faster and lower labor costs.
Market Trends:
- Cars and trucks need more stamped parts.
- Planes need parts that are light and strong.
- Factories and telecom use more stamped parts.
- Prices for raw materials can change fast.
- New ways to make parts are coming with additive manufacturing.
Process Steps
Die and Tooling
First, you need a die to shape the metal. Tooling means the die and other parts that help cut and guide the sheet. You must pay for tooling before you start making parts. This step takes time and money, but it helps when you make many parts. The die must match the shape and size of your part. Progressive dies are for complex shapes. Compound dies are for simple cuts.
Press Operation
You put the metal sheet in the press. The press pushes the die into the metal. This shapes the metal in one quick move. Some presses can make up to 1,500 parts every hour with progressive dies. The blanking process uses a punch that works very fast. It lasts only 3.3 milliseconds at 500 strokes per minute. Each stroke takes about 0.024 seconds. This gives you fast cycles and high output. Sensors watch every stroke and collect lots of data to check for mistakes.
Stamping Types
You can pick from different stamping types:
- Progressive Die Stamping: The metal moves through stations. Each station makes a cut or bend. You can make up to 1,500 parts per hour.
- Compound Die Stamping: Cuts and shapes the part in one press. You can make over 1,000 parts per hour.
- Transfer Stamping: Moves the part from one station to another for each step.
- Blanking: Cuts flat shapes from the sheet. This is the fastest and makes up 41.5% of the market.
Stamping Method | Production Rate (parts/hour) | Key Advantage for High-Volume Production |
---|---|---|
Progressive Die | Up to 1500 | Makes lots of parts fast with automation |
Compound Die | Over 1000 | Stamps quickly with many steps at once |
Unibody Vehicle Body | N/A | Fast cycles and low costs for big jobs |
Materials Used
You can use many metals in Metal Stamping. The most common are mild steel, aluminum, and copper. Each metal has its own thickness and needs a certain force.
Material | Thickness (mm) | Tonnage per mm² (tons) | Clearance (%) |
---|---|---|---|
Mild Steel | 0.5 – 1.0 | 30 – 40 | 10 – 15 |
Aluminum | 1.0 – 2.5 | 15 – 22 | 12 – 18 |
Copper | 0.8 – 1.8 | 22 – 28 | 8 – 12 |
You pick the metal based on what your part needs. The right metal helps the process go well and makes sure your parts are of good quality.
Applications
You want your parts to fit many uses. Metal Stamping helps you reach many industries. You can see stamped parts in cars, planes, electronics, and buildings. This process gives you the speed and scale you need for big projects.
- The global metal stamping market reached about USD 195.8 billion in 2023. Experts expect it to grow to USD 289.4 billion by 2033.
- You find stamped parts in car bodies, chassis, doors, and engines. The automotive industry uses the most stamped parts.
- Aerospace companies use stamped parts for airframes, engines, and other key parts. These parts must be light and strong.
- Electronics makers use stamped parts for connectors, cases, and switches.
- Construction companies use stamped metal for beams, panels, and brackets.
- Asia Pacific leads the market, with China, Japan, and India making many stamped parts.
- The rise of electric vehicles increases the need for lightweight stamped parts.
- Mechanical presses and bending processes are the most common in this field.
- Companies like Magna International, Gestamp, and Ford Motor Company lead the market.
Tip: If you want to serve the automotive or aerospace sector, you need a process that can make many parts fast and keep costs low. Metal Stamping gives you this edge.
Product Quality
You want every part to meet your standards. Metal Stamping uses many checks to help you get the right result. You see inspections before, during, and after production. You get real-time data from sensors and machines. This data helps you spot problems early.
Quality teams use tools like laser scanners and coordinate measuring machines. They compare each part to the design. You get tests for strength, hardness, and corrosion. These steps help you avoid mistakes and keep your parts in line with ISO standards. If you work in cars, you need parts that pass tests for impact and fatigue. If you make electronics, you need parts that fit tight spaces and resist heat. Aerospace needs parts that hold up under stress and do not rust.
You can see the difference between a qualified and an unqualified stamped part. A qualified part has smooth edges, the right size, and no cracks. An unqualified part may have rough edges, the wrong size, or surface flaws.
Note: You lower your risk of defects when you use a process with strong quality checks. Metal Stamping gives you this control.
Sheet Metal Fabrication
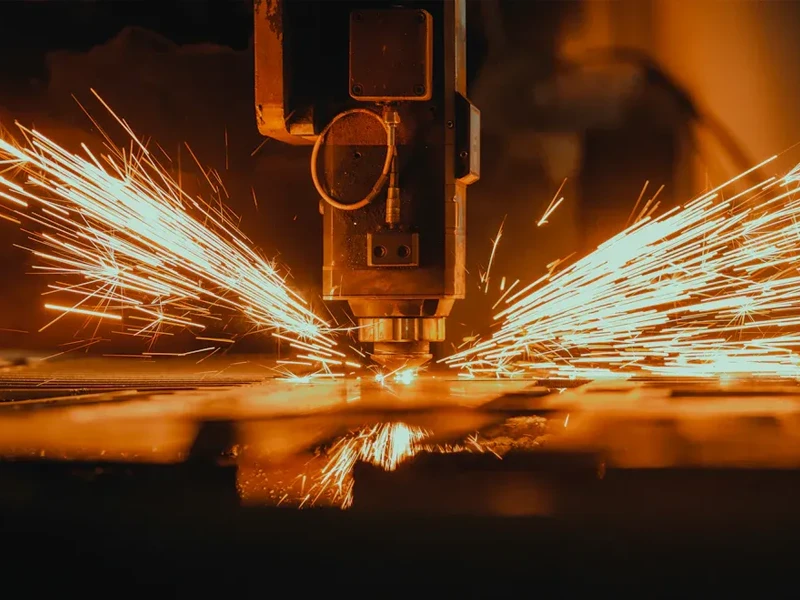
Overview
You want a process that lets you change things easily. Sheet metal fabrication helps you shape, cut, and join metal sheets. You can use it for small or big jobs. Many industries use this method, like construction, cars, planes, and engineering. You can change your design at any time. This helps you react quickly if something changes.
Aspect | Statistic / Trend |
---|---|
Automotive Production | Global car making went up 10.3% from 2022 to 2023. This makes more need for sheet metal fabrication. |
Automation Adoption | More CNC machines, robotic welding, and laser cutting are used now. |
Fastest Growth Segments | Laser cutting, aluminum, enclosures, and low-volume jobs are growing fastest. |
Regional Growth | North America makes the most money in 2024. Asia-Pacific is growing the fastest. |
Industry Segments | Cars use the most in 2024. Electronics will grow fastest from 2025 to 2032. |
Process Segments | Stamping is biggest in 2024. Laser cutting will grow fastest through 2032. |
Material Segments | Steel is used most (60.5% in 2024). Aluminum will grow fastest from 2025 to 2032. |
Application Segments | Structural parts are biggest in 2024. Enclosures will grow fastest from 2025 to 2032. |
Volume Segments | High-volume jobs are biggest in 2024. Low-volume jobs will grow fastest from 2025 to 2032. |
Challenges | It costs a lot to start. There are not enough skilled workers. |
Sheet metal fabrication keeps up with new trends. Automation and robots help save time and stop mistakes. You can use this process for both big and small orders.
Fabrication Steps
Cutting
First, you cut metal sheets to the size you need. You can use laser cutting, water jet cutting, or shearing. Laser cutting is getting more popular. It gives smooth edges and works with many metals. Cutting services made up 25.1% of the market in 2024. You can pick standard sheet sizes like 3m x 1.5m or 4m x 2m. This helps you waste less and save money.
- Lean manufacturing means you only cut what you need.
- Just In Time (JIT) production helps you get parts faster.
- Machine utilization rate shows how well you use your machines.
Bending
Next, you bend the cut pieces into the shapes you want. You use press brakes or rollers for this step. Good bending saves time and money. You can make simple or tricky bends, depending on your design. First-pass yield tells you how many parts are bent right the first time.
- Bending makes your parts stronger.
- You can change bends for different jobs.
- Quality checks help you catch mistakes early.
Assembly
You put the bent and cut pieces together to finish the product. You can use welding, riveting, or bolting. Robotic welding is common for big jobs. It saves work and makes strong joints. On-time delivery and order accuracy show how good your assembly is.
- The assembly puts all the parts together.
- Modular designs help you work faster.
- Always improving helps you waste less and fix fewer mistakes.
Materials Used
You can choose from many metals for your project. Steel is the most common and cheapest. Aluminum is lighter and does not rust, but costs more. Stainless steel does not rust and looks nice. Copper costs a lot but carries electricity well. You pick the metal based on what you need and how much you can spend.
Metal Type | Cost per Square Foot (USD) | Cost per Sheet (USD) |
---|---|---|
Copper | $25–$45 | $2,100–$4,400 |
Tin | $11–$28 | $1,200–$2,650 |
Zinc | $6–$21 | $1,555–$2,400 |
Stainless Steel | $8–$19 | $710–$2,100 |
Aluminum | $7.50–$23 | $675–$2,200 |
Galvanized Steel | $4.75–$19 | $465–$1,600 |
Galvalume Steel | $4–$7 | $390–$950 |
You can save money by picking the right metal and sheet size. Early choices in design change your final cost. Good cutting, bending, and assembly help you stay on budget and finish on time.
You want every part to be good. Checking quality at each step helps you avoid bad parts and get the results you want.
Applications
You want your parts to fit many jobs. Sheet metal fabrication helps you do this. You can make car bodies, airplane parts, and building frames. You can also make cases for electronics. You can create special parts for unique projects. Many industries use sheet metal fabrication. It lets you pick the best metal, shape, and way to join parts.
Category | Details |
---|---|
Materials | Steel, Aluminum, Copper, Magnesium, Brass, Titanium |
Cutting Methods | Laser cutting, Plasma cutting, Shearing |
Forming Methods | Bending, Stamping |
Joining Methods | Welding, Riveting |
Applications | Car bodies, custom auto parts, vintage car restoration |
Industry Demand | Automotive, aerospace, construction, electronics |
Customization | Custom parts for looks and function, CNC machining for repeatability |
Lightweight Focus | Aluminum and magnesium for lighter vehicles |
Each industry uses sheet metal fabrication in its way:
End-User Industries | Role of Sheet Metal Fabrication |
---|---|
Automotive | Body panels, frames, engine parts |
Aerospace | Aircraft components |
Construction | Roofing, cladding, structural elements |
Electronics | Enclosures, device chassis |
You can pick steel for strong parts. Aluminum is good if you want less weight. Copper works well for electrical jobs. Laser cutting gives smooth edges. Plasma cutting works for thick metal. You can bend metal to make shapes. Welding joins pieces together. You can make one part or many. You can change your design whenever you want.
You get more control over your work. You can meet the needs of cars, planes, buildings, and devices. You can also make parts that match your own ideas.
Product Quality
You want every part to be of good quality. Sheet metal fabrication uses many checks to help you. You get tests for strength, toughness, and surface finish. You also check each step as you go.
- Hardness tests show how well your part resists wear.
- Tensile tests show how much force your part can take.
- Impact tests show how much energy your part can handle before it cracks.
- Visual checks look for cracks, pits, and color changes.
- You get records and certificates for each part.
You can use both people and computers to check parts. You can find problems early and fix them fast. Lean methods and Six Sigma help you keep getting better. Sampling and process control help you keep your parts on target.
You lower your risk of bad parts with strong checks. You get parts that pass tests and work as planned. You can trust your parts to do their job.
Comparison
Volume
You want to choose the right process for your production needs. If you need thousands or millions of parts, Metal Stamping gives you the best results. This process uses automated presses and dies. You can make many parts in a short time. The cost per part drops as you make more. You get the same shape and size every time.
Sheet metal fabrication works better for small batches. You can change your design without much trouble. You do not need to make expensive dies. If you only need a few parts, you save money and time. You can also make custom parts for special jobs.
Production Volume | Metal Stamping | Sheet Metal Fabrication |
---|---|---|
High (10,000+ parts) | Best choice | Not cost-effective |
Medium (1,000–10,000) | Good if design is stable | Flexible for changes |
Low (1–1,000) | Too costly | Best choice |
If you want to make many parts, pick Metal Stamping. If you want to make a few, pick sheet metal fabrication.
Cost
You care about cost. Metal Stamping needs a big investment at the start. You pay for strong dies and setup. When you make many parts, the cost per part drops. You save money as you make more. Automation lowers labor costs.
Sheet metal fabrication has lower startup costs. You do not need special dies. You pay more for each part, but you save if you only need a few. Labor costs are higher because people do more of the work. You can change your design without spending much.
A study in 2024 shows that incremental sheet forming, a type of sheet metal fabrication, costs less for small jobs. You do not pay for expensive dies. You get more design choices. Metal Stamping wins on cost when you make many parts. Sheet metal fabrication wins when you make a few.
Factor | Metal Stamping (High Volume) | Sheet Metal Fabrication (Low Volume) |
---|---|---|
Cost per Unit | Lower due to economies of scale; tooling costs spread over many units | Higher due to less tooling cost dispersion over fewer units |
Tooling Costs | High upfront tooling costs for robust, long-lasting tools | Lower tooling costs with simpler or less robust tools |
Material Efficiency | Improved through bulk purchasing and waste reduction | Less optimized material use; higher material cost per unit |
Labor Costs | Reduced by automation producing standardized parts | Higher due to reliance on manual labor |
Setup and Changeover Time | Cost impact reduced by producing many parts with minimal changeovers | Higher cost impact due to fewer units sharing setup time |
Tooling Cost Increase for Complex Geometries | Tooling costs can increase by 15-30% due to precision and complexity | Generally lower tooling complexity and cost |
Production Volume Suitability | More cost-efficient at high volumes due to tooling amortization and automation | More cost-effective for low-volume, customized production due to lower upfront tooling investment |
You save money with Metal Stamping for big jobs. You save money with sheet metal fabrication for small jobs.
Lead Time
You want your parts fast. Metal Stamping takes time to set up. You must design and build the die. This can take weeks. Once you finish the setup, you get parts quickly. The press makes many parts every hour. You get short production times for big orders.
Sheet metal fabrication starts faster. You do not need to wait for a die. You can cut, bend, and assemble right away. This works well for rush jobs or when you need to change your design. You get your first parts sooner, but each part takes longer to make.
- Metal Stamping: Long setup, fast production.
- Sheet Metal Fabrication: Short setup, slower production.
If you need many parts and can wait for setup, choose Metal Stamping. If you need parts now or want to change your design, choose sheet metal fabrication.
Design Complexity
You want to make parts with shapes that fit your needs. Sheet metal fabrication lets you create parts with holes, bends, and cutouts. You can change your design at any time. You do not need to buy new tools for each change. You can make one part or many. You can use machines like lasers and press brakes to shape the metal.
Stamping uses dies to make parts. You need to build a die for each shape. If you want a new shape, you must make a new die. This takes time and money. Stamping works best when you make the same part many times. You get the same shape every time.
Method | Design Change | Setup Needed | Best Use Case |
---|---|---|---|
Sheet Metal Fabrication | Easy | Low | Custom or new designs |
Stamping | Hard | High | Repeat shapes |
You can pick sheet metal fabrication if you want to change your design often. You can pick stamping if you want to make the same part many times.
Customization
You want parts that match your needs. Sheet metal fabrication gives you this choice. You can make parts with special holes, bends, or shapes. You can make one part or many. You do not need to wait for new tools. You can change your order at any time.
Stamping works best for parts that do not change. You need a die for each shape. If you want a new part, you must make a new die. This costs money and takes time. Stamping does not work well for custom jobs.
Benefits of Sheet Metal Fabrication for Customization:
- You can order one part or many.
- You can change your design fast.
- You can use many metals.
When to Choose Stamping:
- You want the same part every time.
- You need many parts.
Material Suitability
You want to pick the right metal for your job. Sheet metal fabrication lets you use many metals. You can use steel, aluminum, copper, or stainless steel. You can pick the thickness you need. You can use the same machines for different metals.
Stamping works best with metals that bend and cut well. You must pick a metal that matches the die. Some metals wear out the die fast. You may need to buy a new die for hard metals. Stamping works best with steel and aluminum.
Method | Metals You Can Use | Tool Wear | Change Metal Easily |
---|---|---|---|
Sheet Metal Fabrication | Many | Low | Yes |
Stamping | Some | High | No |
You can use sheet metal fabrication if you want to try new metals. You can use stamping if you use the same metal every time.
Quality Control
You want every part to meet your needs. Quality control helps you get the right results. You can use different checks for each process.
Metal Stamping Quality Control
You get checks at every step. Machines use sensors to watch each press. You see data for every part. You can spot mistakes fast. You use laser scanners to check size. You use hardness tests to check strength. You get reports for each batch. You can trust the process for big jobs.
Sheet Metal Fabrication Quality Control
You check each step as you go. You use visual checks to find cracks or pits. You use machines to test strength. You can change your process if you find a problem. You get more control for small jobs. You can fix mistakes before you finish the part.
What You Get
You want to see the difference between the good and the bad parts. You can use pictures to help you know what to look for.
You lower your risk when you use strong checks. You get parts that work as planned. You avoid waste and save money.
Quick Comparison Table
Feature | Metal Stamping Quality Control | Sheet Metal Fabrication Quality Control |
---|---|---|
Checks per Step | Sensors and machines | Visual and machine checks |
Data Collection | Real-time | Batch or manual |
Fixing Mistakes | After batch | During process |
Best for | Big jobs | Small jobs |
You want to choose the process that gives you the best control. You get strong checks with both methods. You pick the one that fits your job.
How to Choose
Decision Factors
You want to make the right choice for your project. You need a clear guide that helps you decide. Use this checklist to match your needs with the best process:
Decision Factor | Stamping | Sheet Metal Fabrication |
---|---|---|
Break-even Volume | 10,000+ units | 1–1,000 units |
Per-part Cost | $0.15 (e.g., bracket) | Up to $85 (e.g., custom part) |
Lead Time | 8–12 weeks (with tooling) | 24–72 hours (digital workflow) |
Material Utilization | 85% | 93% (with AI nesting) |
Checklist for Your Project:
- Do you need more than 10,000 parts?
- Do you need fewer than 1,000 parts or prototypes?
- Choose sheet metal fabrication.
- Is your budget tight for startup costs?
- Choose sheet metal fabrication.
- Do you want the lowest cost per part for large runs?
- Choose stamping.
- Do you need parts fast, with little setup?
- Choose sheet metal fabrication.
- Do you want to change your design often?
- Choose sheet metal fabrication.
- Do you need tight tolerances and repeatable shapes?
- Choose stamping.
Tip: If you want to combine both methods, you can use stamping for complex features and fabrication for final touches or assembly.
Industry Use Cases
You can see how real companies make these choices. In the heavy-vehicle industry, two projects switched from old production systems to new multi-product systems. The results showed more flexibility, lower labor cost per output, and higher productivity. The assembly area also became smaller. Over two years, teams collected data from workshops, meetings, and interviews. They also used company documents. These steps gave clear rules and outcomes for picking the right process. The numbers showed that using the right method improved production and saved money.
You can use the same approach. Look at your project needs, collect data, and measure results. You will see better output and lower costs when you match your process to your goals.
You can trust these steps to help you choose. Use the checklist, look at your needs, and pick the process that fits your project.
Materials and Quality
Common Metals
You need to pick the right metal for your job. Steel, aluminum, and copper are used the most in fabrication. These metals are found in cars, buildings, and machines. Steel is popular because it is strong and easy to weld. Aluminum is light and does not rust. Copper is good for carrying electricity.
Metal | Main Use | Market Share/Value (2024) | Key Industry |
---|---|---|---|
Steel | Frames, beams, panels | $18.8B (North America) | Construction |
Aluminum | Auto, aerospace parts | $177.28B (Global casting market) | Automotive, Aerospace |
Copper | Electrical components | Included in global market | Electronics |
Over 1.4 million people work with these metals in fabrication. Welders and machinists use them every day. The United States leads the world in casting, so you can trust these materials.
Qualified vs. Unqualified
You want every part to pass all checks. You need to know what makes a part good or bad. Factories check each step to make sure parts are right. They look at how smooth the surface is, if the size is correct, and if the part is strong.
Surface Finish
You look at the surface of each part. Tools like profilometers help you measure if it is smooth. You follow rules like ASME B46.1. A smooth surface helps the part work better. If the surface is rough or bumpy, the part is not good.
Surface Finish Metric | Standard Used | Typical Range (Ra) | Tool Used |
---|---|---|---|
Roughness | ASME B46.1 | 32-125 microinches | Profilometer |
A good finish makes your parts look and work better. It also helps stop rust and makes sure parts fit together.
Accuracy
You measure each part to check if it fits right. You use calipers, micrometers, and CMMs for this. You follow ISO 2768 and use CAD drawings. If a part does not match the drawing, it is not good.
Quality Metric | Description | Tool Used |
---|---|---|
Dimensional Accuracy | Matches drawing and CAD model | Caliper, CMM |
Tolerance Representation | Uses GD&T for fit and function | CAD, Inspection |
Keeping parts accurate means less waste and less fixing. Every part will fit with others as planned.
Integrity
You check if the part is strong and the welds are good. You follow ISO 3834 for welding. You look for cracks or bad welds. You use both your eyes and tests to check. You use IQC and AQL to see if a batch is good.
- Problems happen if welders do not follow the plan.
- You might see cracks or missing welds.
- You can stop these problems with good training and checks.
- OEE and capacity utilization help you watch your process.
You get safe and strong parts when you use good materials and skilled workers. This helps you avoid mistakes and keeps your project moving forward.
Case Studies
Automotive
You want to know how these methods help car makers. Many companies use metal stamping and sheet metal fabrication to make more cars. In Europe, the ULCOS program started in 2004. This program helped cut carbon pollution by almost half. In Japan, the COURSE50 project began in 2008. It worked to lower CO2 from making steel. In the USA, companies have used less energy since 1990. They cut energy use by 30%. In China, new machines and better plants made steel production about 30% more efficient.
Region/Country | Program/Project | Documented Improvement | Timeframe/Notes |
---|---|---|---|
Europe | ULCOS programme | Nearly 50% reduction in carbon intensity | Started 2004 |
Japan | COURSE50 project | CO2 reduction in steelmaking | Started 2008 |
USA | Various measures | 30% reduction in energy intensity | Since 1990 |
China | Facility upgrades | ~30% improvement in steel production efficiency | Past decades |
Car factories now use less energy and make more parts. This means lower costs and faster shipping. These changes also help the planet by cutting pollution.
You can trust these ways to give you strong car parts.
Electronics
You want faster work and fewer mistakes in electronics. Companies using precision sheet metal fabrication see big improvements. Cycle times drop from 45 minutes to 30 minutes. Defects go down from 10% to 5%. Documentation mistakes drop from 5% to 1.5%.
Metric | Before Implementation | After Implementation |
---|---|---|
Cycle Time (min) | 45 | 30 |
Defect Rate (%) | 10 | 5 |
Documentation Error Rate (%) | 5 | 1.5 |
You also get:
- ROI of 289%
- 84% success with new systems
- 67% faster paperwork
- 24% more worker productivity
- 41% faster problem solving
- 35% better training
- 72% fewer data entry mistakes
You can use tools like Statistical Process Control and Cpk to check quality. You can find problems early and fix them fast. This helps you get almost perfect parts and high output.
You can count on these results to help your electronics projects.
Industrial
You want to save money and make your factory better. Companies like Intel, Caterpillar, and John Deere made big changes. Intel cut cycle times by 35% and made 7% more products. Caterpillar saved 13.4% in costs over three years. John Deere cut inventory by 85% and lead time by 60%. Siemens made products faster, from 12 days to 3 days, and raised output by 35%.
Company / Source | Improvement Area | Quantified Improvement(s) |
---|---|---|
Intel Corporation | Cycle time reduction | 35% reduction in cycle times |
Caterpillar Inc. | Manufacturing costs | 13.4% reduction over 3 years (~$2 billion savings) |
John Deere | Inventory reduction | 85% reduction |
Siemens AG | Production cycle time | Reduced from 12 days to 3 days |
American Society for Quality | Defect rates | 27% reduction |
A two-wheeler company in India used quality tools and digital data. This saved $2.2 million each year. The company spent less on scrap, tools, and supplies. You can use these steps to get cleaner work and better results.
You can get these savings and better results by picking the right process.
Key Differences
You want to choose the best way for your project. Each method has things that make it special. The table below helps you compare them. It shows the main points for both methods.
Aspect | Metal Stamping | Precision Sheet Metal Fabrication |
---|---|---|
Production Volume | Cost-effective for mid-to-high volume production | More economical for short runs and prototyping |
Throughput | Much higher throughput for large quantities | Slower production process |
Automation | Highly automated, reduces labor costs | More labor-intensive, higher labor costs |
Cost per Unit | Reduced per-unit costs with volume | Higher piece price costs for short runs |
Tooling Costs | High upfront tooling costs | Low tooling costs, easier to implement design changes |
Pre-production Time | Longer due to tooling development | Shorter startup time |
Flexibility | Less flexible, costly to change designs after tooling | Greater flexibility and easier design adjustments |
Scrap Rate | Reduced scrap rate | Potentially higher material waste |
Reliability and Repeatability | High reliability, repeatability, reproducibility | N/A |
Suitability | Best for high-volume, consistent parts | Best for complex, customized, or prototype parts |
One method is better for making lots of the same part. The other is good for small jobs or special parts. If you want to make many parts and save money, pick the first method. If you want to change your design or make only a few, the second method gives you more choices.
Tip: Think about how many parts you need, how fast you need them, and if you might want to change your design. This will help you choose the right way.
You also want your parts to be of good quality. You need to know what a good part looks like. Look at the pictures below. The first picture shows a part that is made well. The second picture shows a part that is not made right.
A good part has smooth edges and the right shape. A bad part might have rough edges or the wrong size. You want every part to be just right for your needs.
Now you know the main differences. Use this guide to help you decide. You will get better results and save money when you pick the best way for your project.
You can now tell how metal stamping and sheet metal fabrication are different. The way you pick depends on what your project needs. Big companies like Netflix and Amazon do not just look at numbers. They use real feedback and try out ideas to make better choices. You can do this too. Follow the guide, talk to people who know a lot, and pick the way that matches your goals. If you want more info or a price, contact us today.
FAQ
You get lower costs per part when you make many parts. Metal stamping uses automation. You save money as your order size grows. This process gives you fast results for big jobs.
You should pick sheet metal fabrication for small orders or custom parts. You can change your design at any time. You do not need to pay for expensive dies.
Yes, you can combine both. Use stamping for high-volume shapes. Use fabrication for assembly or special features. This mix gives you cost savings and flexibility.
You check the surface, size, and strength. A qualified part matches your drawing. You see no cracks or rough edges. You get a part that works as planned.
You use steel and aluminum for both methods. Stamping works best with softer metals. Fabrication lets you use many metals, including copper and stainless steel.
You get your first parts faster with sheet metal fabrication. You do not wait for tooling. Stamping takes longer to start but makes parts quickly after setup.
You use sensors, visual checks, and strength tests. You catch mistakes early. You fix problems before you finish the job. This keeps your parts on target.
Tip: Always ask for quality reports. You see proof that your parts meet your needs.